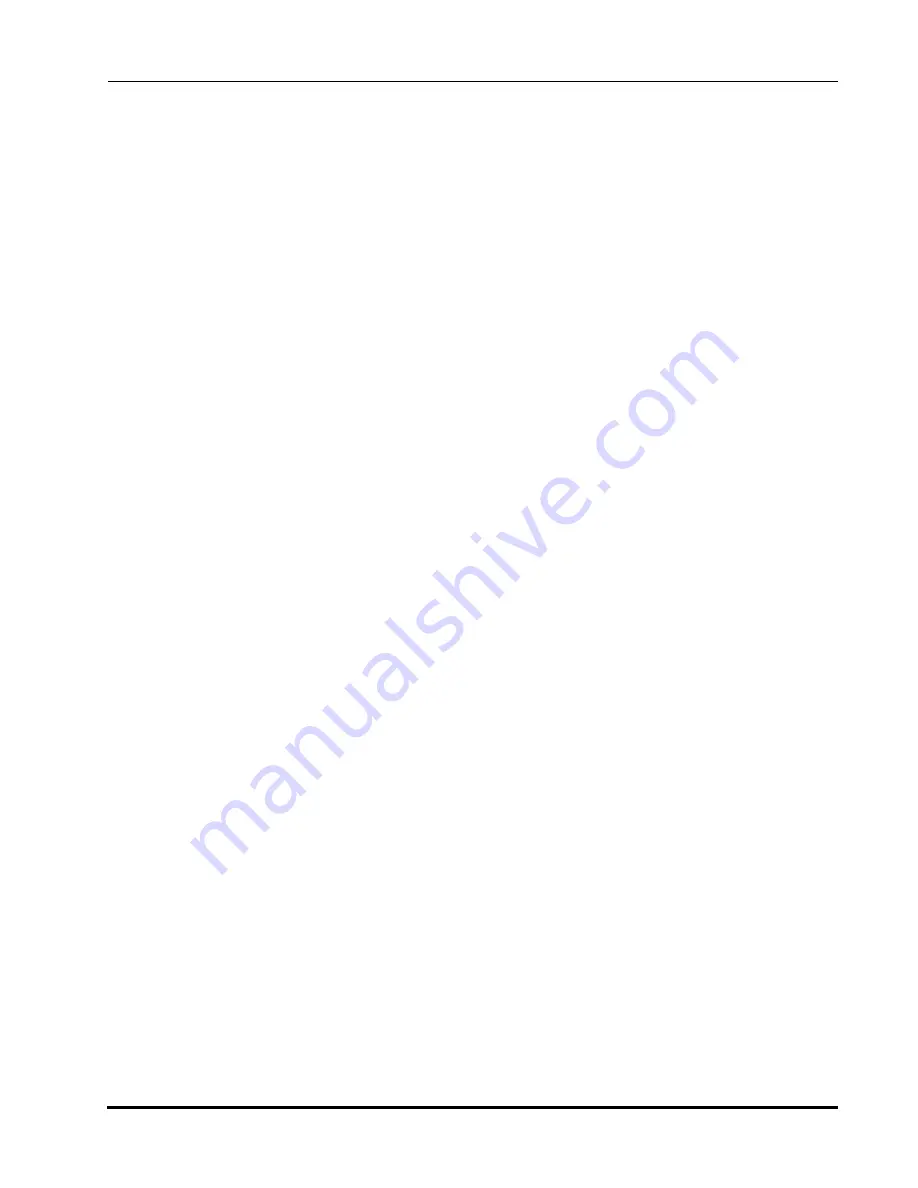
MagnaTran 7.1 User’s Manual
Alignment and Calibration
MN-003-1600-00
Verifying Flatness of Robot’s End Effector
Brooks Automation
Revision 2.2
7-5
Verifying Flatness of Robot’s End Effector
The end effector(s) must be flat to ensure proper support of the wafers being handled
by the robot.
This procedure checks for the top surfaces of the wafer supports on the end effector to
be within 0.076 mm (0.003 in) of each other and that no part of the end effector rises
above the lowest wafer support.
This procedure must be performed during initial setup if the end effector is suspected
of damage during shipment and at any time that the robot’s arms or end effector(s)
are damaged, removed and replaced, or changed while in the system. It is also recom-
mended that this procedure be performed every 90 days as a preventive maintenance
practice.
NOTE:
To successfully align the robot and to obtain consistent and precise handling of
wafers, the limits and tolerances stated in this verification procedure must be met.
Required Tools and Test Equipment
•
Granite surface block
•
Height gauge
Limits and Tolerances
Maximum deviation between supports 0.076 mm (0.003 in).
No point on the end effector’s surface will be higher than the lowest support.
Adjustment/Calibration Strategy
This procedure uses the granite surface block as a reference point to determine the
height of each wafer support on the end effector and to ensure that no part of the end
effector rises above the wafer supports.
Measurement Procedure
1.
Remove the end effector from the robot arms and place the end effector on a
granite surface block with the wafer supports facing up.
2.
Using the height gauge, measure the height of each wafer support.