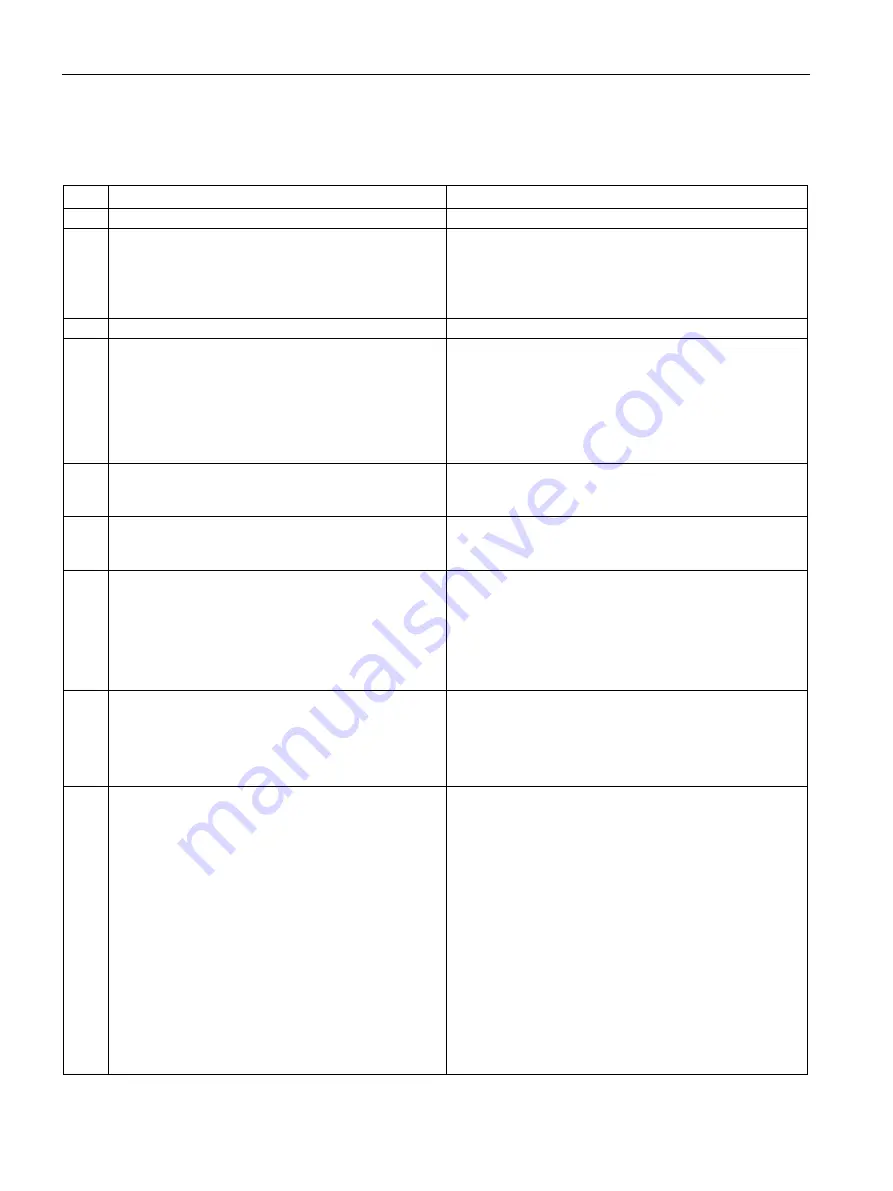
Commissioning
5.4 Commissioning in fast pulse train position control mode (Fast PTI)
SINAMICS V90, SIMOTICS S-1FL6
180
Operating Instructions, 04/2019, A5E36037884-007
5.4
Commissioning in fast pulse train position control mode (Fast PTI)
Step
Description
Comment
1
Switch off the line supply.
2
Power off the servo drive and connect it to the control-
ler (for example, SIMATIC S7-200 SMART) with the
signal cable.
The digital signal EMGS must be kept at high level (1) to
ensure normal operation.
Refer to "Standard application wiring (factory setting)
(Page 136)" and "Connection examples with PLCs
(Page 146)".
3
Switch on the 24 VDC power supply.
4
Check the servo motor type.
•
If the servo motor has an incremental encoder,
input the motor ID (p29000).
•
If the servo motor has an absolute encoder, the
servo drive can identify the servo motor automati-
cally.
Fault F52984 occurs when the servo motor is not identi-
fied.
You can find the motor ID from the motor rating plate. Go
to "Motor components (Page 30)" for detailed descriptions
about motor rating plate.
Refer to "Basic operations (Page 195)" for information
about how to change a parameter with the BOP.
5
Check the current control mode by viewing value of
the parameter p29003. Set p29003 = 9 for Fast PTI
control mode.
Refer to "Compound controls (Page 209)".
6
Save the parameter and restart the servo drive to
apply the setting of the pulse train input position con-
trol mode.
7
Select a setpoint pulse train input form by setting pa-
rameter p29010.
•
p29010 = 0 (default): pulse + direction, positive logic
•
p29010 = 1: AB track, positive logic
•
p29010 = 2: pulse + direction, negative logic
•
p29010 = 3: AB track, negative logic
Refer to "Selecting a setpoint pulse train input form
(Page 223)".
8
Select a pulse input channel by setting parameter
p29014.
•
p29014 = 0: high-speed 5 V differential pulse train
input (RS485)
•
p29014 = 1 (default): 24 V single end pulse train input
Refer to "Selecting a setpoint pulse train input channel
(Page 222)".
9
Set the electronic gear ratio.
You can use one of the following three methods to set the
electronic gear ratio:
•
Set the electronic gear ratio with parameters p29012
and p29013.
–
p29012: numerator of the electronic gear. Four
numerators in total (p29012[0] to p29012[3]) are
available.
–
p29013: denominator of the electronic gear.
•
Set the setpoint pluses per revolution.
–
p29011: number of setpoint pulses per revolution.
•
Calculate the electronic gear ratio by selecting me-
chanical structure.
–
For more information, see SINAMICS V90 V-
ASSISTANT Online Help.
Refer to "Electronic gear ratio (Page 225)".