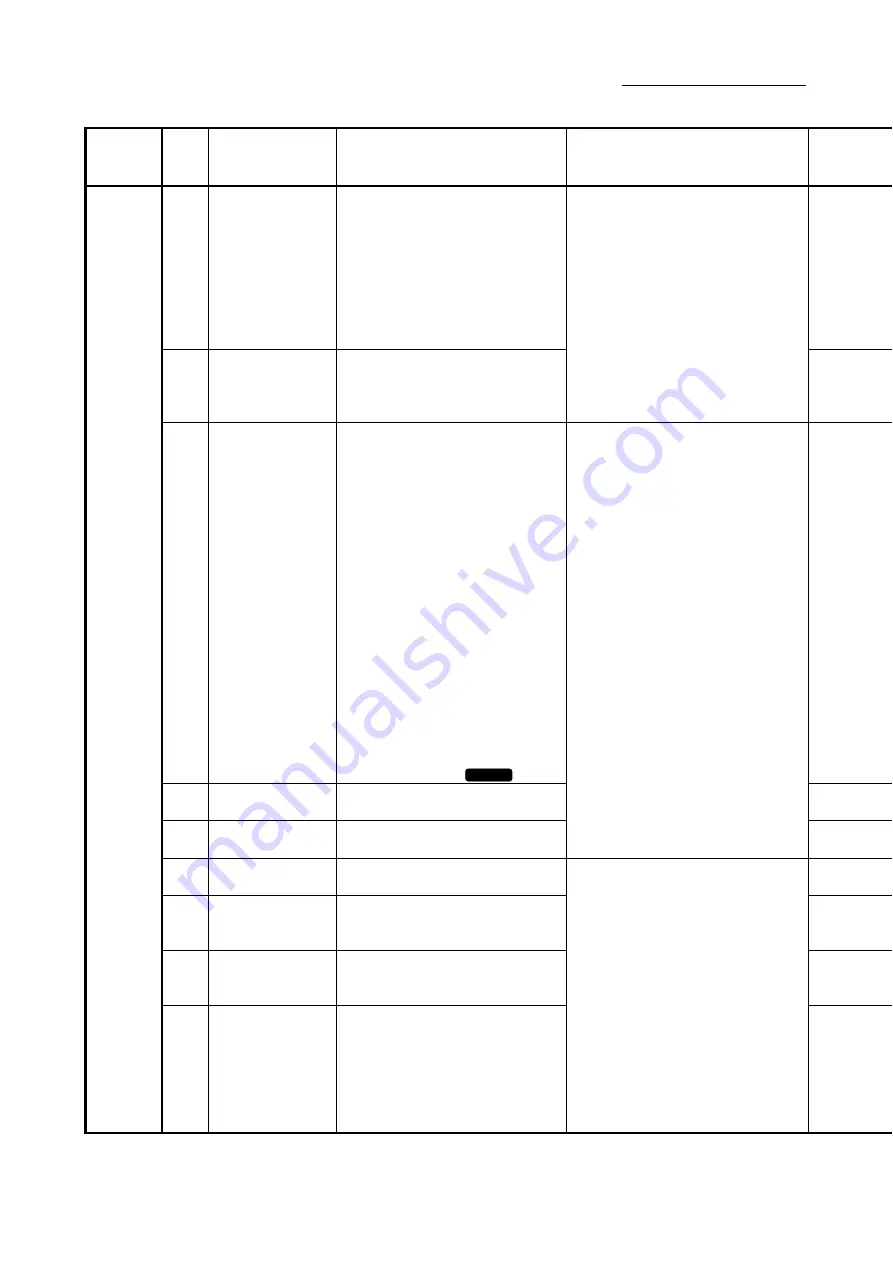
16 - 30
Chapter 16 Troubleshooting
Classification
of errors
Error
code
Error name
Error
Operation status at error occurrence
530 Outside address range
• In the speed-position switching control
and the position-speed switching control,
the setting value of a positioning address
is negative.
• In ABS1, ABS2, ABS3 and ABS4, the
setting value of a positioning address is
outside the range of 0 to 359.99999
degrees.
532
Simultaneous start not
possible
Among the axes to be started
simultaneously, there is an axis on which
an error other than this error occurs.
At start
: The system does not
operate.
During operation : The system stops
immediately with the setting
(deceleration stop/sudden
stop) of the detailed
parameter 2 sudden stop
selection
(stop group 3).
(Note that the deceleration
stop only occurs during the
manual pulse generator
operation.)
533 Condition data error
• The condition setting values are not set or
outside the setting range.
• The condition operator setting values are
not set or outside the setting range.
• The condition operator is a bit operator,
and the parameter 1 is 32 or more.
• An unusable condition operator is set for
the set condition.
• The conditional operator has been
[parameter 1 is greater than to parameter
2] with 05H (P1
≤
**
≤
P2).
• The setting value of "address" is outside
the setting range when the condition
target is set to "Buffer memory (1-word/2-
word)".
(1-word: 0 to 32767, 2-word: 0 to 32766)
• The setting value of "simultaneous
starting axis" is outside the setting range
when the condition target is set to
"positioning data No.".
QD77MS16
534
Special start instruction
error
No applicable special start instruction is
present.
535
Circular interpolation
not possible
Circular interpolation is carried out on an
axis in the unit of degree.
The operation is terminated.
536 M code ON signal start
The positioning start is carried out when an
M code ON signal is turned ON.
537 PLC READY OFF start
The positioning start is carried out when
the PLC READY signal [Y0] is turned OFF.
538 READY OFF start
The positioning start is carried out when
the QD77 READY signal [X0] is turned
OFF.
Positioning
operation
errors
543 Outside start No. range
• At the start of positioning, the setting
value of the "positioning start No." of the
axis control data is outside the ranges of
1 to 600, 7000 to 7004, and 9001 to 9004.
• At a Pre-reading start, the "positioning
start No." setting of the axis control data is
other than 1 to 600.
The system does not operate at start.
Summary of Contents for MELSEC-Q QD77MS
Page 1: ......
Page 27: ...A 26 MEMO...
Page 29: ...MEMO...
Page 101: ...3 34 Chapter 3 Specifications and Functions MEMO...
Page 232: ...5 111 Chapter 5 Data Used for Positioning Control MEMO...
Page 315: ...5 194 Chapter 5 Data Used for Positioning Control MEMO...
Page 337: ...6 22 Chapter 6 Sequence Program Used for Positioning Control...
Page 338: ...6 23 Chapter 6 Sequence Program Used for Positioning Control...
Page 339: ...6 24 Chapter 6 Sequence Program Used for Positioning Control...
Page 340: ...6 25 Chapter 6 Sequence Program Used for Positioning Control...
Page 341: ...6 26 Chapter 6 Sequence Program Used for Positioning Control...
Page 342: ...6 27 Chapter 6 Sequence Program Used for Positioning Control...
Page 343: ...6 28 Chapter 6 Sequence Program Used for Positioning Control...
Page 344: ...6 29 Chapter 6 Sequence Program Used for Positioning Control...
Page 345: ...6 30 Chapter 6 Sequence Program Used for Positioning Control...
Page 346: ...6 31 Chapter 6 Sequence Program Used for Positioning Control...
Page 347: ...6 32 Chapter 6 Sequence Program Used for Positioning Control...
Page 348: ...6 33 Chapter 6 Sequence Program Used for Positioning Control...
Page 349: ...6 34 Chapter 6 Sequence Program Used for Positioning Control...
Page 353: ...6 38 Chapter 6 Sequence Program Used for Positioning Control...
Page 354: ...6 39 Chapter 6 Sequence Program Used for Positioning Control...
Page 357: ...6 42 Chapter 6 Sequence Program Used for Positioning Control...
Page 359: ...6 44 Chapter 6 Sequence Program Used for Positioning Control...
Page 360: ...6 45 Chapter 6 Sequence Program Used for Positioning Control...
Page 361: ...6 46 Chapter 6 Sequence Program Used for Positioning Control...
Page 363: ...6 48 Chapter 6 Sequence Program Used for Positioning Control...
Page 364: ...6 49 Chapter 6 Sequence Program Used for Positioning Control...
Page 413: ...MEMO...
Page 433: ...8 20 Chapter 8 OPR Control MEMO...
Page 458: ...9 25 Chapter 9 Major Positioning Control MEMO...
Page 593: ...10 30 Chapter 10 High Level Positioning Control MEMO...
Page 625: ...11 32 Chapter 11 Manual Control MEMO...
Page 659: ...12 34 Chapter 12 Expansion Control MEMO...
Page 767: ...13 108 Chapter 13 Control Sub Functions MEMO...
Page 813: ...14 46 Chapter 14 Common Functions MEMO...
Page 831: ...15 18 Chapter 15 Dedicated Instructions MEMO...
Page 846: ...16 15 Chapter 16 Troubleshooting MEMO...
Page 892: ...16 61 Chapter 16 Troubleshooting MEMO...
Page 971: ...Appendix 62 Appendices MEMO...
Page 974: ......
Page 975: ......