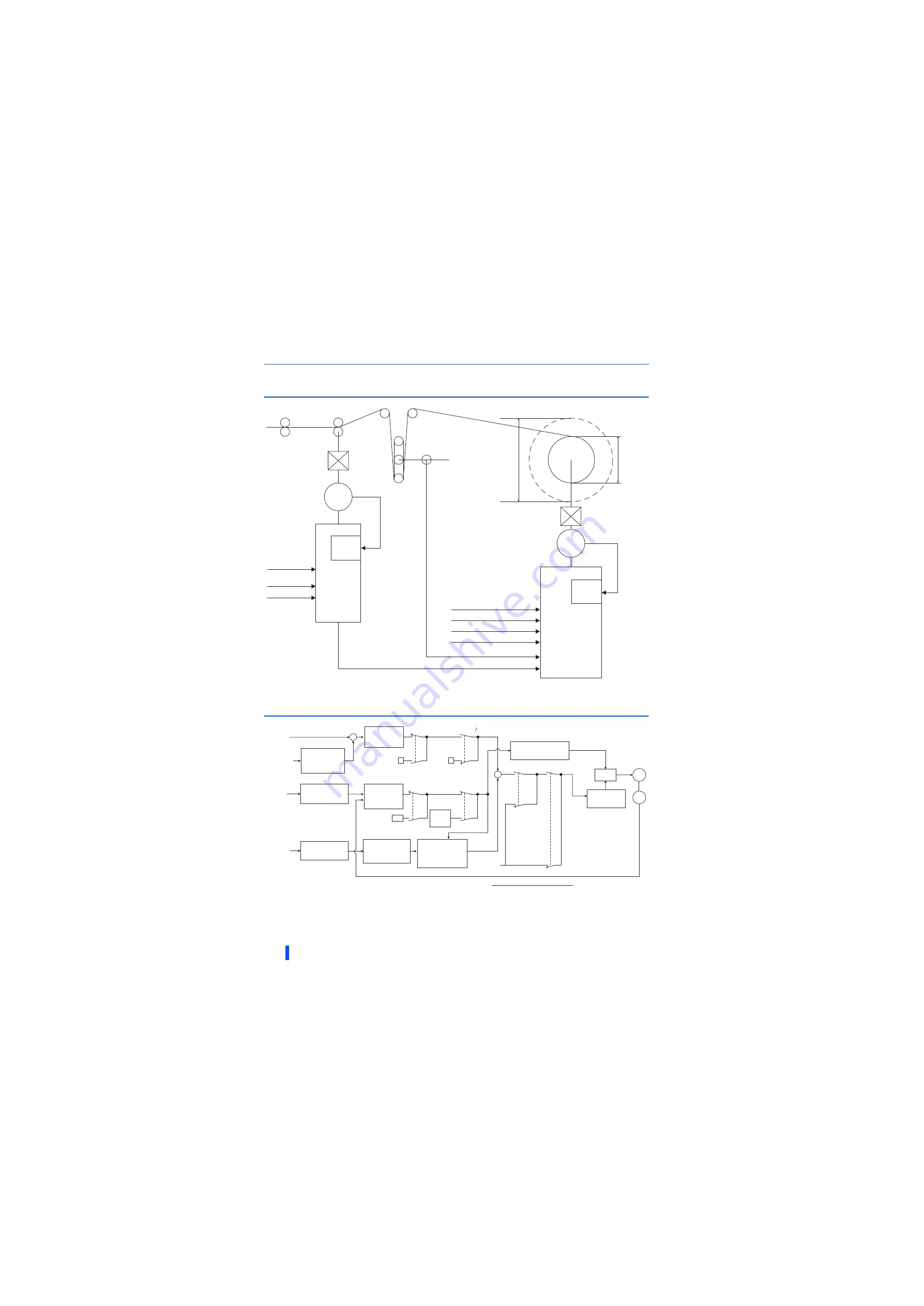
System configuration example
42
3.2
System configuration example
3.3
Control block diagram
FR-A800-R2R
Encoder
Line speed command
Potentiometer
Dancer roll
Dancer signal
Minimum
diameter
Maximum diameter
AM
2
2 (
Pr.361
= 3)
1 (
Pr.363
= 5)
STF/STR
For winding roll (
Pr.1230
= 0)
Start signal
Dancer/tension control selection
X114 (
Pr.180
= 114)
FR-A8AP
Encoder
Line speed
command
Line speed command
FR-A800-R2R
FR-A8AP
M
M
STF/STR
Start signal
Dancer/tension
control selection
X114
X117 (
Pr.182
= 117)
Winding length clear
X109 (
Pr.181
= 109)
Stored winding diameter clear
Winding diameter
compensation
speed generation
Conversion from
line speed to frequency
∗2
After clearing, the value becomes the minimum winding diameter when
Pr.1230
= "0" (winding),
and the maximum winding diameter when
Pr.1230
= "1" (unwinding).
+
-
X116-OFF
X116-ON
X109-OFF
X109-ON
X115-OFF
X115-ON
Held
Winding
diameter
clear
∗2
0
0
+
+
Speed control proportional
gain compensation
Pr.639 to Pr.644
M
Encoder
X114-ON
X114-OFF
Dancer signal /
tension feedback
input selection
Pr.363
PID action
set point
(
Pr.133
)
Dancer
roll position
Actual
line speed
Line speed
command
Actual line speed
input selection
Pr.362
Line speed
command selection
Pr.361
Winding diameter
calculation
Pr.1235, Pr.1236,
Pr.1243, Pr.1244
Line speed command
Acceleration
/deceleration
Pr.394, Pr.395
PID operation
Pr.129, Pr.130,
Pr.134
Pr.363
= 9999
Pr.363
= 9999
Pr.128
= 40, 41
Pr.128
= 0
Winding diameter
compensation
speed
∗1
Winding diameter
Motor speed
Speed
control
Acceleration
/deceleration
Pr.7, Pr.8
= 0
Line speed command
∗1
Winding diameter compensation speed =
π
× Winding diameter × Gear ratio
Frequency
command
Summary of Contents for A800 Plus Series
Page 240: ...239 MEMO ...