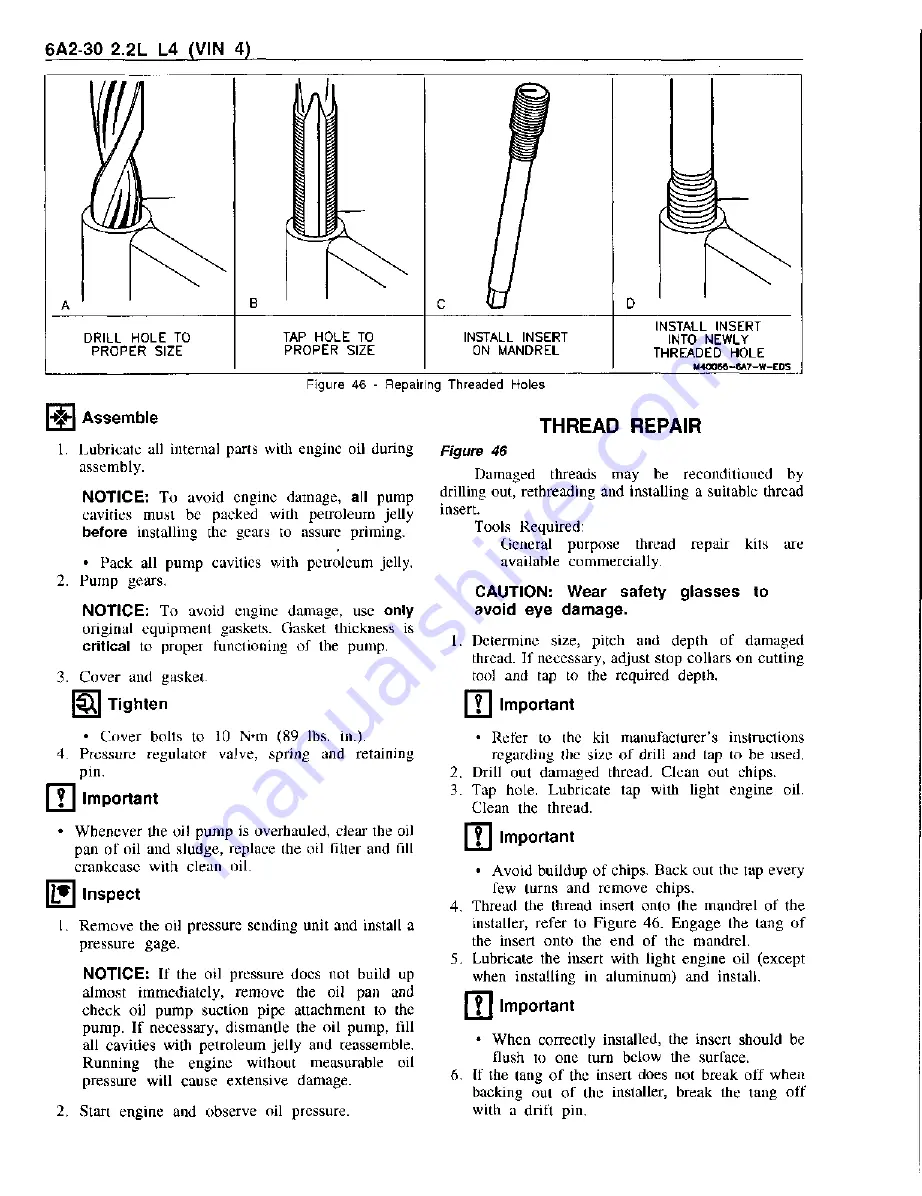
DRILL HOLE TO
PROPER SIZE
TAP HOLE TO
PROPER SIZE
INSTALL INSERT
ON MANDREL
INSTALL INSERT
INTO NEWLY
THREADED HOLE
M40066—6A7—W - E D S
Figure 46 - Repairing Threaded Holes
Assemble
1. Lubricate all internal parts with engine oil during
assembly.
NOTICE:
To avoid engine damage,
all
pump
cavities must be packed with petroleum jelly
before
installing the gears to assure priming.
• Pack all pump cavities with petroleum jelly.
2. Pump gears.
NOTICE:
To avoid engine damage, use
only
original equipment gaskets. Gasket thickness is
critical
to proper functioning of the pump.
3. Cover and gasket.
Tighten
• Cover bolts to 10 N*m (89 lbs. in.).
4. Pressure regulator valve, spring and retaining
pin.
Important
Whenever the oil pump is overhauled, clear the oil
pan of oil and sludge, replace the oil filter and fill
crankcase with clean oil.
Inspect
1. Remove the oil pressure sending unit and install a
pressure gage.
NOTICE:
If the oil pressure does not build up
almost immediately, remove the oil pan and
check oil pump suction pipe attachment to the
pump. If necessary, dismantle the oil pump, fill
all cavities with petroleum jelly and reassemble.
Running the engine without measurable oil
pressure will cause extensive damage.
2. Start engine and observe oil pressure.
THREAD REPAIR
Figure 46
Damaged threads may be reconditioned by
drilling out, rethreading and installing a suitable thread
insert.
Tools Required:
General purpose thread repair kits are
available commercially.
CAUTION: Wear safety glasses to
avoid eye damage.
1.
Determine size, pitch and depth of damaged
thread. If necessary, adjust stop collars on cutting
tool and tap to the required depth.
9
Important
• Refer to the kit manufacturer’s instructions
regarding the size of drill and tap to be used.
2. Drill out damaged thread. Clean out chips.
3. Tap hole. Lubricate tap with light engine oil.
Clean the thread.
m Important
• Avoid buildup of chips. Back out the tap every
few turns and remove chips.
4. Thread the thread insert onto the mandrel of the
installer, refer to Figure 46. Engage the tang of
the insert onto the end of the mandrel.
5. Lubricate the insert with light engine oil (except
when installing in aluminum) and install.
m Important
• When correctly installed, the insert should be
flush to one turn below the surface.
6. If the tang of the insert does not break off when
backing out of the installer, break the tang off
with a drift pin.
Summary of Contents for S Series 1994
Page 1: ......
Page 11: ...VIEW A p n n n j VIEW C F7554 Figure 10 Hydra Matic 4L60 E Transmission I D Location...
Page 24: ...NOTES...
Page 26: ......
Page 69: ...NOTES...
Page 71: ...3 2 STEERING...
Page 73: ......
Page 84: ......
Page 102: ...40...
Page 130: ...NOTES...
Page 146: ...NOTES...
Page 162: ...NOTES...
Page 166: ...Figure 5 Removing the Pinion Flange Figure 6 Pressing the Drive Pinion from the Cage...
Page 178: ...Figure 3 Spreading the Differential Case Figure 4 Removing the Differential...
Page 190: ...NOTES...
Page 202: ...NOTES...
Page 206: ...F5785...
Page 212: ...B Button Moved Out of Bearing Bore F5791...
Page 228: ...NOTES...
Page 232: ......
Page 234: ......
Page 236: ...Adjuster 63 Bolt 64 Lock Figure 10 Turning the Adjuster Plug K3 Models...
Page 237: ...Figure 13 Removing the Pinion Seal 39 Bearing Cup Figure 16 Removing the Inner Bearing Cap...
Page 261: ...F7475...
Page 267: ...B Button Moved Out of Bearing Bore F5791...
Page 294: ...NOTES...
Page 300: ...NOTES...
Page 318: ...NOTES...
Page 322: ...SR207LN2 EDS...
Page 324: ......
Page 326: ...OVERHEAD OILING AND RETURN MAIN OIL GALLERY N30005 6A2 J EDS...
Page 368: ...103 153 127 V1200...
Page 370: ......
Page 372: ......
Page 374: ...F9375 Figure 7 Engine Lubrication Diagram Engines Without Balance Shaft...
Page 376: ...Figure 9 Engine Lubrication Diagram Engines With Balance Shaft...
Page 399: ...V2974...
Page 410: ......
Page 412: ...195 196 201 174 252 163 165 164 244 3706r3924...
Page 452: ......
Page 454: ...163 164 V1202...
Page 456: ...20 21x 302 210 4 0 41 2 5 2 5 1 2 51 4 2 e3 54 3 9 252 252 S 255 255 25 6 256 209 V1196...
Page 458: ...100 1 8 4 185 183 177 v 75 201 3706r1204...
Page 460: ......
Page 510: ......
Page 512: ...V2131...
Page 514: ...110 106 106 103 90 93 89 88 87 86 v 7 7 7 7 j A _ 111 f t 2 a a s 53 49 L 47 46 3706r4751...
Page 516: ...259 260 150 237 S lM 180 167180 J 1 82 183 170 169 1 1 78 1 7 9 213212 2 0 7 205 r i 3706r4752...
Page 566: ...NOTES...
Page 574: ...NOTES...
Page 618: ...SPECIAL TOOLS...
Page 620: ...NOTES...
Page 672: ......
Page 682: ......
Page 686: ......
Page 694: ...RH0213 4L60 E...
Page 695: ...657 659 m i J 8092 H J 34196 4 3 34196 5 657 658 665 J 23907 J 7004 1 J 8092 RH0214 4L60 E...
Page 696: ...J 8092 J 34196 4 33 31 J 8092 RH0215 4L60 E...
Page 697: ...SPECIAL TOOLS...
Page 698: ...SPECIAL TOOLS...
Page 758: ...RH0194 4L80 E...
Page 764: ......
Page 770: ...SPECIAL TOOLS...
Page 771: ...SPECIAL TOOLS CONT...
Page 772: ......
Page 775: ......
Page 776: ......
Page 785: ......
Page 804: ...NOTES...
Page 806: ......
Page 808: ......
Page 822: ...3707r5079...
Page 840: ......
Page 848: ...NOTES...
Page 852: ......
Page 860: ...F5435...
Page 866: ......
Page 878: ...F9167...
Page 882: ...16 FrontOutputShaft 18 DrivtQNr 19 DrivenGm t 20 DriveChain 22 FrontOutputBearing V2836...
Page 890: ...F9168...
Page 908: ......
Page 919: ......