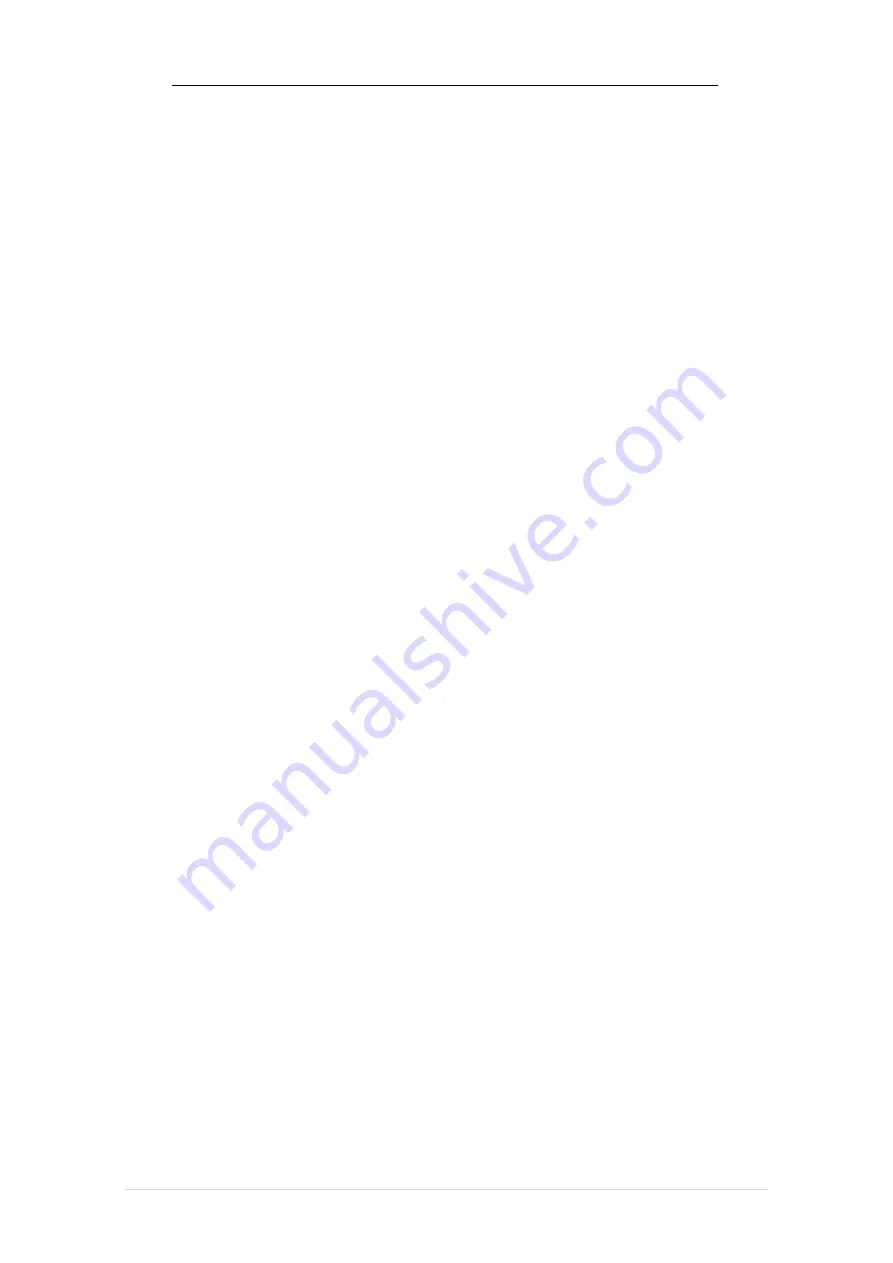
Chapter 6 - Fuselage - Translations (includes
mechanics)
6.13 - Extras
Page 135
locate a bolt to attach as far forward as practical on the flat surface on the side of the
“fork” (the nose wheel fork has a material separator pointing forward for this end). A
“fix” shaped Bondo or micro dry can be used to match and space the inner surface of the
wheel fairing to the side of the “fork”. Center of the fairing longitudinal seam with the
tire axis during this assembly. The material on the’ fork” side can be used for the clamping
segment - we suggest #10-32. attaching screws should be located even wider on the sides
of the”fork” and as far apart as allowed by the “fork” in width. (Make sure the bolts
extending across this surface do not rub into the tire or wheel - watch the placement and
trimmed length for this). If the fixing holes are exploited as suggested rather than using
self-locking nut plates, remember to use Loktite wire compound or similar warranty on
final assembly.
FARING NOSE GEAR MEETING SKETCH
Temporarily attach the other half, and locate a similar set of screws and “fixes” in
symmetrical locations. Check at each step to ensure proper alignment is being maintained,
and trim or add shim material as needed.
Make a note of the complexity of assembly and disassembly, and decide if you are
going to provide a hole for tire inflation. If so, carefully locate the required hole and cut
it out before painting. Electric fountain houses frequently sell metal plated push in capital
letters that could be used to close such a hole in such a final way.