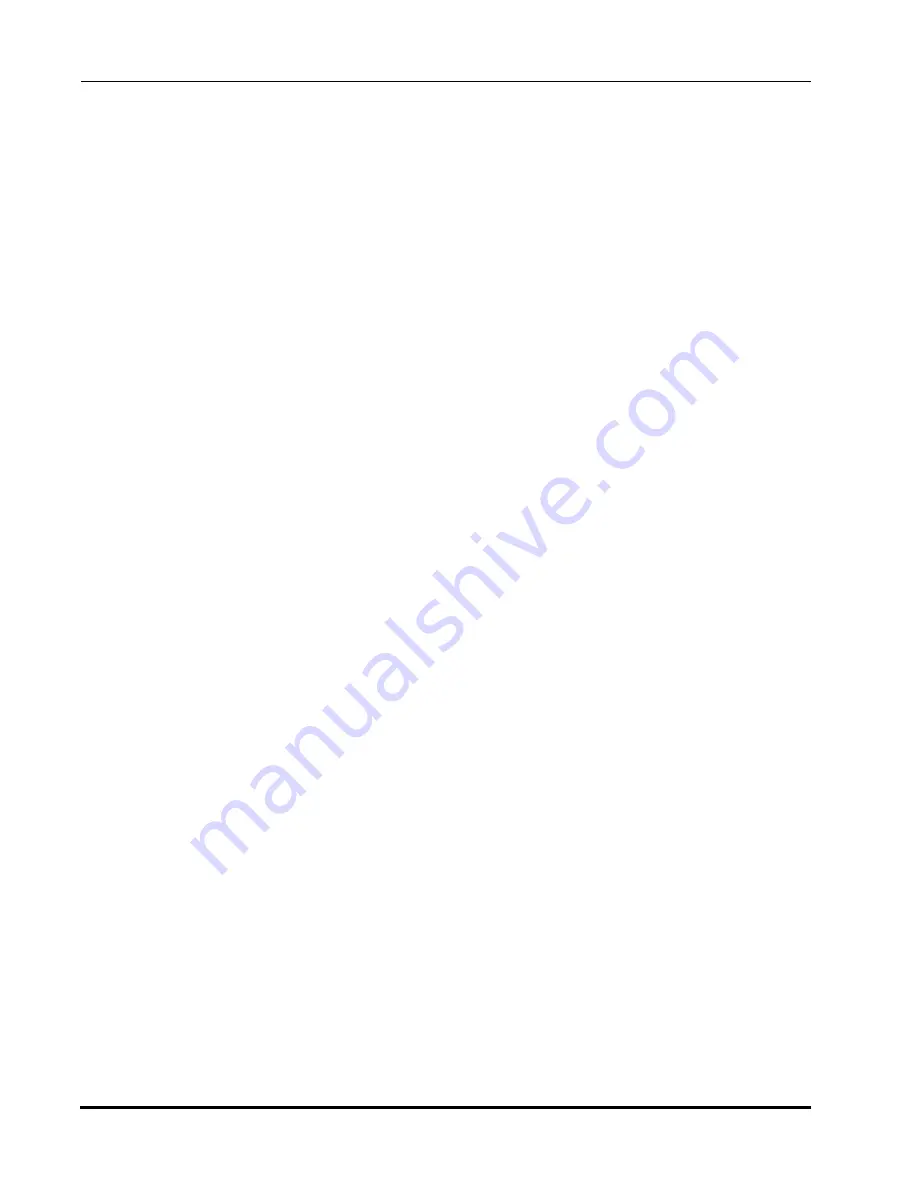
Maintenance and Repair
MagnaTran 7.1 User’s Manual
Repair Philosophy
MN-003-1600-00
Brooks Automation
9-22
Revision 2.2
Repair Philosophy
If a MagnaTran 7 malfunctions, refer to
in this manual for
diagnostic procedures. If these procedures are not adequate to determine the source
of the problem, refer to the MagnaTran 7 operational descriptions in
for in-depth descriptions of the various subsystems of the robot. Once the
failed unit or part has been identified it can be removed from the MagnaTran 7. Refer
to the
section in this chapter for basic removal/replacement proce-
dures.
A number of alternatives are available for obtaining replacement FRUs, IRCs, and
other parts to repair the MagnaTran 7. The following replacement parts options are
available for the MagnaTran 7:
•
Facilitated Field Repair (using Field Replaceable Units)
•
Depot Field Repair (using Individual Component Level Parts)
•
Brooks’ Priority Parts Service (PPS)
•
Preventive Maintenance (PM) Parts
•
Brooks’ Factory Repair Services
•
Finally, if MagnaTran 7 downtime is not critical, individual replacement parts
can be ordered from Brooks Customer Support (978) 262-2900, as required.
The difference between each of these approaches is how much time, on average, is
required to diagnose and repair the MagnaTran 7. A description of each option fol-
lows.
Facilitated Field Repair
The Facilitated Field Repair approach offers the fastest way to fix a hardware problem
in the field through the use of Field Replaceable Units (FRUs). The Field Replaceable
Units are designed to enable a trained technician to remove and replace the FRU. The
FRUs are designed to keep MTTR and, therefore, MagnaTran 7 downtime to a mini-
mum.
A series of FRUs has been identified for the MagnaTran 7 to reduce Mean Time To
Repair (MTTR) and to simplify repair procedures in the field. Some of these FRUs
may comprise a complete assembly, such as the Electronics Enclosure for the Mag-
naTran 7.
NOTE:
Maintenance training classes on how to trouble-shoot and repair a MagnaTran 7