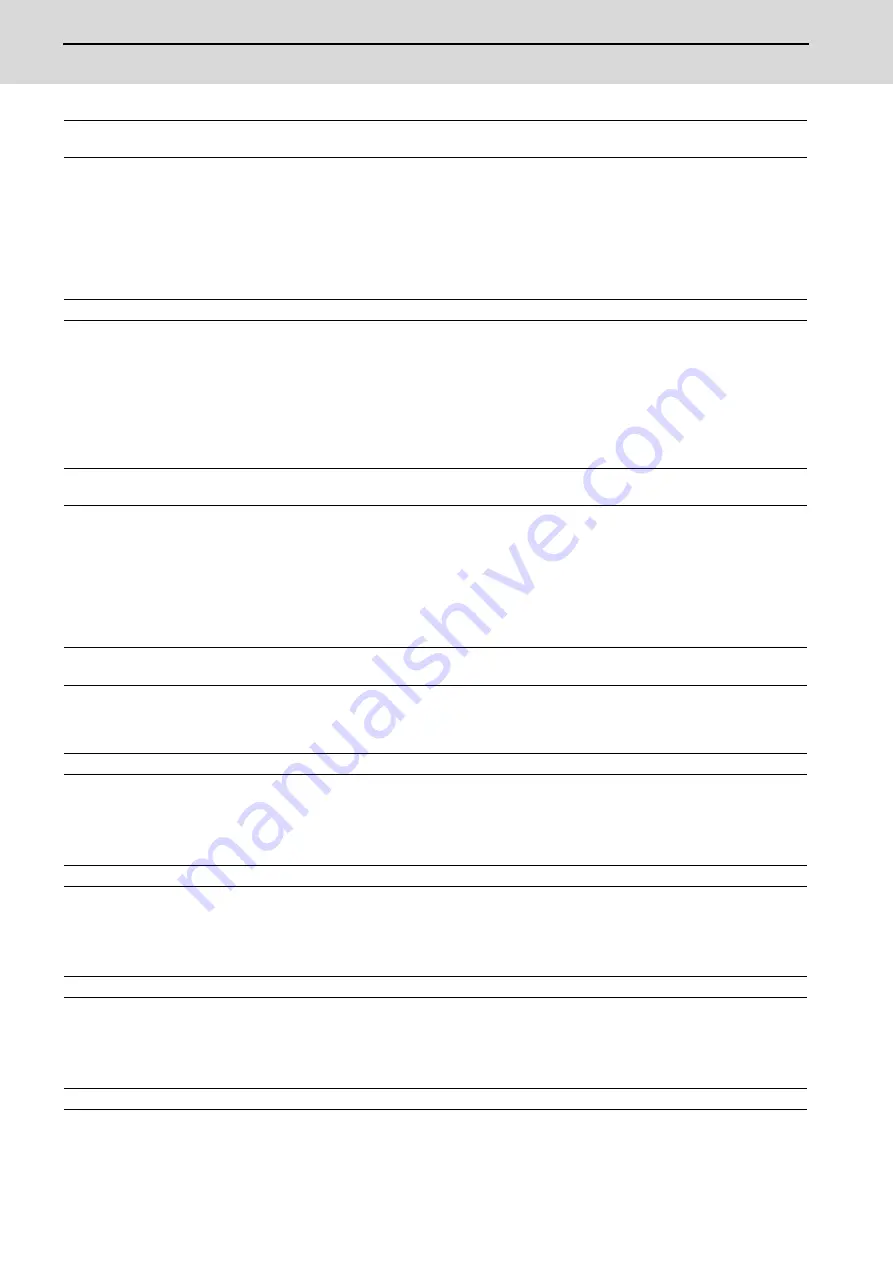
M800/M80/E80/C80 Series Alarm/Parameter Manual
16 Machine Parameters
676
IB-1501279-H
Set the excessive error detection width when "operation parameter group n" is selected.
The excessive error alarm (S03 0052) will be detected when the position droop becomes larger than this set-
ting value.
In the stopper positioning operation mode, this will be regarded as excessive error detection width when po-
sitioning to the stopper starting coordinates. .
---Setting range---
0 to 32767( ° or mm)
Set the tolerable value at which "set position reached" (JST) or "automatic set position reached" (JSTA) sig-
nal is output when "operation parameter group n" is selected.
"Set position reached" (JST) indicates that the machine position is at any station.
During automatic operation, "automatic set position reached" (JSTA) is also output under the same condition.
These signals will turn OFF when the machine position moves away from the station over this value.
---Setting range---
0.000 to 99999.999( ° or mm)
Set the tolerable value at which "near set position" (NEAR) signal is output when "operation parameter group
n" is selected.
"Near set position" (NEAR) indicates that the machine position is near any station position.
This value is generally set wider than the set position output width. During operations, this is related to the
special commands when the station selection is set to "0".
---Setting range---
0.000 to 99999.999(° or mm)
Select the acceleration/deceleration type when "operation parameter group n" is selected.
0, 1: Linear acceleration/deceleration
F: S-pattern acceleration/deceleration
Set the station 2 coordinate value when arbitrary coordinate assignment is selected.
The station 1 coordinate value is fixed at "0.000" (machine coordinate zero point).
---Setting range---
-99999.999 to 99999.999(° or mm)
Set the station 3 coordinate value when arbitrary coordinate assignment is selected.
The station 1 coordinate value is fixed at "0.000" (machine coordinate zero point).
---Setting range---
-99999.999 to 99999.999(° or mm)
Set the station 4 coordinate value when arbitrary coordinate assignment is selected.
The station 1 coordinate value is fixed at "0.000" (machine coordinate zero point).
---Setting range---
-99999.999 to 99999.999(° or mm)
Set the station 5 coordinate value when arbitrary coordinate assignment is selected.
The station 1 coordinate value is fixed at "0.000" (machine coordinate zero point).
---Setting range---
-99999.999 to 99999.999(° or mm)
#12815+10(n-1)
aux_ODn
Operation parameter group n Excessive error detection
width
#12816+10(n-1)
aux_justn
Operation parameter group n Set position output width
#12817+10(n-1)
aux_nearn
Operation parameter group n Near set position output
width
(PR)
#12818+10(n-1)
aux_smgstn
Operation parameter group n Acceleration/Deceleration
type
#12850
aux_stpos2
Station 2 coordinate
#12851
aux_stpos3
Station 3 coordinate
#12852
aux_stpos4
Station 4 coordinate
#12853
aux_stpos5
Station 5 coordinate
Содержание C80 Series
Страница 1: ......
Страница 7: ......
Страница 11: ......
Страница 13: ......
Страница 15: ......
Страница 18: ...1 IB 1501279 H Alarm ...
Страница 19: ...M800 M80 E80 C80 Series Alarm Parameter Manual 2 IB 1501279 H ...
Страница 20: ...1 3 IB 1501279 H Operation Errors M ...
Страница 54: ...2 37 IB 1501279 H Stop Codes T ...
Страница 62: ...3 45 IB 1501279 H Servo Spindle Alarms S ...
Страница 81: ...M800 M80 E80 C80 Series Alarm Parameter Manual 3 Servo Spindle Alarms S 64 IB 1501279 H ...
Страница 82: ...4 65 IB 1501279 H MCP Alarms Y ...
Страница 98: ...5 81 IB 1501279 H System Alarms Z ...
Страница 111: ...M800 M80 E80 C80 Series Alarm Parameter Manual 5 System Alarms Z 94 IB 1501279 H ...
Страница 112: ...6 95 IB 1501279 H Absolute Position Detection System Alarms Z7 ...
Страница 117: ...M800 M80 E80 C80 Series Alarm Parameter Manual 6 Absolute Position Detection System Alarms Z7 100 IB 1501279 H ...
Страница 118: ...7 101 IB 1501279 H Distance coded Reference Scale Errors Z8 ...
Страница 120: ...8 103 IB 1501279 H Emergency Stop Alarms EMG ...
Страница 124: ...9 107 IB 1501279 H Computer Link Errors L ...
Страница 126: ...10 109 IB 1501279 H User PLC Alarms U ...
Страница 136: ...11 119 IB 1501279 H Network Service Errors N ...
Страница 139: ...M800 M80 E80 C80 Series Alarm Parameter Manual 11 Network Service Errors N 122 IB 1501279 H ...
Страница 140: ...12 123 IB 1501279 H Program Errors P ...
Страница 178: ...13 161 IB 1501279 H Smart Safety Observation Alarm V ...
Страница 192: ...14 175 IB 1501279 H Multi CPU Errors A C80 ...
Страница 215: ...M800 M80 E80 C80 Series Alarm Parameter Manual 14 Multi CPU Errors A C80 198 IB 1501279 H ...
Страница 216: ...199 IB 1501279 H Parameter ...
Страница 217: ...M800 M80 E80 C80 Series Alarm Parameter Manual 200 IB 1501279 H ...
Страница 218: ...15 201 IB 1501279 H User Parameters ...
Страница 359: ...M800 M80 E80 C80 Series Alarm Parameter Manual 15 User Parameters 342 IB 1501279 H ...
Страница 360: ...16 343 IB 1501279 H Machine Parameters ...
Страница 748: ......