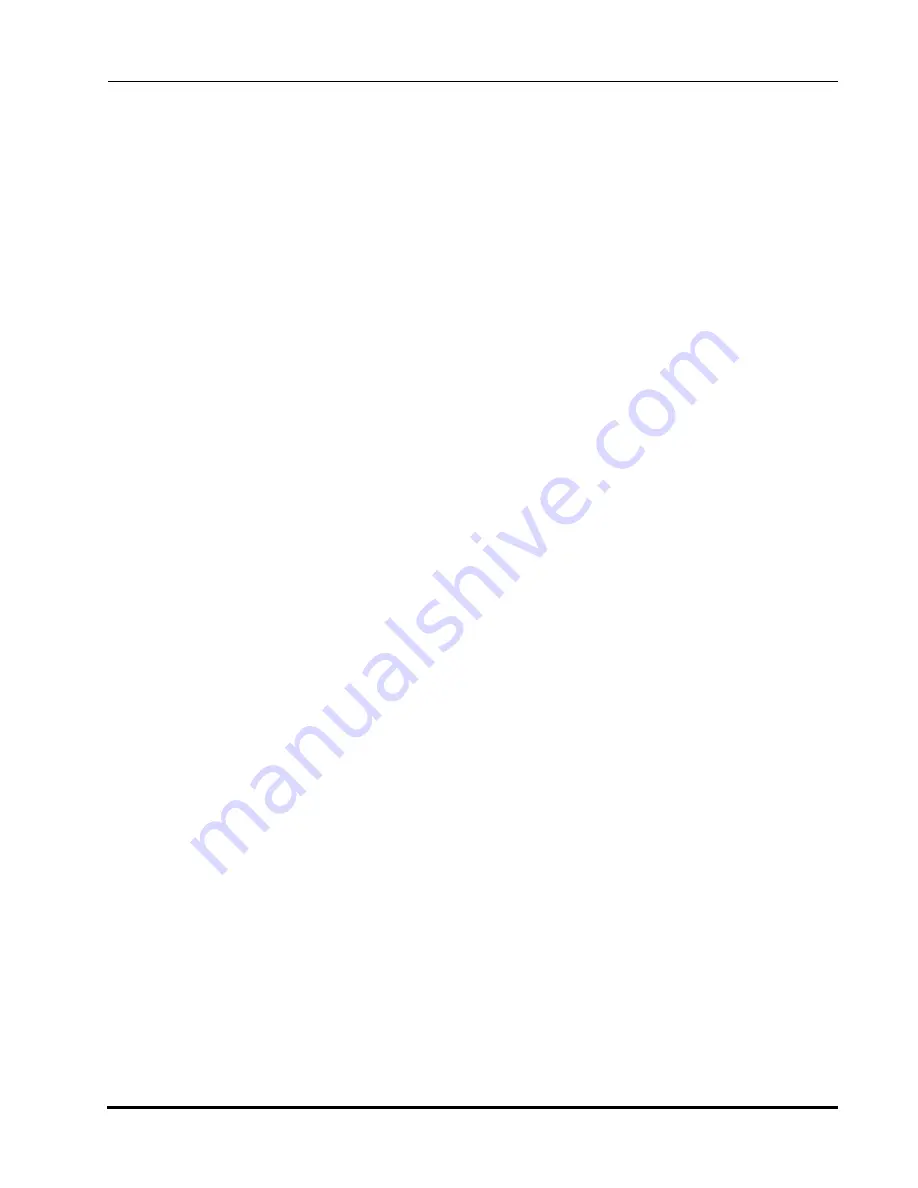
MagnaTran 7.1 User’s Manual
Operation
MN-003-1600-00
Operational Interlocks
Brooks Automation
Revision 2.2
6-27
This interface can be removed by following the command
. It
can also be moved to another output pin by following the procedure
Special Notes on the PowerPak
The PowerPak provides a controlled stop of the robot (see
). Two signals may be sent to the robot:
AC_FAIL_UPS: The robot comes to a controlled stop as quickly as possible
regardless of the position of the robot arm after receiving the signal.
BATT_LO_UPS: Monitors the status of the battery backup power in the Pow-
erPak. An error signal is sent when battery voltage is less than +23.5VDC.
To map the interlocks, the type of I/O board for the MagnaTran 7 robot must be
known:
High Side I/O Board
example:
MAP AC_FAIL_UPS EMER_STOP LOW TO DIGITAL_IN 0X800000
MAP BATT_LO_UPS UPS_BATTERY_SEN LOW TO DIGITAL_IN 0X400000
(IN23 = 0x800000) AC_FAIL_UPS
(IN22 = 0x400000) BATT_LO_UPS
Low Side I/O Board
example:
MAP AC_FAIL_UPS EMER_STOP LOW TO DIGITAL_IN 0X400000
MAP BATT_LO_UPS UPS_BATTERY_SEN LOW TO DIGITAL_IN 0X800000
(IN22 = 0x400000) AC_FAIL_UPS
(IN23 = 0x800000) BATT_LO_UPS
Relay I/O Board
(
Appendix F: Relay I/O Option on page 11-24
) example:
MAP AC_FAIL_UPS EMER_STOP LOW TO DIGITAL_IN 0X1000
MAP BATT_LO_UPS UPS_BATTERY_SEN LOW TO DIGITAL_IN 0X20000
Marathon Express MX I/O Board
example:
MAP AC_FAIL_UPS EMER_STOP LOW TO DIGITAL_IN 0X20000000