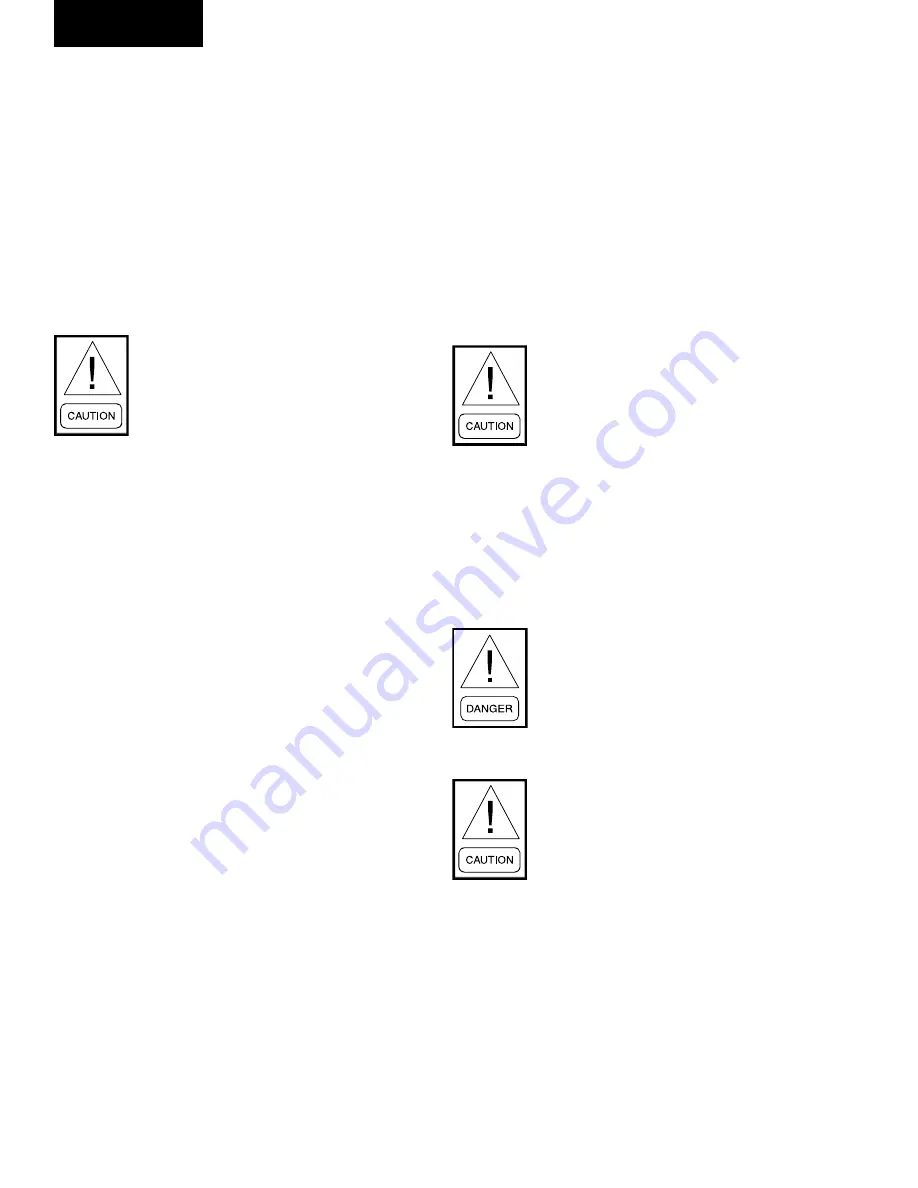
114
Maintenance
JOHNSON CONTROLS
5276178-JIM-C-0118
SECTION 4 – MAINTENANCE
GENERAL
A planned program of regularly scheduled maintenance
will return dividends by averting possible costly and
unexpected periods of down time. It is the responsibility
of the owner to provide the necessary maintenance
for the air handling units and coils. If a system failure
occurs due to improper maintenance during the warranty
period, Johnson Controls will not be liable for costs
incurred to return the unit to satisfactory operation.
Prior to any of the following mainte
-
nance procedures, shut off all power to
the unit. Failure to do so could cause
personal injury.
Label all wires prior to disconnection
when servicing controls. Wiring errors
can cause improper and dangerous
operation. Verify proper operation
after servicing.
PERIODIC MAINTENANCE – MONTHLY
Filters
Inspect once a month. Replace disposable or clean
permanent type as necessary. The dimensional size of
the replacement filter must be the same as the replaced
filter
(Refer to Table 11).
Linkages
Examine the damper and operator linkages to insure
that each is free and operating smoothly.
Compressors
Oil Level Check:
The oil level can only be tested when
the compressor is running in stabilized conditions, to
ensure that there is no liquid refrigerant in the lower
shell of the compressor. When the compressor is running
in stabilized conditions, the oil level must be between
1/4 and 3/4 in the oil sight glass.
Note: at shutdown,
the oil level can fall to the bottom limit of the oil sight
glass.
Oil Analysis:
Use Johnson Controls Type “T” POE oil
(clear) for units charged with R-410A refrigerant. The
type of refrigerant and amount per system is listed on
the unit rating plate. A change in the oil color or odor
may be an indication of contaminates in the refrigeration
system. If this occurs, an oil sample should be taken
and analyzed. If contaminations are present, the system
must be cleaned to prevent compressor failure. This can
be accomplished through the installation of oversized
suction and liquid line driers. The driers may have to be
changed several times to clean up the system depending
on the degree of contamination.
Never use the scroll compressor
to pump the refrigerant system down
into a vacuum. Doing so will cause
internal arcing of the compressor
motor, which will result in failure of
compressor.
Condenser Coils
Dirt should not be allowed to accumulate on the
condenser coil surfaces. Cleaning should be as often
as necessary to keep coil clean.
PERIODIC MAINTENANCE – 3 TO 6 MONTHS
Disconnect and lock-out power from
the unit anytime service is being per
-
formed on the fan section. Failure to
do so could result in serious injury or
death due to the fan turning on while
work is in progress.
Squealing belts during starting is
caused by slipping belts that are not
tensioned properly.
Motors
Outdoor fan motors are permanently lubricated and
require no maintenance. Lubrication, if desired, is to
be performed by a qualified service agency.
Ventor motors are factory lubricated for an estimated
10-year life.
Summary of Contents for 40 25 TON
Page 22: ...22 JOHNSON CONTROLS 5276178 JIM C 0118 THIS PAGE INTENTIONALLY LEFT BLANK ...
Page 35: ...35 2 JOHNSON CONTROLS 5276178 JIM C 0118 FIGURE 10 PARTIAL ROOF CURB MODEL 1RC0455P LD14177 ...
Page 41: ...41 2 JOHNSON CONTROLS 5276178 JIM C 0118 FIGURE 18 40 TON FORWARD CURVE EXAMPLE ...
Page 159: ...159 JOHNSON CONTROLS 5276178 JIM C 0118 THIS PAGE INTENTIONALLY LEFT BLANK ...
Page 244: ...244 JOHNSON CONTROLS 5276178 JIM C 0118 Service NOTES ...