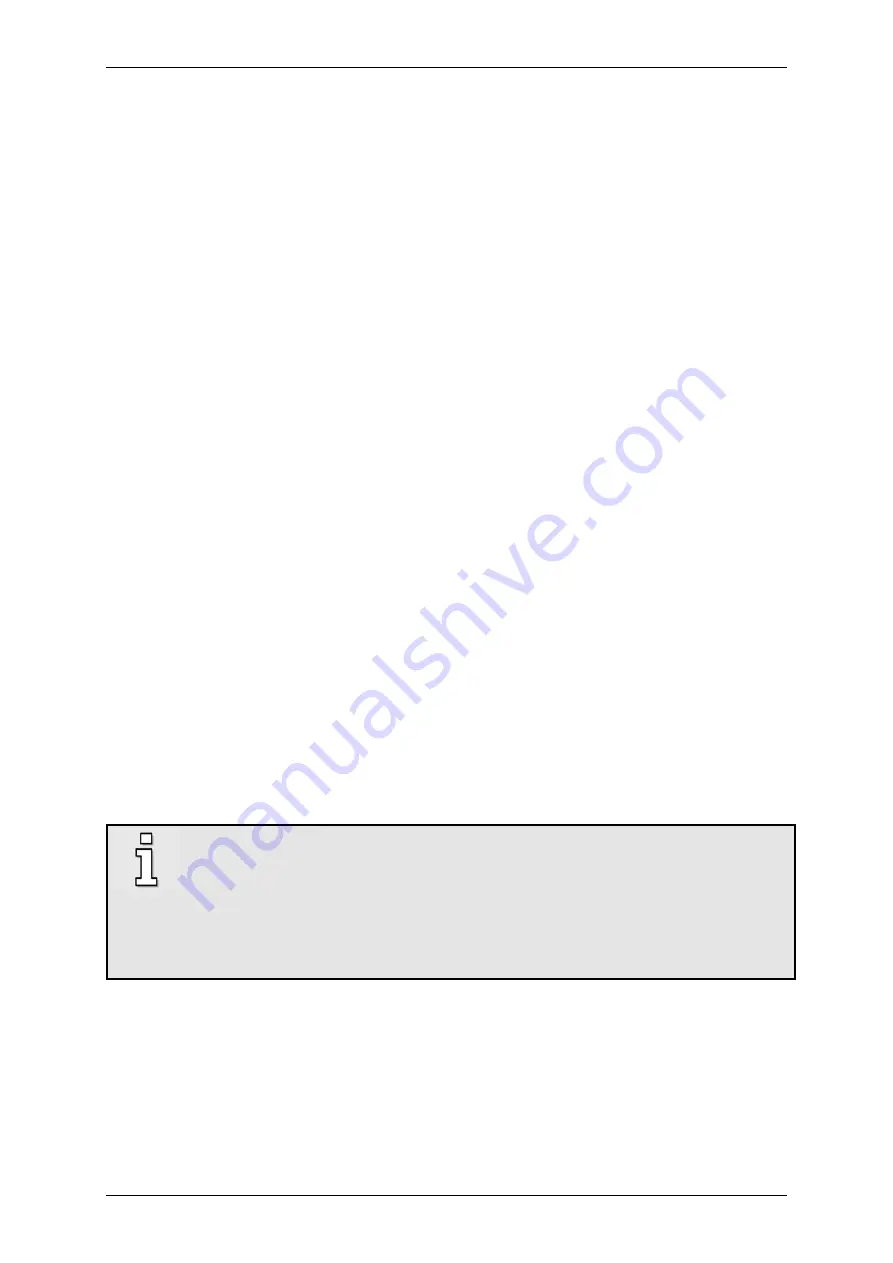
Page 52
4
Current and speed control
Function overview
The current and speed control system is a cascade control structure with an internal current control
circuit and a superimposed speed control circuit. These controllers are PI controllers. The setpoint
selectors are used to transfer setpoints from various different sources to the corresponding controllers
(see
chapter 4.2 Setpoint assignment through setpoint selectors
).
The basic structure is shown in the block diagram on the next page.
In the case of a rotor-oriented control, two phase currents and the rotor position are measured. At first,
the currents are transformed into an imaginary part and a real part with the help of a Clark
transformation. Then they are transformed back into the rotor coordinates using a Park transformation.
This allows the rotor currents to be controlled to corresponding rotor voltages using PI-controllers and
to transform them back into the stator system. The driver signal generation uses a symmetrical pulse
width modulation for the power stage in sine commutation with the third harmonic.
An integrator monitors the current
2
-time-integral of the controller. If a maximum value (maximum
current for 1s) is exceeded, a warning will be issued and the current will be limited to the rated current.
The main advantages of the rotor-oriented current control have already been summarized in
In torque-controlled mode, a current setpoint
i_set
is predefined for the active current controller. In this
operating mode, only the current controller in the servo positioning controller is active. As the torque
generated on the motor shaft is approximately proportional to the active current in the motor, one can
justifiably talk about torque control.
The accuracy of the torque control depends mainly on the motor and the sensor system
used to measure the rotor position.
With a good synchronous machine, a high-resolution rotary encoder (SINCOS encoder)
and good controller adjustment, the DUET_FL can reach a torque ripple in the range of
1% to 3% referred to the maximum current or the associated maximum torque of the
motor.
In speed-controlled mode, a certain speed setpoint is assigned. The DUET_FL servo positioning
controller determines the current actual speed
n_actual
through the encoder evaluation.
To make sure
that the speed setpoint is complied with, the current setpoint
i_set
is determined.
User Manual DUET_FL „DUET_FL 48/10“
Version 1.1 Motor Power Company
Summary of Contents for DUET_FL 48/10
Page 3: ...ber dieses Handbuch Page 3...
Page 4: ...Page 4 User Manual DUET_FL DUET_FL 48 10 Version 1 1 Motor Power Company...
Page 12: ...Page 12 List of Figures User Manual DUET_FL DUET_FL 48 10 Version 1 1 Motor Power Company...
Page 15: ...Page 15 List of Tables User Manual DUET_FL DUET_FL 48 10 Version 1 1 Motor Power Company...
Page 76: ...Page 76 User Manual DUET_FL DUET_FL 48 10 Version 1 1 Motor Power Company...
Page 196: ...Page 196 User Manual DUET_FL DUET_FL 48 10 Version 1 1 Motor Power Company...