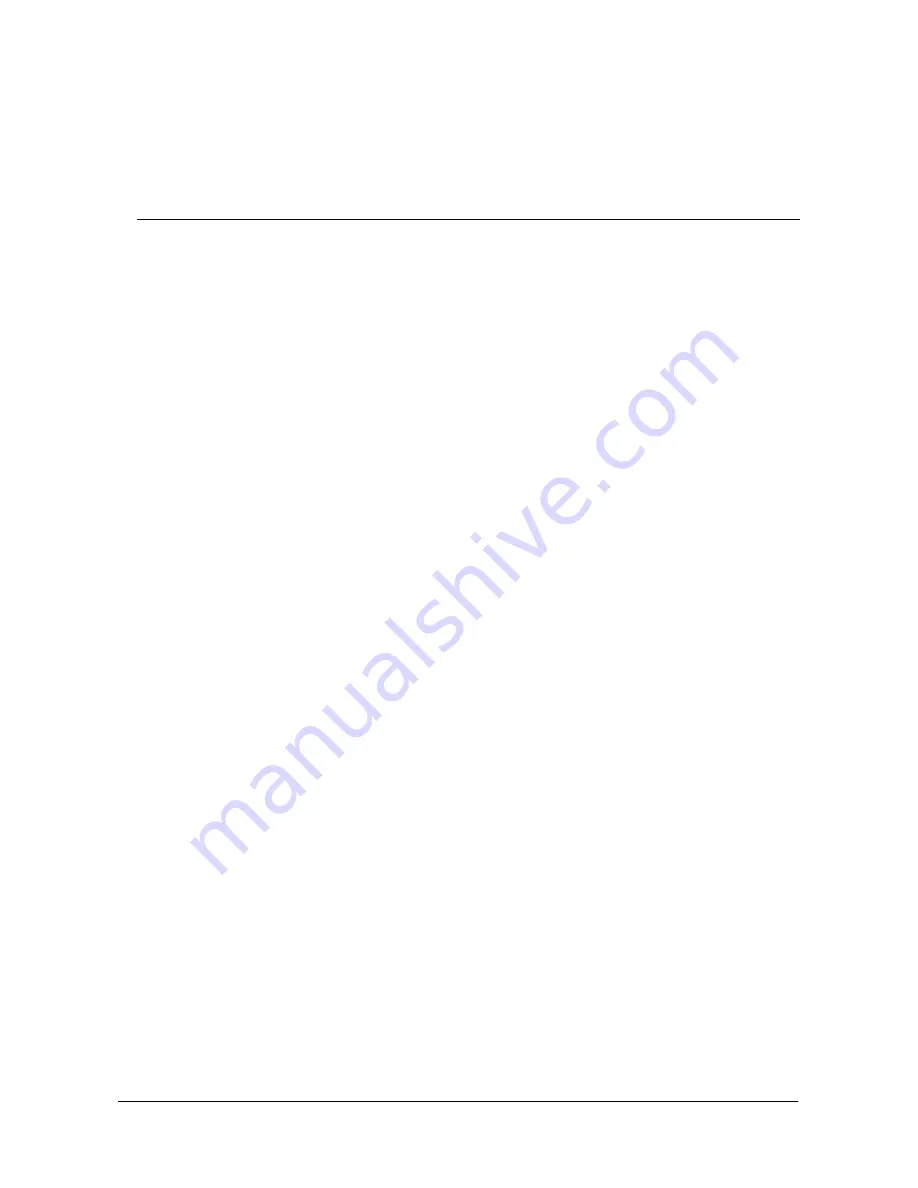
SINUS PENTA
PROGRAMMING
INSTRUCTIONS
38/452
7.
FIRST
STARTUP
For the signal wiring and power wiring, please refer to the
Sinus Penta’s Installation Instructions
manual
.
Parameter programming is detailed in the START-UP MENU.
7 .1 .
“IFD” Control Algorithm
SINUS PENTA drives are factory set with the IFD (
C010
) control algorithm, allowing the first startup of the equipment.
The default functions of the drive terminals are given in the table below. For more details, please refer to the
Sinus
Penta’s Installation Instructions manual
.
1) Wiring:
Follow the instructions stated in the “Caution Statements” and “Installation” sections
(Installation Instructions Manual).
2) Power on:
Power on the drive and do not close the link to the
START
input to prevent the
motor from running.
3)
Parameter
modification:
Access parameter
P000
(Key parameter) and set its code (default value: 00001).
Use the
ESC
,
▲
,
▼
and
SAVE/ENTER
keys to access the programming
parameters. Also refer to the Menu Tree.
4) Supply voltage:
Set the real supply voltage for the drive. You can set either mains voltage range or
the DC supply stabilized by a Regenerative Penta drive. To set the type of power
supply for the drive, access the MOTOR CONTROL MENU and set configuration
parameter
C008
to the value corresponding to the installation concerned.
5) Motor parameters:
Set
C010
(Control Algorithm) as IFD Voltage/Frequency; set the motor ratings as
follows:
-
C015
(fmot1) rated frequency
-
C016
(rpmnom1) rated rpm
-
C017
(Pmot1) rated power
-
C018
(Imot1) rated current
-
C019
(Vmot1) rated voltage
-
C029
(Speedmax1) max. allowable speed.
For loads with square torque with respect to the rpm (centrifugal pumps, fans, etc.),
set
C034
(preboost1) to 0%. Press SAVE/ENTER each time a new parameter value
is set.
6) Autotune:
For the IFD control algorithm, the Autotune function is not necessary but is
always recommended.
First remove the
ENABLE
command, then access the AUTOTUNE MENU and set
I073
[1: Motor Tune] and
I074
= [0: All Ctrl no rotation]. Use the
ESC
key to accept
changes. Close the
ENABLE
command and wait until tune is complete (Warning
“
W32
Open Enable” is displayed). The drive has computed and saved the values for
C022
(stator resistance) and
C023
(leakage inductance).
If alarm “
A097
Motor Wires KO“ trips, check the motor wiring. If alarm “
A065
Autotune KO” trips, this means that the
ENABLE
command has opened before
autotune was complete. In this case, reset the drive sending a command from
terminal MDI3, or press the
RESET
key in the display/keypad and perform the
autotune procedure again.
7) Overload:
Set parameters in the LIMITS MENU depending on the max. desired current.
8) Startup:
Activate the
ENABLE
input (terminal 15) and the
START
input (terminal 14) and
send a speed reference: the RUN LED and REF LED will come on and the motor will
start. Make sure that the motor is rotating in the correct direction. If not, select the
Engineering Level (P001) and set parameter
C014
(Phase Rotation) to [1:Yes], or
open the ENABLE and START inputs, remove voltage from the drive and, after
waiting at least 5 minutes, reverse two of the motor phases.