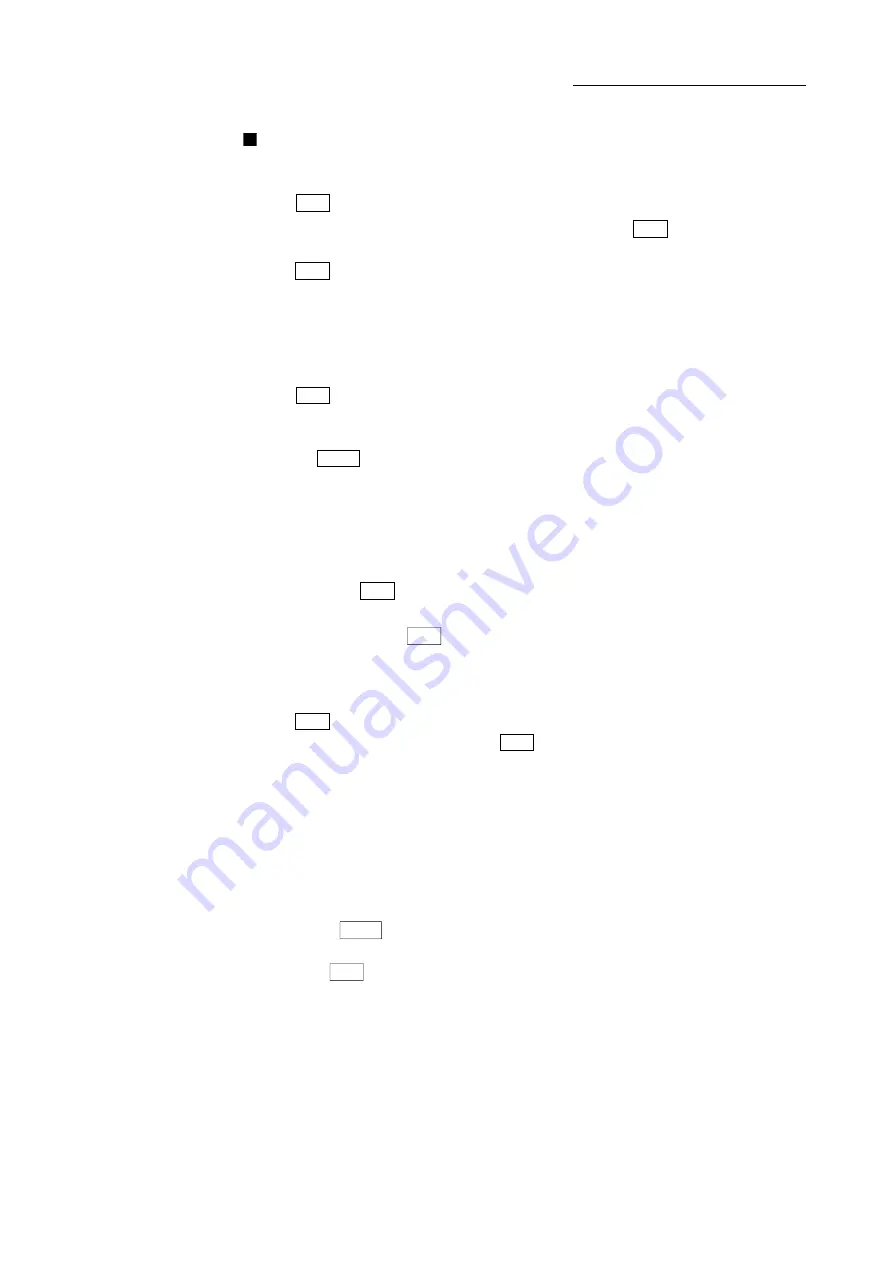
9 - 100
Chapter 9 Major Positioning Control
Restrictions
(1) An axis error (error code: 516) will occur and the operation cannot start if
"continuous positioning control" or "continuous path control" is set in
"
Da.1
Operation pattern".
(2) "Speed-position switching control" cannot be set in "
Da.2
Control system" of
the positioning data when "continuous path control" has been set in
"
Da.1
Operation pattern" of the immediately prior positioning data. (For
example, if the operation pattern of positioning data No. 1 is "continuous path
control", "speed-position switching control" cannot be set in positioning data
No. 2.) An axis error (error code: 516) will occur and the machine will carry out
a deceleration stop if this type of setting is carried out.
(3) An error (error code: 503) will occur if "current speed (-1)" is set in
"
Da.8
Command speed".
(4) The software stroke limit range check during speed control is made only when
the following (a) and (b) are satisfied:
(a) "
Pr.21
Current feed value during speed control" is "1: Update current feed
value".
If the movement amount exceeds the software stroke limit range during
speed control in case of the setting of other than "1: Update current feed
value", an error (error code: 507 or 508) will occur as soon as speed control
is changed to position control and the axis will decelerate to a stop.
(b) When "
Pr.1
Unit setting" is other than "2: degree"
If the unit is "degree", the software stroke limit range check is not performed.
(5) If the value set in "
Da.6
Positioning address/movement amount" is negative, an
error (error code: 530) will occur.
(6) Deceleration processing is carried out from the point where the speed-position
switching signal is input if the position control movement amount set in
"
Da.6
Positioning address/movement amount" is smaller than the
deceleration distance from the "
Da.8
Command speed".
(7) Turn ON the speed-position switching signal in the speed stabilization region
(constant speed status). A warning (warning code: 508) will occur because of
large deviation in the droop pulse amount if the signal is turned ON during
acceleration.
During use of the servo motor, the actual movement amount after switching of
speed control to position control is the "preset movement droop
pulse amount". If the signal is turned ON during acceleration/deceleration, the
stop position will vary due to large variation of the droop pulse amount. Even
though "
Md.29
Speed-position switching control positioning amount" is the
same, the stop position will change due to a change in droop pulse amount
when "
Da.8
Command speed" is different.
Summary of Contents for MELSEC-Q QD77MS
Page 1: ......
Page 27: ...A 26 MEMO...
Page 29: ...MEMO...
Page 101: ...3 34 Chapter 3 Specifications and Functions MEMO...
Page 232: ...5 111 Chapter 5 Data Used for Positioning Control MEMO...
Page 315: ...5 194 Chapter 5 Data Used for Positioning Control MEMO...
Page 337: ...6 22 Chapter 6 Sequence Program Used for Positioning Control...
Page 338: ...6 23 Chapter 6 Sequence Program Used for Positioning Control...
Page 339: ...6 24 Chapter 6 Sequence Program Used for Positioning Control...
Page 340: ...6 25 Chapter 6 Sequence Program Used for Positioning Control...
Page 341: ...6 26 Chapter 6 Sequence Program Used for Positioning Control...
Page 342: ...6 27 Chapter 6 Sequence Program Used for Positioning Control...
Page 343: ...6 28 Chapter 6 Sequence Program Used for Positioning Control...
Page 344: ...6 29 Chapter 6 Sequence Program Used for Positioning Control...
Page 345: ...6 30 Chapter 6 Sequence Program Used for Positioning Control...
Page 346: ...6 31 Chapter 6 Sequence Program Used for Positioning Control...
Page 347: ...6 32 Chapter 6 Sequence Program Used for Positioning Control...
Page 348: ...6 33 Chapter 6 Sequence Program Used for Positioning Control...
Page 349: ...6 34 Chapter 6 Sequence Program Used for Positioning Control...
Page 353: ...6 38 Chapter 6 Sequence Program Used for Positioning Control...
Page 354: ...6 39 Chapter 6 Sequence Program Used for Positioning Control...
Page 357: ...6 42 Chapter 6 Sequence Program Used for Positioning Control...
Page 359: ...6 44 Chapter 6 Sequence Program Used for Positioning Control...
Page 360: ...6 45 Chapter 6 Sequence Program Used for Positioning Control...
Page 361: ...6 46 Chapter 6 Sequence Program Used for Positioning Control...
Page 363: ...6 48 Chapter 6 Sequence Program Used for Positioning Control...
Page 364: ...6 49 Chapter 6 Sequence Program Used for Positioning Control...
Page 413: ...MEMO...
Page 433: ...8 20 Chapter 8 OPR Control MEMO...
Page 458: ...9 25 Chapter 9 Major Positioning Control MEMO...
Page 593: ...10 30 Chapter 10 High Level Positioning Control MEMO...
Page 625: ...11 32 Chapter 11 Manual Control MEMO...
Page 659: ...12 34 Chapter 12 Expansion Control MEMO...
Page 767: ...13 108 Chapter 13 Control Sub Functions MEMO...
Page 813: ...14 46 Chapter 14 Common Functions MEMO...
Page 831: ...15 18 Chapter 15 Dedicated Instructions MEMO...
Page 846: ...16 15 Chapter 16 Troubleshooting MEMO...
Page 892: ...16 61 Chapter 16 Troubleshooting MEMO...
Page 971: ...Appendix 62 Appendices MEMO...
Page 974: ......
Page 975: ......