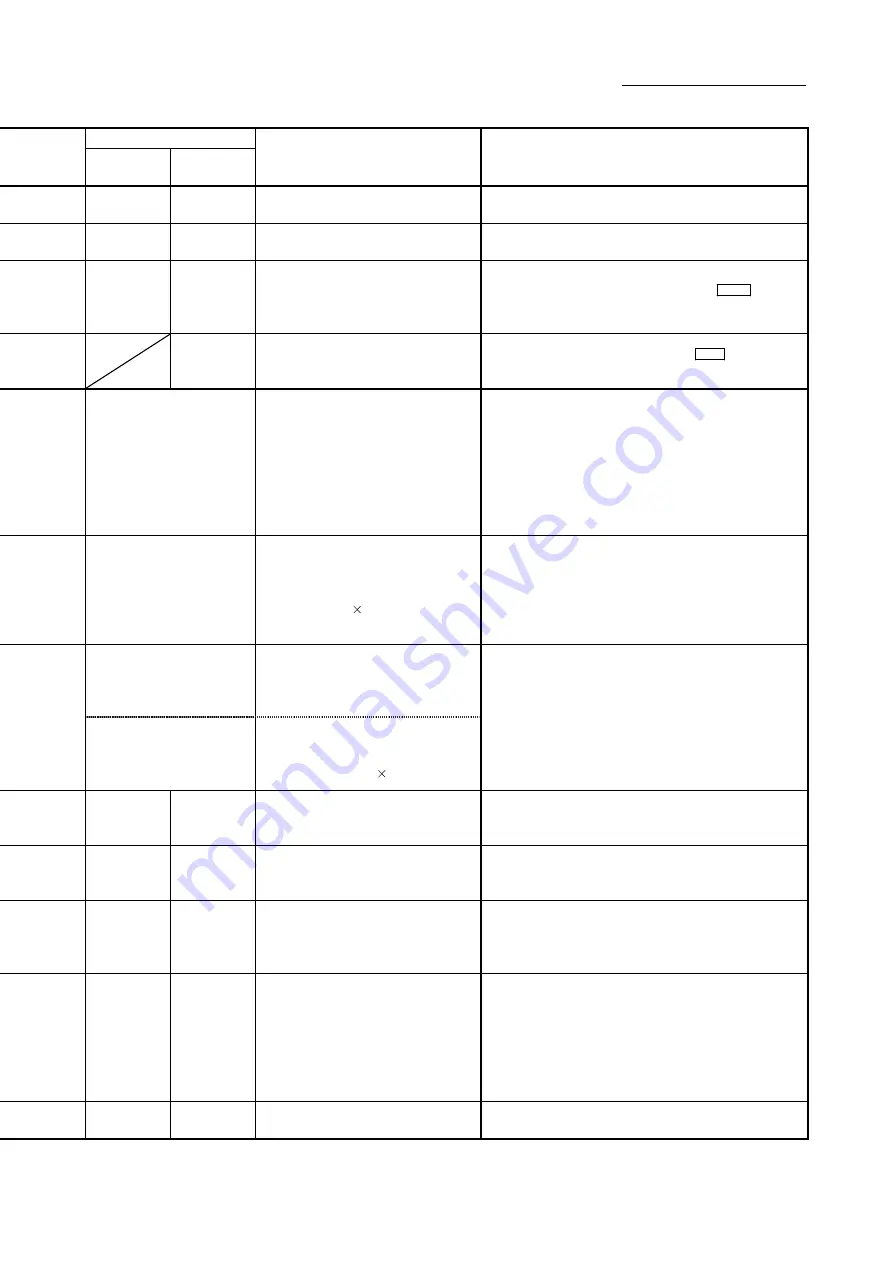
16 - 19
Chapter 16 Troubleshooting
Related buffer memory address
QD77MS2
QD77MS4
QD77MS16
Set range
(Setting with sequence program)
Remedy
— —
—
Turn ON the PLC READY signal [Y0] with the BUSY signals
of all axes OFF.
— —
—
Do not request the start when the axis operation state is other
than "standby", "stop", and "step standby".
30100+200n 28400+100n
<Servo series>
0, 1, 3, 4, 6, 7, 32, 96
Match the set series of the servo parameter "
Pr.100
Servo
series
" to the series of connected servo amplifier.
105
—
Review the content of the positioning or "
Pr.96
Operation cycle
setting
" longer than the current setting.
78+150n
<OPR retry>
0, 1
• Validate the OPR retry function (set value: 1). (Refer to
Section 13.2.1).
• Move the work piece from the current position (on OP) using
the manual control operation (refer to Chapter 11), then carry
out a machine OPR again.
74+150n
75+150n
<OPR speed>
1 to 1000000000 [PLS/s]
1 to 2000000000 [ 10
-2
mm/min or others]
• Lower the OPR speed.
• Increase the dog signal input time.
(Refer to Section 8.2.3)
80+150n
81+150n
<Movement amount setting after near-
point dog ON>
0 to 2147483647
74+150n
75+150n
<OPR speed>
1 to 1000000000 [PLS/s]
1 to 2000000000 [ 10
-2
mm/min]
• Calculate the movement distance using a speed limit, OPR
speed, and deceleration time, and set the movement amount
after near-point dog ON so that the distance becomes a
deceleration distance or longer.
• Lower the OPR speed.
• Adjust the near-point dog position so that the movement
amount after near-point dog ON becomes longer. (Refer to
Section 8.2.4, 8.2.5)
1500+100n 4300+100n
<Positioning start No.>
1 to 600, 7000 to 7004, 9001 to 9004
Execute the machine OPR (positioning start No. 9001). (Refer
to Section 8.2)
1500+100n 4300+100n
<Positioning start No.>
1 to 600, 7000 to 7004, 9001 to 9004
Start the machine OPR (positioning start No. 9001) again.
(Refer to Section 8.2)
— —
—
Turn the motor more than one revolution using JOG or
positioning operation.
— —
—
• Execute OPR again.
• When the servo parameter "Function selection C-4 (PC17)"
is changed to "1: Not need to pass motor Z-phase after the
power supply is switched on", transfer the parameter from
QD77MS to the servo amplifier and turn the power supply of
the servo amplifier OFF. Then, turn it ON and execute OPR
again.
—
—
—
Execute OPR again.
Summary of Contents for MELSEC-Q QD77MS
Page 1: ......
Page 27: ...A 26 MEMO...
Page 29: ...MEMO...
Page 101: ...3 34 Chapter 3 Specifications and Functions MEMO...
Page 232: ...5 111 Chapter 5 Data Used for Positioning Control MEMO...
Page 315: ...5 194 Chapter 5 Data Used for Positioning Control MEMO...
Page 337: ...6 22 Chapter 6 Sequence Program Used for Positioning Control...
Page 338: ...6 23 Chapter 6 Sequence Program Used for Positioning Control...
Page 339: ...6 24 Chapter 6 Sequence Program Used for Positioning Control...
Page 340: ...6 25 Chapter 6 Sequence Program Used for Positioning Control...
Page 341: ...6 26 Chapter 6 Sequence Program Used for Positioning Control...
Page 342: ...6 27 Chapter 6 Sequence Program Used for Positioning Control...
Page 343: ...6 28 Chapter 6 Sequence Program Used for Positioning Control...
Page 344: ...6 29 Chapter 6 Sequence Program Used for Positioning Control...
Page 345: ...6 30 Chapter 6 Sequence Program Used for Positioning Control...
Page 346: ...6 31 Chapter 6 Sequence Program Used for Positioning Control...
Page 347: ...6 32 Chapter 6 Sequence Program Used for Positioning Control...
Page 348: ...6 33 Chapter 6 Sequence Program Used for Positioning Control...
Page 349: ...6 34 Chapter 6 Sequence Program Used for Positioning Control...
Page 353: ...6 38 Chapter 6 Sequence Program Used for Positioning Control...
Page 354: ...6 39 Chapter 6 Sequence Program Used for Positioning Control...
Page 357: ...6 42 Chapter 6 Sequence Program Used for Positioning Control...
Page 359: ...6 44 Chapter 6 Sequence Program Used for Positioning Control...
Page 360: ...6 45 Chapter 6 Sequence Program Used for Positioning Control...
Page 361: ...6 46 Chapter 6 Sequence Program Used for Positioning Control...
Page 363: ...6 48 Chapter 6 Sequence Program Used for Positioning Control...
Page 364: ...6 49 Chapter 6 Sequence Program Used for Positioning Control...
Page 413: ...MEMO...
Page 433: ...8 20 Chapter 8 OPR Control MEMO...
Page 458: ...9 25 Chapter 9 Major Positioning Control MEMO...
Page 593: ...10 30 Chapter 10 High Level Positioning Control MEMO...
Page 625: ...11 32 Chapter 11 Manual Control MEMO...
Page 659: ...12 34 Chapter 12 Expansion Control MEMO...
Page 767: ...13 108 Chapter 13 Control Sub Functions MEMO...
Page 813: ...14 46 Chapter 14 Common Functions MEMO...
Page 831: ...15 18 Chapter 15 Dedicated Instructions MEMO...
Page 846: ...16 15 Chapter 16 Troubleshooting MEMO...
Page 892: ...16 61 Chapter 16 Troubleshooting MEMO...
Page 971: ...Appendix 62 Appendices MEMO...
Page 974: ......
Page 975: ......