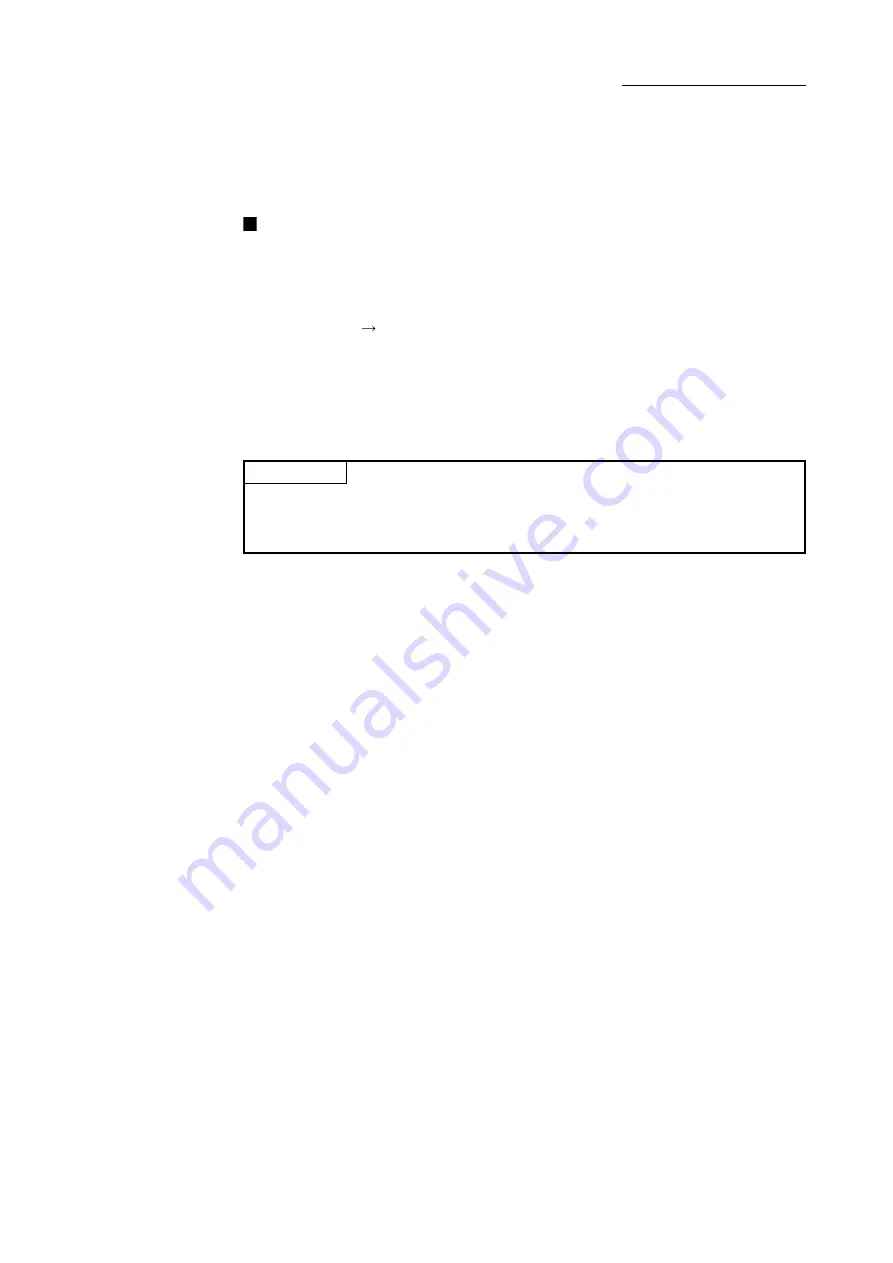
16 - 9
Chapter 16 Troubleshooting
16.4 Error and warning details
[1] Errors
Types of errors
Errors detected by the QD77MS include parameter setting range errors, errors at
the operation start or during operation and errors detected by servo amplifier.
(1) Errors detected by the QD77MS include parameter setting range errors
The parameters are checked when the power is turned ON and at the rising
edge (OFF ON) of the PLC READY signal [Y0]. An error will occur if there is
a mistake in the parameter setting details at that time.
When this kind of error occurs, the QD77 READY signal [X0] does not turn
ON.
To cancel this kind of error, set the correct value in the parameter for which
the error occurred, and then turn ON the PLC READY signal [Y0].
POINT
Execute the re-setup of the parameter after you execute the initialization (refer to
the Section 14.2) of the parameter when the error (error code: 900 to 999) occurs in
many and QD77MS doesn't start.
(2) Errors at the operation start or during operation (QD77MS detection errors)
These are errors that occur at the operation start or during operation when the
positioning control, JOG operation, or inching operation is used. If an axis
error occurs during interpolation operation, the error No. will be stored in both
the reference axis and the interpolation axis.
Note that, in the following cases (a) and (b), the axis error No. will be stored
only in the reference axis during analysis of the positioning data set in each
point of the positioning start data table.
(a) When the interpolation axis is BUSY.
(b) When the error occurred in positioning data or parameters unrelated to
interpolation control.
If the error occurred at the simultaneous start of a positioning operation, the
axis error storage details will differ depending on whether the error occurred
before or after the simultaneous start.
•
If the error occurred before the simultaneous start (illegal axis No., other axis
BUSY, etc.), an "error before simultaneous start" will occur.
•
If the error occurred after the simultaneous start (positioning data error,
software stroke limit error, etc.), an error code corresponding to the axis in
which the error occurred will be stored. Because a simultaneous start
cannot be carried out due to this, a "simultaneous start not possible error"
error code will be stored in all axes in which an error has not occurred.
The axis operation status will be displayed as "error occurring" for axes in
which an error occurred.
If an error occurs during operation, any moving axes will deceleration stop,
and their operation status will be displayed as "error occurring".
All axes will decelerate to a stop during interpolation operations, even if the
error occurs in only one axis.
Summary of Contents for MELSEC-Q QD77MS
Page 1: ......
Page 27: ...A 26 MEMO...
Page 29: ...MEMO...
Page 101: ...3 34 Chapter 3 Specifications and Functions MEMO...
Page 232: ...5 111 Chapter 5 Data Used for Positioning Control MEMO...
Page 315: ...5 194 Chapter 5 Data Used for Positioning Control MEMO...
Page 337: ...6 22 Chapter 6 Sequence Program Used for Positioning Control...
Page 338: ...6 23 Chapter 6 Sequence Program Used for Positioning Control...
Page 339: ...6 24 Chapter 6 Sequence Program Used for Positioning Control...
Page 340: ...6 25 Chapter 6 Sequence Program Used for Positioning Control...
Page 341: ...6 26 Chapter 6 Sequence Program Used for Positioning Control...
Page 342: ...6 27 Chapter 6 Sequence Program Used for Positioning Control...
Page 343: ...6 28 Chapter 6 Sequence Program Used for Positioning Control...
Page 344: ...6 29 Chapter 6 Sequence Program Used for Positioning Control...
Page 345: ...6 30 Chapter 6 Sequence Program Used for Positioning Control...
Page 346: ...6 31 Chapter 6 Sequence Program Used for Positioning Control...
Page 347: ...6 32 Chapter 6 Sequence Program Used for Positioning Control...
Page 348: ...6 33 Chapter 6 Sequence Program Used for Positioning Control...
Page 349: ...6 34 Chapter 6 Sequence Program Used for Positioning Control...
Page 353: ...6 38 Chapter 6 Sequence Program Used for Positioning Control...
Page 354: ...6 39 Chapter 6 Sequence Program Used for Positioning Control...
Page 357: ...6 42 Chapter 6 Sequence Program Used for Positioning Control...
Page 359: ...6 44 Chapter 6 Sequence Program Used for Positioning Control...
Page 360: ...6 45 Chapter 6 Sequence Program Used for Positioning Control...
Page 361: ...6 46 Chapter 6 Sequence Program Used for Positioning Control...
Page 363: ...6 48 Chapter 6 Sequence Program Used for Positioning Control...
Page 364: ...6 49 Chapter 6 Sequence Program Used for Positioning Control...
Page 413: ...MEMO...
Page 433: ...8 20 Chapter 8 OPR Control MEMO...
Page 458: ...9 25 Chapter 9 Major Positioning Control MEMO...
Page 593: ...10 30 Chapter 10 High Level Positioning Control MEMO...
Page 625: ...11 32 Chapter 11 Manual Control MEMO...
Page 659: ...12 34 Chapter 12 Expansion Control MEMO...
Page 767: ...13 108 Chapter 13 Control Sub Functions MEMO...
Page 813: ...14 46 Chapter 14 Common Functions MEMO...
Page 831: ...15 18 Chapter 15 Dedicated Instructions MEMO...
Page 846: ...16 15 Chapter 16 Troubleshooting MEMO...
Page 892: ...16 61 Chapter 16 Troubleshooting MEMO...
Page 971: ...Appendix 62 Appendices MEMO...
Page 974: ......
Page 975: ......