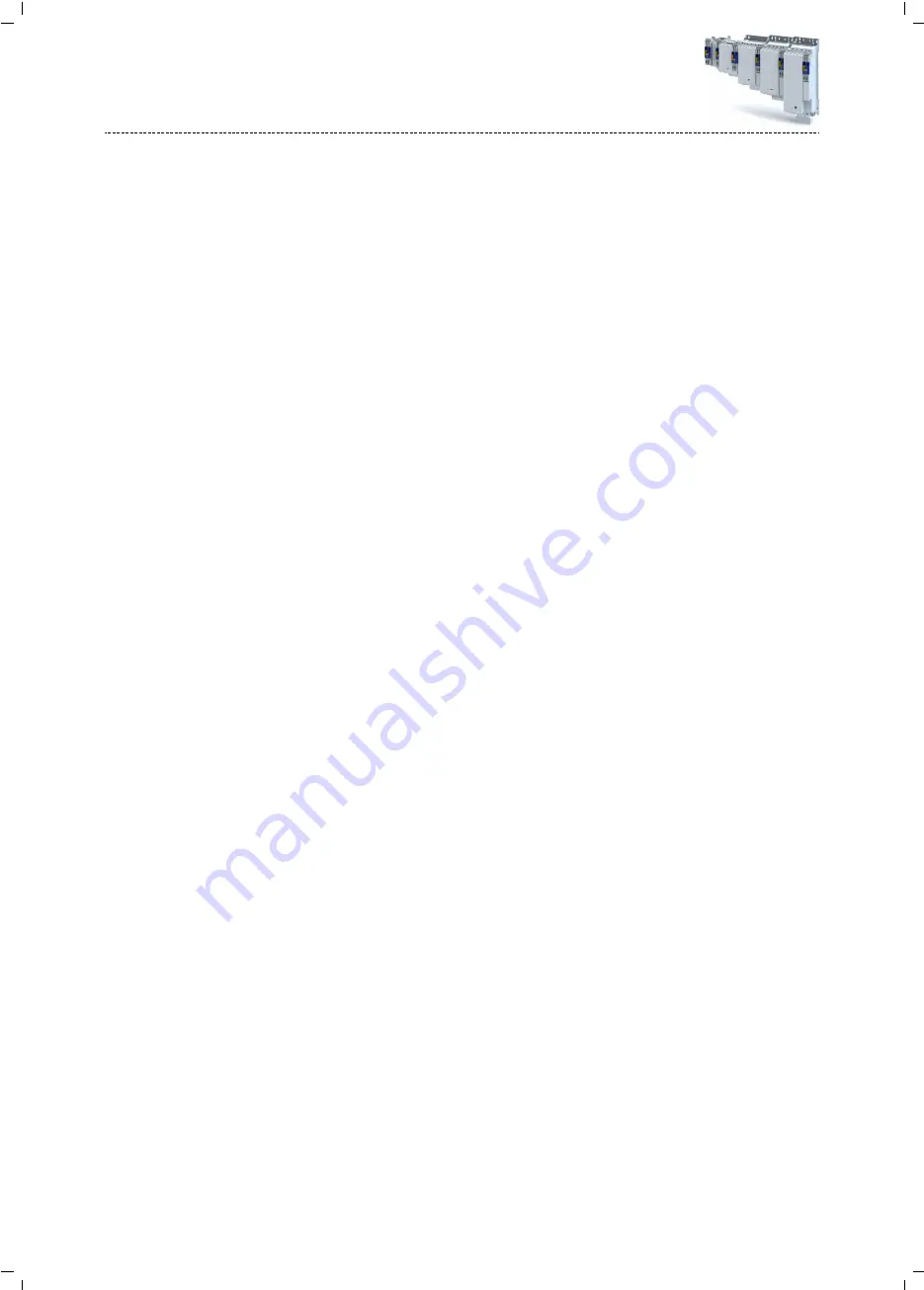
If the servo control is set for synchronous motor and no error is pending, the current is first
raised in a ramp-shaped manner to 141 % of the rated motor current after the inverter is ena-
bled.
Left image
First, the rotor is moved from any position of rest to the 0° angle.
•
For this purpose, the amplitude of the d current vector is created in the stator coordinate
system at a starting angle of 45° and then turned to 0°.
•
A sufficiently high amplitude of the d current vector and its rotary motion result in a mag-
netic force that moves the rotor to the angle 0°.
Right image
Afterwards, the d current vector is turned further in 15 steps by 22.5° each starting at the
angle 0°.
•
Due to the magnetic forces, the rotor adjusts to the respective angle.
•
After 16 steps, the rotor has moved by absolute electrical 360°.
Result
For determining the pole position, a mean value is calculated from all 16 messages. The rotor
displacement angle can be recorded via the 0x2DDE parameter (actual motor rotor angle posi-
tion). The detected pole position is stored in the inverter parameters ,
. The detected pole position must then be saved.
Abort of the pole position identification
The pole position identification is aborted if the deviations between the rotary motion of the
current vector and the rotor exceed the fault tolerance set in
(check if parameter
is available)
.
Preconditions for the performance
•
The motor must not be braked or blocked during the pole position identification.
•
The servo inverter is error-free and in
device state.
Response of the motor during performance
The rotor aligns during the pole position identification. The motor shaft moves by max. one
electrical revolution which causes a corresponding movement of the connected mechanics!
How to execute the pole position identification PLI (360°):
1. If the servo inverter is enabled, disable it.
2. Set the object
to "5" to change to the "pole position identification PLI (360°)" oper-
ating mode.
3. Before the PLI can be started, the works mentioned below must be completed.
4. Enable the servo inverter to start the pole position identification (360°). Note: Inhibiting the
controller serves to abort the started procedure any time if required without changing the
settings.
After the pole position identification has been completed successfully...
...the controller is inhibited automatically and the pole position determined for the activated
feedback system is set in the
object.
•
Save the changed settings.
The »EASY Starter« serves to save the parameter settings of the servo inverter as parame-
ter file (*.gdc).
•
The inverter disable set automatically by the procedure can be deactivated again via the
CiA402 control word
Configuring the feedback system
Synchronous motor: Pole position identification (PPI)
Pole position identification (PPI) 360°
228
Summary of Contents for i950 Series
Page 1: ...Inverters i950 servo inverters Commissioning EN ...
Page 2: ......
Page 497: ......
Page 498: ......
Page 499: ......