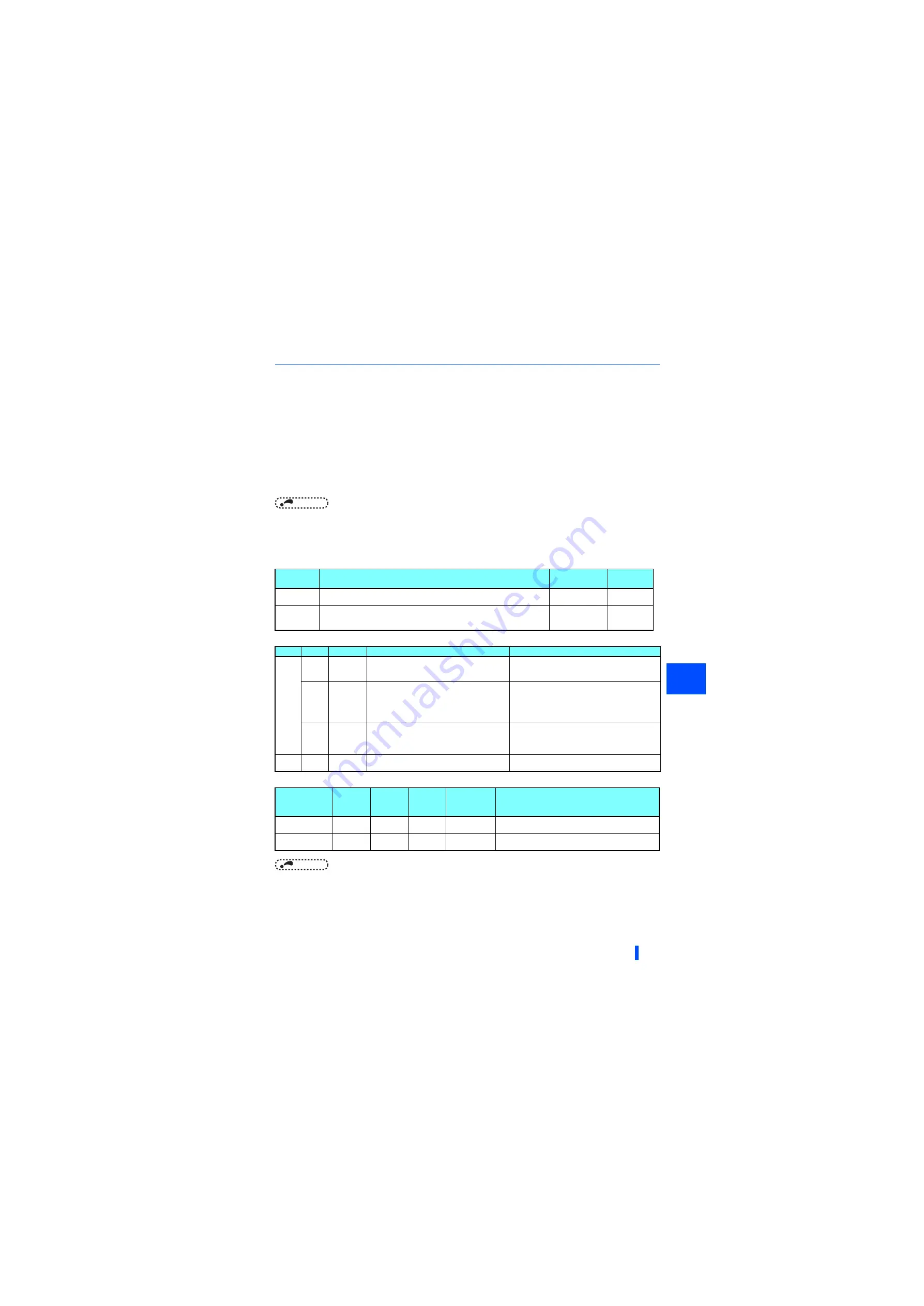
Dancer feedback speed control details
65
3
Line speed command input by parameter setting (Pr.361 = "8")
• The value set in
Pr.360 Line speed command value
is used for the line speed command. (Setting range: 0 to 6553.4 m/
min)
Line speed command input through RS-485/Ethernet or using a
communication option (except for the FR-A8ND)
• Use the read/write procedure for the set frequency to read/write the line speed command value through RS-485 / Ethernet
(CC-Link IE Field Network Basic) or using a communication option (FR-A8NC/FR-A8NCE/FR-A8NP). The frequency set for
normal speed control is used as the line speed command value for dancer feedback speed control. (The setting is used as
the set frequency when the X114 signal is OFF, and used as the line speed command value when the X114 signal is ON.)
• The setting range is H0000 to HFFFE (0 to 6553.4), and the setting increment is 0.1.
NOTE
• For the details of RS-485 communication, refer to the FR-A800 Instruction Manual (Detailed). For the details of CC-Link IE
Field Network Basic, refer to the Ethernet Function Manual. For the details of communication options, refer to the Instruction
Manual of each option.
Line speed command input using the FR-A8ND
• The line speed command value is read/written as follows.
• The line speed command value is written through I/O communication (output instance 127) as follows.
• The message communication (instance 1 in class 0x2A) related to the line speed command value is defined as follows.
NOTE
• Output instances 20, 21, and 126 and input instances 70, 71, and 176 are not available for the line speed command.
Read/write
Reading/writing method for line speed command
Setting range
Setting
increments
Read
• Read the
Pr.360
setting.
H0000 to HFFFE
(0 to 6553.4)
0.1 m/min
Write
• Writing through I/O communication (Output instance 127).
• Write through message communication.
• Write in
Pr.360
.
H0000 to HFFFE
(0 to 6553.4)
0.1 m/min
Byte
Bit
Function
Setting method
Remarks
1
5
Write Attr
0: The values set in bytes 2 and 3 are used as the
speed/frequency setting value.
1: The values set in bytes 2 and 3 are used as the
writing data to the attributes specified in bytes 6 and
7, respectively.
6
Hz
1: 0.01 Hz increment
0: An unexpected value is written. (The value written
in byte 2 and byte 3 is recognized as a number of
rotations. Then, the value is converted into a
frequency value and written as the line speed
command value.)
7
32-bit
format
0: The format for 16-bit data is being selected.
(Bytes 2 and 3 are used.)
1: The format for 32-bit data is being selected.
(Bytes 2 to 5 are used.)
2, 3
—
Speed
setting
The line speed command value is written.
According to the setting of bit 7 in byte 1, the format
is selected for 16-bit data or 32-bit data.
Attribute ID
Access
Data
type
Number
of data
bytes
Range
Description
112
Set
UINT
2
0 to 0xFFFE
(0 to 6553.4)
The line speed command value is written in RAM.
(0.1 increments)
113
Set
UINT
2
0 to 0xFFFE
(0 to 6553.4)
The line speed command value is written in EEPROM.
(0.1 increments)
Summary of Contents for A800 Plus Series
Page 240: ...239 MEMO ...