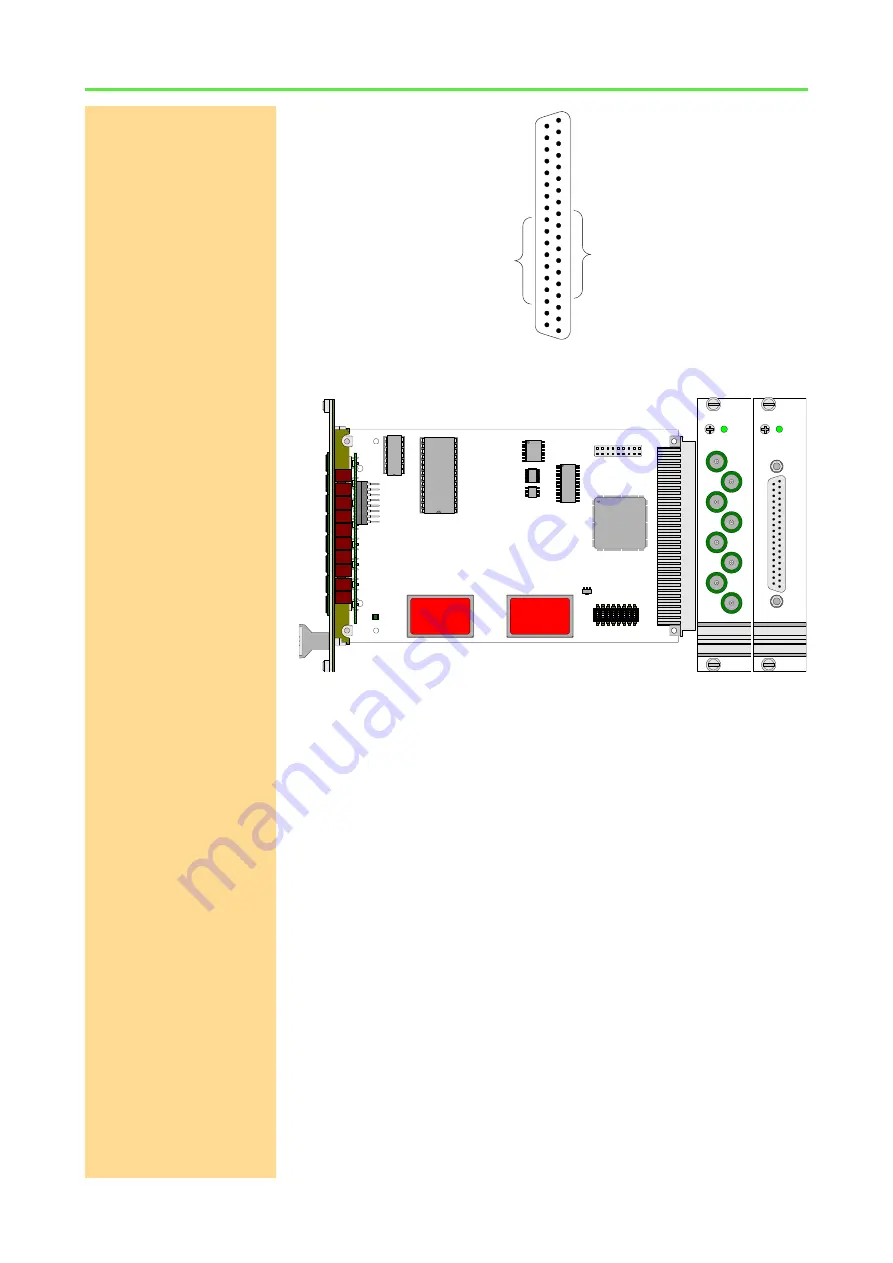
Pro I: Analog Input Modules
Pro-AIn-8/16 Rev. C
ADwin
60
ADwin-Pro
Hardware, manual version 2.9, June 2006
Fig. 101 – Pro-AIn-8/16-D Rev. C: Pin assignment differential
Fig. 102 –
: Board and front panel
ANALOG IN 1 (-)
ANALOG IN 2 (-)
ANALOG IN 3 (-)
ANALOG IN 4 (-)
ANALOG IN 5 (-)
ANALOG IN 6 (-)
ANALOG IN 7 (-)
ANALOG IN 8 (-)
AGND
RESERVED
ANALOG IN 1 (+)
ANALOG IN 2 (+)
ANALOG IN 3 (+)
ANALOG IN 4 (+)
ANALOG IN 5 (+)
ANALOG IN 6 (+)
ANALOG IN 7 (+)
ANALOG IN 8 (+)
AGND
RESERVED
DGND
19
18
17
16
15
14
13
12
11
10
9
8
7
6
5
4
3
2
1
37
36
35
34
33
32
31
30
29
28
27
26
25
24
23
22
21
20
RESERVED
RESERVED
19AD0102
A0 A1 A2 A3 A4 A5 A6 A7
74LS
19
ON
DIP
1
2
3
4
5
6
7
8
FPGA
A42MX16
D
G
407D
J
DC/DC CONVERTER
IN 5V OUT ±15V / ±65mA
DC/DC CONVERTER
IN 5V OUT ±5V / ±250mA
LT
C
1605C
S
W
MA
X
6225
D
S
1867
C
1-
100
P
G
A
206U
035
AIN8/16RB
ANALOG
INPUT
1
2
3
4
5
6
7
8
AIN8/16RB
ANALOG
INPUT