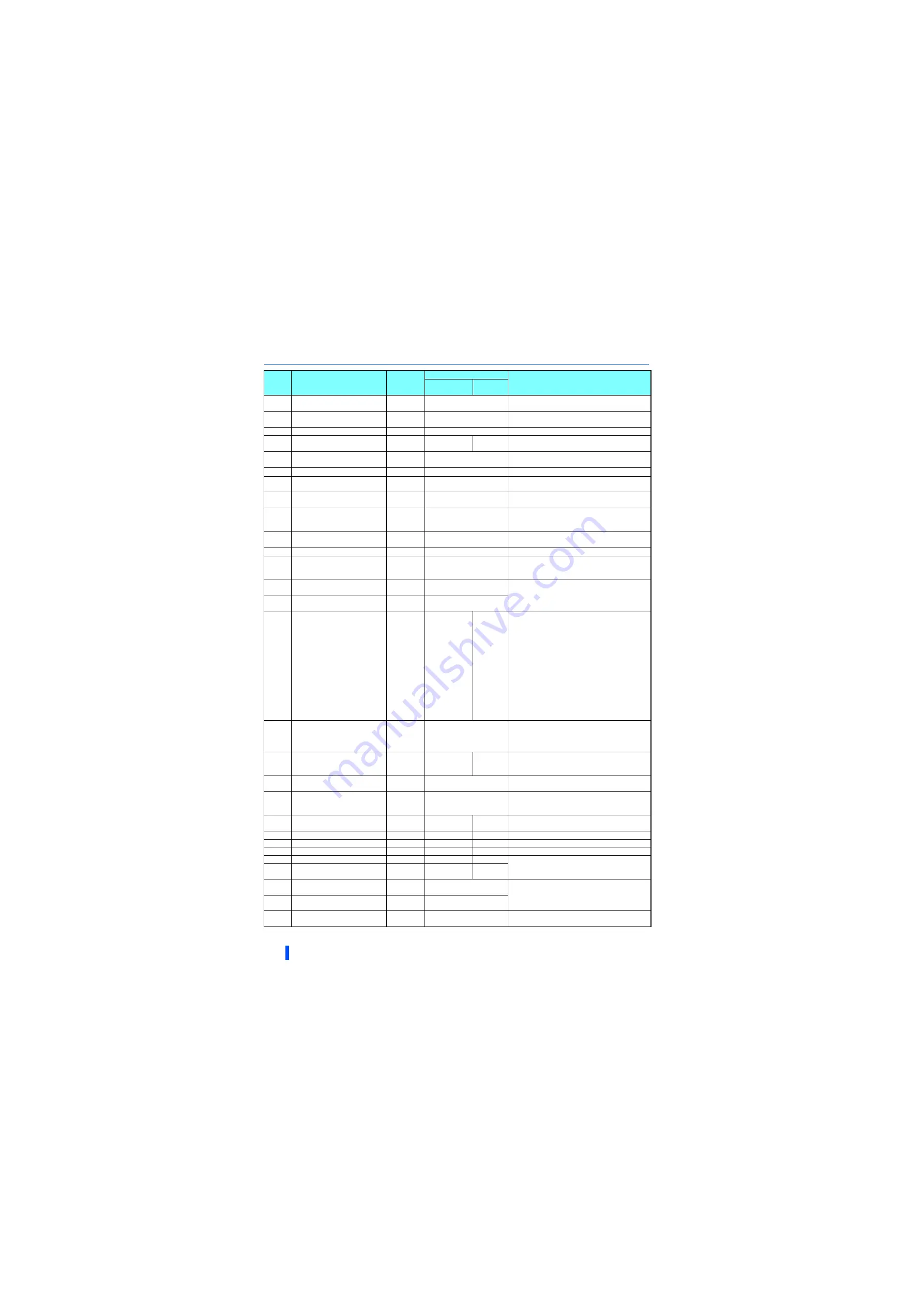
Application examples
210
270
Acceleration/deceleration time
during stall condition
15 s
15 s
Set the acceleration/deceleration time during stall
mode.
350
Line speed command voltage/
current bias
0%
0%
351
Line speed command bias
0 m/min
0 m/min
Use
Pr.358
to set the increment.
352
Line speed command voltage/
current gain
50%
50%
100%
353
Line speed command gain
1000 m/min 400 m/min
Use
Pr.358
to set the increment. Maximum line
speed (400 m/min) is set.
358
Line speed unit
0
0
0: m/min (increment of the maximum line speed)
360
Line speed command value
0 m/min
0 m/min
If setting
Pr.361
to "8", set a line speed command
value in this parameter.
361
Line speed command input
selection
9999
3
3: Input via terminal 2
362
Actual line speed input selection 0
0
0: Signals for the actual line speed are not input
(the actual line speed is determined by calculating
from the line speed setting).
363
Dancer / tension sensor
feedback input selection
9999
9999
Leave the setting "9999 (initial value)" (No
function) since tension feedback is not required.
369
Number of encoder pulses
1024
2048
393
Line speed command
acceleration/deceleration
reference
1000 m/min 250 m/min
The line accelerates to 250 m/min in 5 seconds.
394
First acceleration time for line
speed command
15 s
5 s
Setting must be lower than the acceleration/
deceleration rate of the line speed command
(input via terminals 2 and 5).
395
First deceleration time for line
speed command
15 s
5 s
645
Winding diameter storage
selection
0
0
1
When "1" (storing roll diameters enabled) is set,
the input of the Stored winding diameter clear
(X109) signal is required.
The storing of roll diameters (writing in EEPROM)
is conducted when the inverter power or the X114
signal turns OFF. Note that the storing is not
conducted when the RES signal is input.
Therefore, avoid inputting the RES signal
frequently without storing the roll diameters.
For the input of the RES signal by necessity such
as a reset of the inverter fault, it is recommended
to configure the sequence that the RES signal will
be input after the X114 signal turns OFF and
before the X114 signal turns ON again.
647
Operation time with stored
winding diameter
0 s
0.01 s
Be sure to set this parameter when storing roll
diameters is set to enabled (the value of the
stored roll diameter is not applied to any setting if
this parameter is not set).
800
Control method selection
20
0
2
0: Vector control (speed control)
2: Vector control (switchover between speed
control and torque control)
803
Constant output range torque
characteristic selection
0
0
To limit output torque in the constant power range,
set "1" (constant torque).
804
Tension / Torque command
source selection
0
0
Tension command given by analog input via
terminal 1 on the inverter (0 to ±10 VDC)
or terminal 6 on the FR-A8AZ (0 to ±10 VDC)
807
Speed limit selection
0
0
2
2: Speed limit command given by analog voltage
input via terminal 1
821
Speed control integral time 1
0.333 s
0.333 s
0 s
868
Terminal 1 function assignment
0
0
2
2: Forward/reverse rotation speed limit (
Pr.807
=2)
1230
Winding/unwinding selection
0
1
0
0:Winding, 1: Unwinding
1235
Maximum winding diameter 1
2 mm
80 mm
300 mm
Set the initial roll diameter (the maximum
diameter of an unwinding roll or the minimum
diameter of a winding roll) with high accuracy.
1236
Minimum winding diameter 1
1 mm
80 mm
100 mm
1243
Gear ratio numerator (follower
side)
1
10
Set the gear ratio of the unwinding roller (shaft)
with high accuracy.
1244
Gear ratio denominator (driver
side)
1
12
Sampling time for winding
diameter calculation
9999
0.1
Set a sampling time for the roll diameter
calculation.
Pr.
Parameter name
Initial
value
Setting value
Remarks
Intermediate
roller
Winding
roller
Summary of Contents for A800 Plus Series
Page 240: ...239 MEMO ...