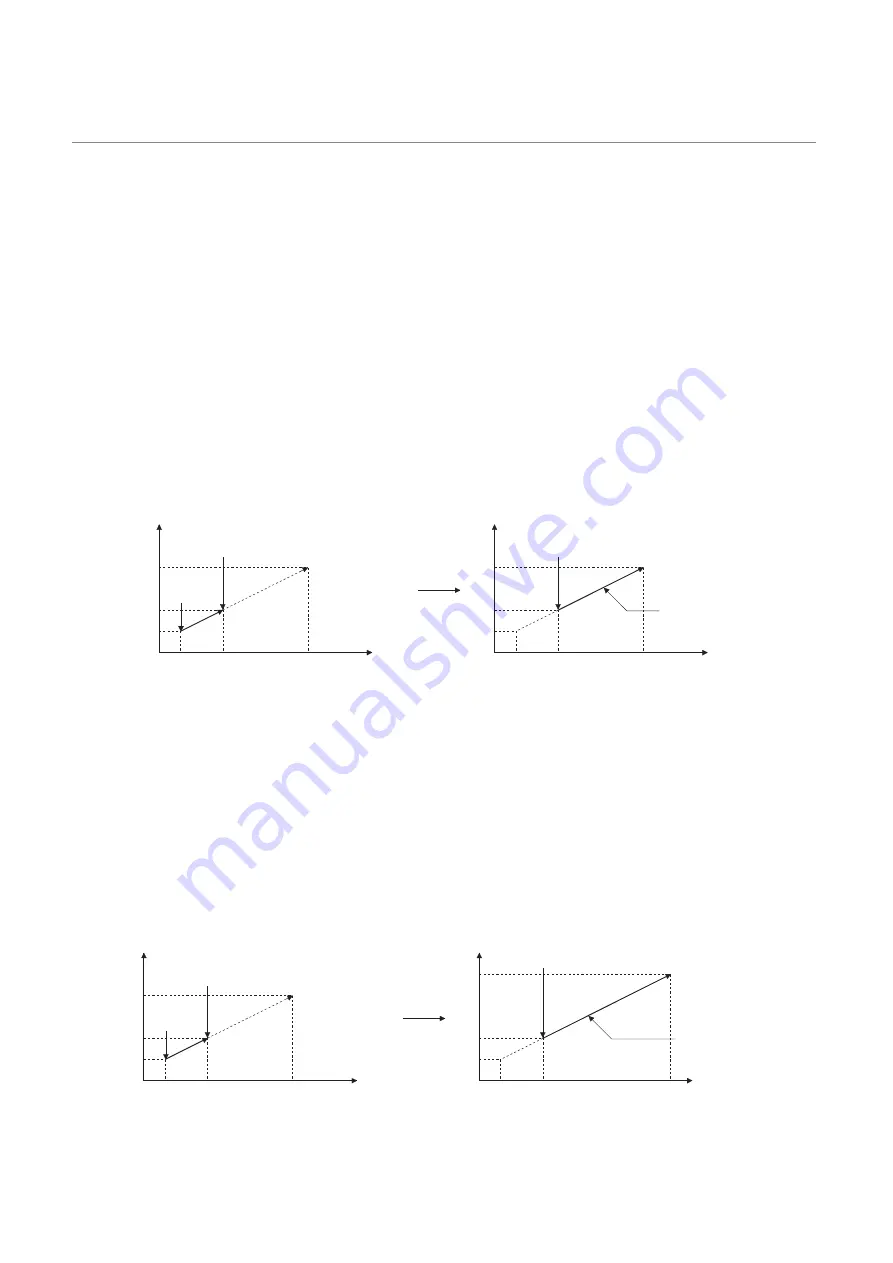
42
1.2.4
Outline of restarting
When a stop cause has occurred during operation with position control causing the axis to stop, positioning to the end
point of the positioning data can be restarted from the stopped position by using the "[Cd.6] Restart command".
If issued during a continuous positioning or continuous path control operation, the restart command will cause the
positioning to be re-executed using the current position (pointed by the positioning data No. associated with the
moment when the movement was interrupted) as the start point.
(1) When "[Cd.6] Restart command" is ON
• If the "[Md.26] Axis operation status" is "Stopped", positioning to the end point of the positioning data will be
restarted from the stopped position regardless of the absolute system or incremental system.
• When "[Md.26] Axis operation status" is not "Stopped", the warning "Restart not possible" (warning code:
104) will be applied, and the restart command will be ignored.
(a) Example for incremental system
The restart operation when the axis 1 movement amount is 300, and the axis 2 movement amount is 600 is
shown below.
(2) Reference
If the positioning start signal [Y10 to Y13]/external command signal
*1
is turned ON while the "[Md.26] Axis
operation status" is "Standby" or "Stopped", positioning will be restarted from the start of the positioning start data
regardless of the absolute system or incremental system.
(Same as normal positioning.)
*1
When the external command signal is set to "External positioning start"
(a) Example for incremental system
The positioning start operation when the axis 1 movement amount is 300 and the axis 2 movement amount is
600 is shown below.
Start point
address
Stop position due to stop cause
Designated end
point position
Axis 1
400
200
100
100
300
700
Axis 2
Stop position due to stop cause
Stop position
after restart
Axis 1
400
200
100
100
300
700
Axis 2
Restart
Operation during
restart
Start point
address
Stop position due to stop cause
Designated end
point position
Axis 1
400
200
100
100
300
700
Axis 2
Stop position due to stop cause
Stop position
after restart
Axis 1
500
200
100
100
300
900
Axis 2
Positioning
start
Operation during
positioning start
Summary of Contents for MELSEC-L LD75D
Page 2: ......
Page 11: ...9 Memo ...
Page 176: ...174 ...
Page 264: ...262 ...
Page 266: ...264 ...
Page 267: ...265 CHAPTER 6 PROGRAM USED FOR POSITIONING CONTROL 6 6 4 Positioning Program Examples ...
Page 268: ...266 ...
Page 269: ...267 CHAPTER 6 PROGRAM USED FOR POSITIONING CONTROL 6 6 4 Positioning Program Examples ...
Page 270: ...268 ...
Page 271: ...269 CHAPTER 6 PROGRAM USED FOR POSITIONING CONTROL 6 6 4 Positioning Program Examples ...
Page 272: ...270 Z ABRST1 instruction execution ...
Page 273: ...271 CHAPTER 6 PROGRAM USED FOR POSITIONING CONTROL 6 6 4 Positioning Program Examples ...
Page 278: ...276 ...
Page 279: ...277 CHAPTER 6 PROGRAM USED FOR POSITIONING CONTROL 6 6 4 Positioning Program Examples ...
Page 280: ...278 ...
Page 281: ...279 CHAPTER 6 PROGRAM USED FOR POSITIONING CONTROL 6 6 4 Positioning Program Examples ...
Page 282: ...280 ...
Page 283: ...281 CHAPTER 6 PROGRAM USED FOR POSITIONING CONTROL 6 6 4 Positioning Program Examples ...
Page 284: ...282 ...
Page 285: ...283 CHAPTER 6 PROGRAM USED FOR POSITIONING CONTROL 6 6 4 Positioning Program Examples ...
Page 286: ...284 ...
Page 287: ...285 CHAPTER 6 PROGRAM USED FOR POSITIONING CONTROL 6 6 4 Positioning Program Examples ...
Page 316: ...314 Memo ...
Page 685: ...683 APPENDICES A Appendix 1 Function Update Appendix 1 1 Function comparison Memo ...
Page 738: ...736 Memo ...
Page 817: ......