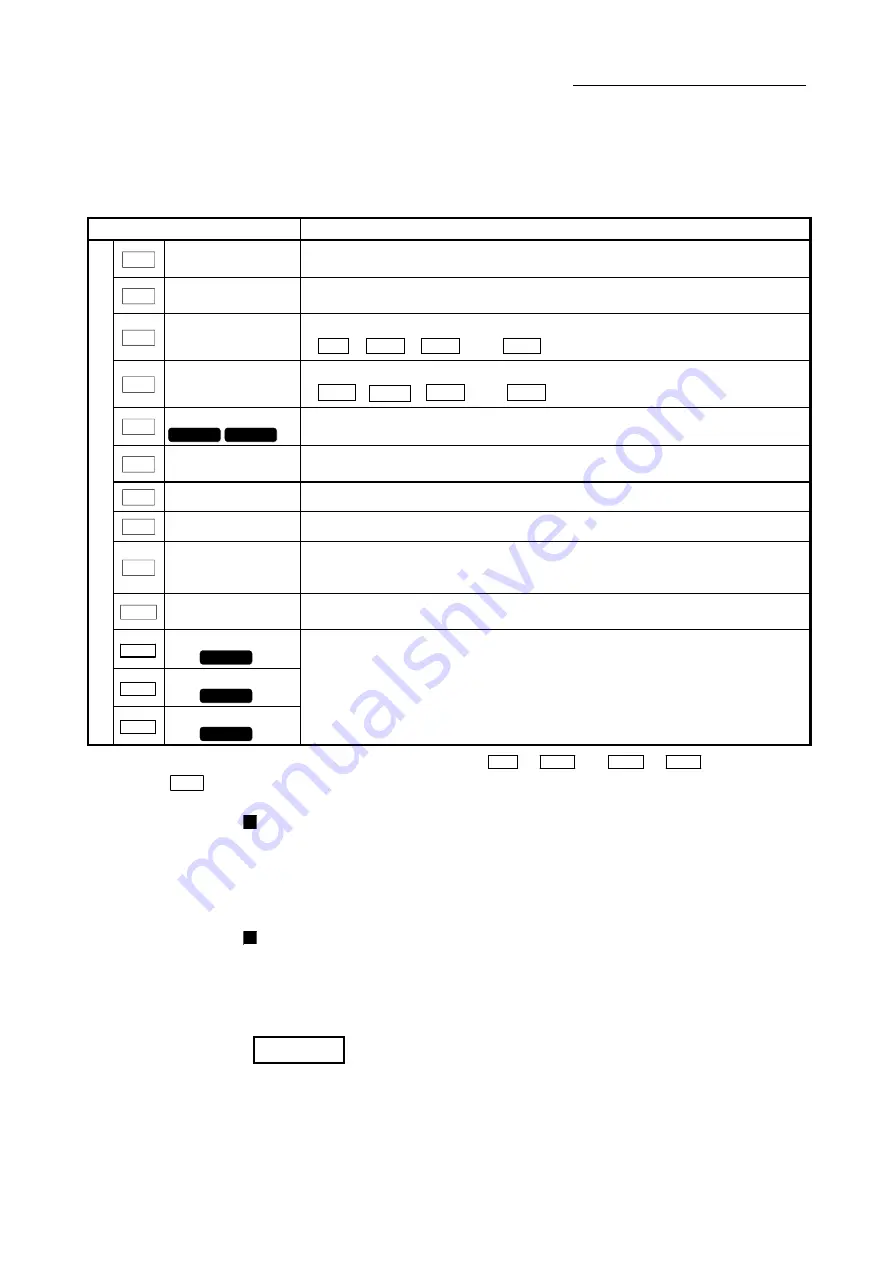
9 - 4
Chapter 9 Major Positioning Control
9.1.1 Data required for major positioning control
The following table shows an outline of the "positioning data" configuration and setting
details required to carry out the "major positioning controls".
Setting item
Setting details
Da.1 Operation pattern
Set the method by which the continuous positioning data (Ex: positioning data No.1,
No.2, No.3) will be controlled. (Refer to Section "9.1.2".)
Da.2 Control system
Set the control system defined as a "major positioning control". (Refer to Section
"9.1".)
Da.3 Acceleration time No.
Select and set the acceleration time at control start. (Select one of the four values set
in
Pr.9
,
Pr.25
,
Pr.26
, and
Pr.27
for the acceleration time.)
Da.4 Deceleration time No.
Select and set the deceleration time at control stop. (Select one of the four values set
in
Pr.10
, Pr.28 ,
Pr.29
, and
Pr.30
for the deceleration time.)
Da.5
Axis to be interpolated
QD77MS2
QD77MS4
Set an axis to be interpolated (partner axis) during the 2-axis interpolation operation
(Refer to Section 9.1.6.).
Da.6
Positioning address/
movement amount
Set the target value during position control. (Refer to Section "9.1.3".)
Da.7 Arc address
Set the sub point or center point address during circular interpolation control.
Da.8 Command speed
Set the speed during the control execution.
Da.9 Dwell time
The time between the command pulse output is completed to the positioning
completed signal is turned ON. Set it for absorbing the delay of the mechanical system
to the instruction, such as the delay of the servo system (deviation).
Da.10
M code
Set this item when carrying out sub work (clamp and drill stops, tool replacement, etc.)
corresponding to the code No. related to the positioning data execution.
Da.20
Axis to be interpolated
No.1
QD77MS16
Da.21
Axis to be interpolated
No.2
QD77MS16
Positioning data N
o. 1
Da.22
Axis to be interpolated
No.3
QD77MS16
Set an axis to be interpolated during the 2- to 4-axis interpolation operation.
(Refer to Section 9.1.6.)
(Note): The settings and setting requirement for the setting details of
Da.1
to
Da.10
and
Da.20
to
Da.22
differ according
to the "
Da.2
Control system". (Refer to Section 9.2 "Setting the positioning data".)
Major positioning control sub functions
Refer to Section 3.2.5 "Combination of QD77MS main functions and sub functions"
for details on "sub functions" that can be combined with the major positioning
control.
Also refer to Chapter 13 "Control Sub Functions" for details on each sub function.
Major positioning control from GX Works2
"Major positioning control" can be executed by test function of GX Works2.
Refer to "Simple Motion Module Setting Tool Help" of GX Works2 for details on
carrying out major positioning control from the GX Works2.
REMARK
600 positioning data (positioning data No. 1 to 600) items can be set per axis.
Summary of Contents for MELSEC-Q QD77MS
Page 1: ......
Page 27: ...A 26 MEMO...
Page 29: ...MEMO...
Page 101: ...3 34 Chapter 3 Specifications and Functions MEMO...
Page 232: ...5 111 Chapter 5 Data Used for Positioning Control MEMO...
Page 315: ...5 194 Chapter 5 Data Used for Positioning Control MEMO...
Page 337: ...6 22 Chapter 6 Sequence Program Used for Positioning Control...
Page 338: ...6 23 Chapter 6 Sequence Program Used for Positioning Control...
Page 339: ...6 24 Chapter 6 Sequence Program Used for Positioning Control...
Page 340: ...6 25 Chapter 6 Sequence Program Used for Positioning Control...
Page 341: ...6 26 Chapter 6 Sequence Program Used for Positioning Control...
Page 342: ...6 27 Chapter 6 Sequence Program Used for Positioning Control...
Page 343: ...6 28 Chapter 6 Sequence Program Used for Positioning Control...
Page 344: ...6 29 Chapter 6 Sequence Program Used for Positioning Control...
Page 345: ...6 30 Chapter 6 Sequence Program Used for Positioning Control...
Page 346: ...6 31 Chapter 6 Sequence Program Used for Positioning Control...
Page 347: ...6 32 Chapter 6 Sequence Program Used for Positioning Control...
Page 348: ...6 33 Chapter 6 Sequence Program Used for Positioning Control...
Page 349: ...6 34 Chapter 6 Sequence Program Used for Positioning Control...
Page 353: ...6 38 Chapter 6 Sequence Program Used for Positioning Control...
Page 354: ...6 39 Chapter 6 Sequence Program Used for Positioning Control...
Page 357: ...6 42 Chapter 6 Sequence Program Used for Positioning Control...
Page 359: ...6 44 Chapter 6 Sequence Program Used for Positioning Control...
Page 360: ...6 45 Chapter 6 Sequence Program Used for Positioning Control...
Page 361: ...6 46 Chapter 6 Sequence Program Used for Positioning Control...
Page 363: ...6 48 Chapter 6 Sequence Program Used for Positioning Control...
Page 364: ...6 49 Chapter 6 Sequence Program Used for Positioning Control...
Page 413: ...MEMO...
Page 433: ...8 20 Chapter 8 OPR Control MEMO...
Page 458: ...9 25 Chapter 9 Major Positioning Control MEMO...
Page 593: ...10 30 Chapter 10 High Level Positioning Control MEMO...
Page 625: ...11 32 Chapter 11 Manual Control MEMO...
Page 659: ...12 34 Chapter 12 Expansion Control MEMO...
Page 767: ...13 108 Chapter 13 Control Sub Functions MEMO...
Page 813: ...14 46 Chapter 14 Common Functions MEMO...
Page 831: ...15 18 Chapter 15 Dedicated Instructions MEMO...
Page 846: ...16 15 Chapter 16 Troubleshooting MEMO...
Page 892: ...16 61 Chapter 16 Troubleshooting MEMO...
Page 971: ...Appendix 62 Appendices MEMO...
Page 974: ......
Page 975: ......