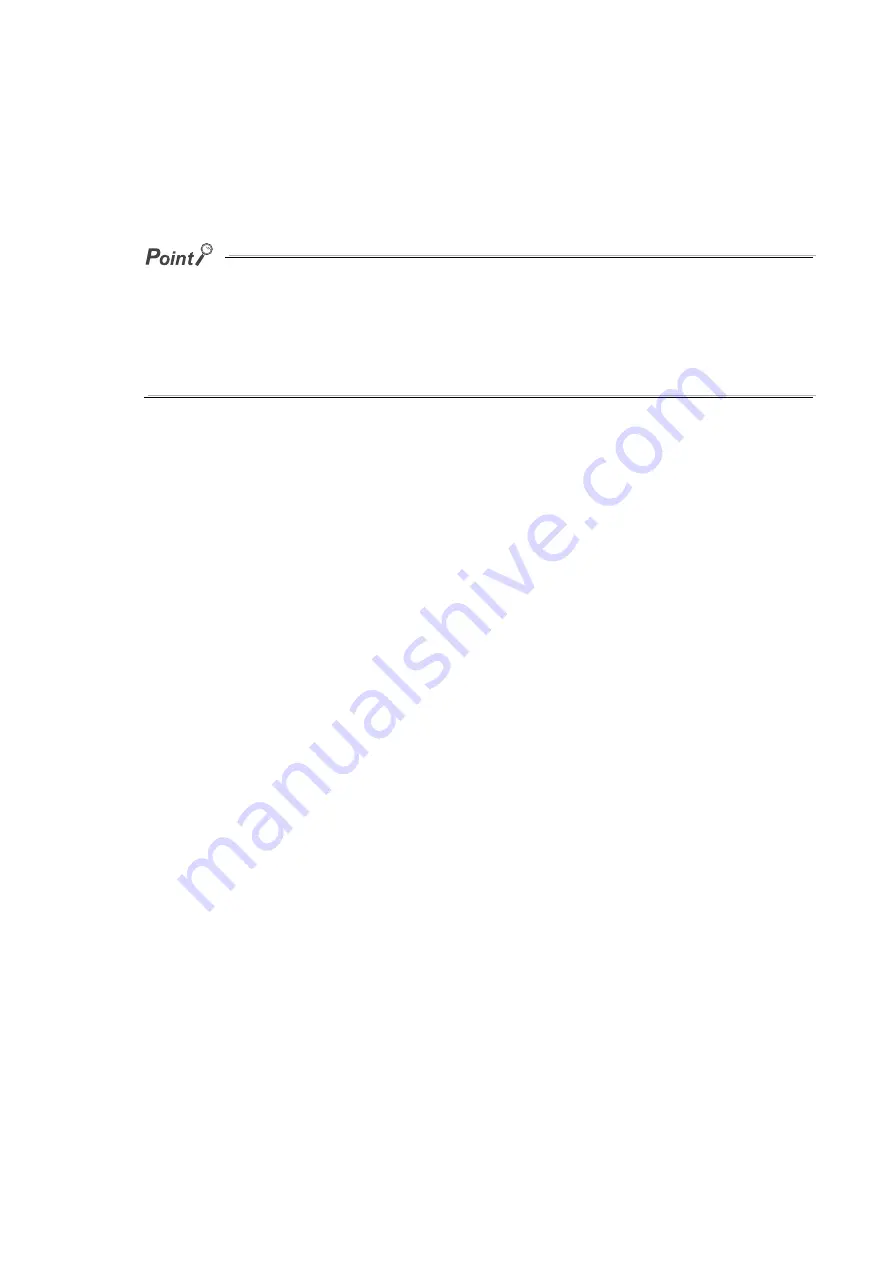
94
(a) Data setting method
The following methods are available for data setting:
• Create the program for data setting using GX Works2 and execute it.
• Set using GX Works2.
In this manual, the method using GX Works2 will be explained.
●
The "setting data" is created for each axis.
●
The "setting data" parameters have determined default values, and are set to the default values before shipment from the
factory. (Parameters related to axes that are not used are left at the default value.)
●
The "setting data" can be initialized with GX Works2 or the program.
●
It is recommended to set the "setting data" with GX Works2. The program for data setting is complicated and many
devices must be used. This will increase the scan time.
(b) Enabling setting data
The basic parameters 1, detailed parameters 1, and OPR parameters become valid when the PLC READY
signal [Y0] turns from OFF to ON. Note, however, that the only valid value of the "[Pr.5] Pulse output mode" is
the value at the moment when the PLC READY signal [Y0] turns from OFF to ON for the first time after the
power is switched ON or the CPU module is reset.
Once the PLC READY signal [Y0] has been turned ON, the value will not be reset even if another value is set
to the parameter and the PLC READY signal [Y0] is turned from OFF to ON.
(c) Changing data
Even when the PLC READY signal [Y0] is ON, the values or contents of the following can be changed: basic
parameters 2, detailed parameters 2, positioning data, and block start data.
(d) Valid data
The only valid data assigned to basic parameters 2, detailed parameters 2, positioning data, or block start data
are the data read at the moment when a positioning or JOG operation is started. Once the operation has
started, any modification to the data is ignored.
Exceptionally, however, modifications to the following are valid even when they are made during a positioning
operation: acceleration time 0 to 3, deceleration time 0 to 3, and external start command.
• For acceleration time 0 to 3 and deceleration time 0 to 3, modifications become valid from the data 4 steps
ahead of that in execution by pre-reading and pre-analyzing positioning data.
• For external command function selection, the value at the time of detection is valid.
Summary of Contents for MELSEC-L LD75D
Page 2: ......
Page 11: ...9 Memo ...
Page 176: ...174 ...
Page 264: ...262 ...
Page 266: ...264 ...
Page 267: ...265 CHAPTER 6 PROGRAM USED FOR POSITIONING CONTROL 6 6 4 Positioning Program Examples ...
Page 268: ...266 ...
Page 269: ...267 CHAPTER 6 PROGRAM USED FOR POSITIONING CONTROL 6 6 4 Positioning Program Examples ...
Page 270: ...268 ...
Page 271: ...269 CHAPTER 6 PROGRAM USED FOR POSITIONING CONTROL 6 6 4 Positioning Program Examples ...
Page 272: ...270 Z ABRST1 instruction execution ...
Page 273: ...271 CHAPTER 6 PROGRAM USED FOR POSITIONING CONTROL 6 6 4 Positioning Program Examples ...
Page 278: ...276 ...
Page 279: ...277 CHAPTER 6 PROGRAM USED FOR POSITIONING CONTROL 6 6 4 Positioning Program Examples ...
Page 280: ...278 ...
Page 281: ...279 CHAPTER 6 PROGRAM USED FOR POSITIONING CONTROL 6 6 4 Positioning Program Examples ...
Page 282: ...280 ...
Page 283: ...281 CHAPTER 6 PROGRAM USED FOR POSITIONING CONTROL 6 6 4 Positioning Program Examples ...
Page 284: ...282 ...
Page 285: ...283 CHAPTER 6 PROGRAM USED FOR POSITIONING CONTROL 6 6 4 Positioning Program Examples ...
Page 286: ...284 ...
Page 287: ...285 CHAPTER 6 PROGRAM USED FOR POSITIONING CONTROL 6 6 4 Positioning Program Examples ...
Page 316: ...314 Memo ...
Page 685: ...683 APPENDICES A Appendix 1 Function Update Appendix 1 1 Function comparison Memo ...
Page 738: ...736 Memo ...
Page 817: ......