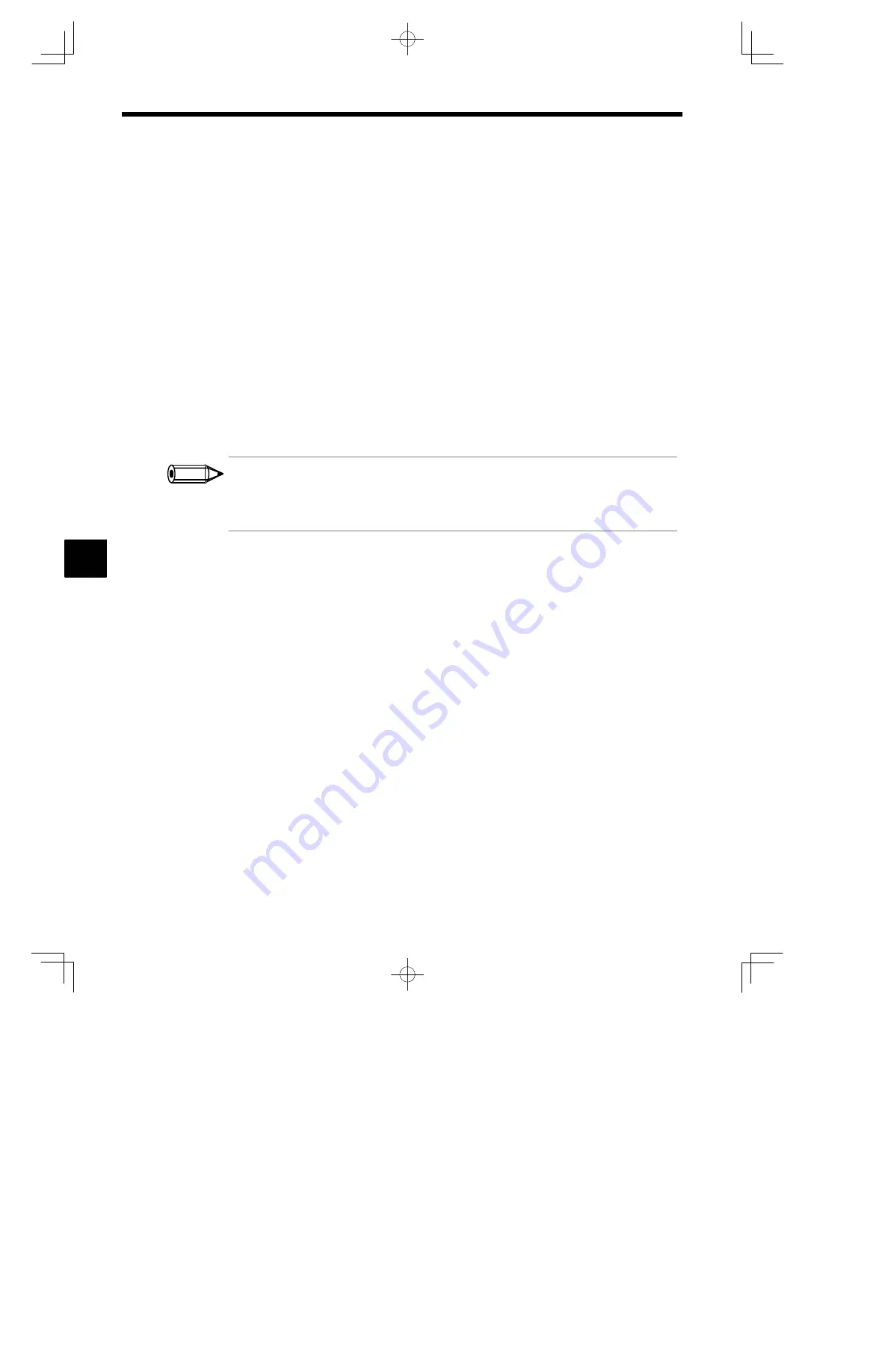
Servo Adjustment
6.4.3 Making Manual Adjustments
6 -28
D
Torque Reference Filter Time Constant (Pn401)
If the mechanical system uses ball screws, torsion resonance may result, in which case the
oscillation noise will be a high-pitched tone. The oscillation may be stopped by increasing
the time constant of the torque reference filter. Like the integral time constant, this filter
causes a delay in the operation of the servo system. Therefore, this constant must not be set
to an excessively large value.
D
Speed Reference Input Gain (Pn300)
Changing the speed reference input gain set in Pn300 is equivalent to changing the position
loop gain. In other words, an increase in the speed reference input gain set in Pn300 isequiv-
alent to a decrease in the position loop gain and vice versa. Use this user constant in the fol-
lowing cases.
·
When the host controller does not have a function for adjusting the position loop gain.
(The host incorporates a D/A converter to change the number of bits but cannot make
fine adjustments of position loop gain.)
·
When it is necessary to clamp the full range of the speed reference output of the host de-
vice to a specified rotation speed.
In normal operation, the factory-set value can be used as it is.
If the Servopack is used for speed control, the position loop gain set in Pn102 is enabled in zero-clamp mode
only. In normal control operation, change the position loop gain through the host or change the speed reference
input gain in Pn300 in the Servopack. The position loop gain remains the same if the setting in Pn102 is
changed.
Adjustment Method
1.
Set the position loop gain to a comparatively low value in the host device. Then increase the
speed loop gain set in Pn100 to within a range where there isno noise or oscillation resulting.
If the position loop gain cannot be changed through the host device, increase the speedrefer-
ence input gain set in Pn300 to a larger value.
2.
Decrease the speed loop gain a little from the value set in step 1. Then increase the position
loop gain through the host controller to within a range where there is no noise or oscillation
resulting. As in step 1., decrease the set value of Pn300 if the position loop gain cannot be
changed through the host device.
3.
Set the speed loop integral time constant in Pn101 while observing the positioning setting
time and the vibration of the mechanical system. If the constant is too large, positioning set-
ting time will be long.
4.
Set the torque reference filter to a small value in Pn401 if the mechanical system has shaft
torsion resonance. If the mechanical system generates oscillation noise in a high-pitched
tone, shaft torsion resonance may be occurring. In that case, set Pn401 to a larger value.
5.
Finally,progressivelymakefineadjustmentstouserconstantssuchastheposition loopgain,
speed loop gain, and integral time constant to find the optimal points.
6
INFO
AUDIN - 7 bis rue de Tinqueux - 51100 Reims - France - Tel : 03.26.04.20.21 - Fax : 03.26.04.28.20 - Web : http: www.audin.fr - Email : [email protected]