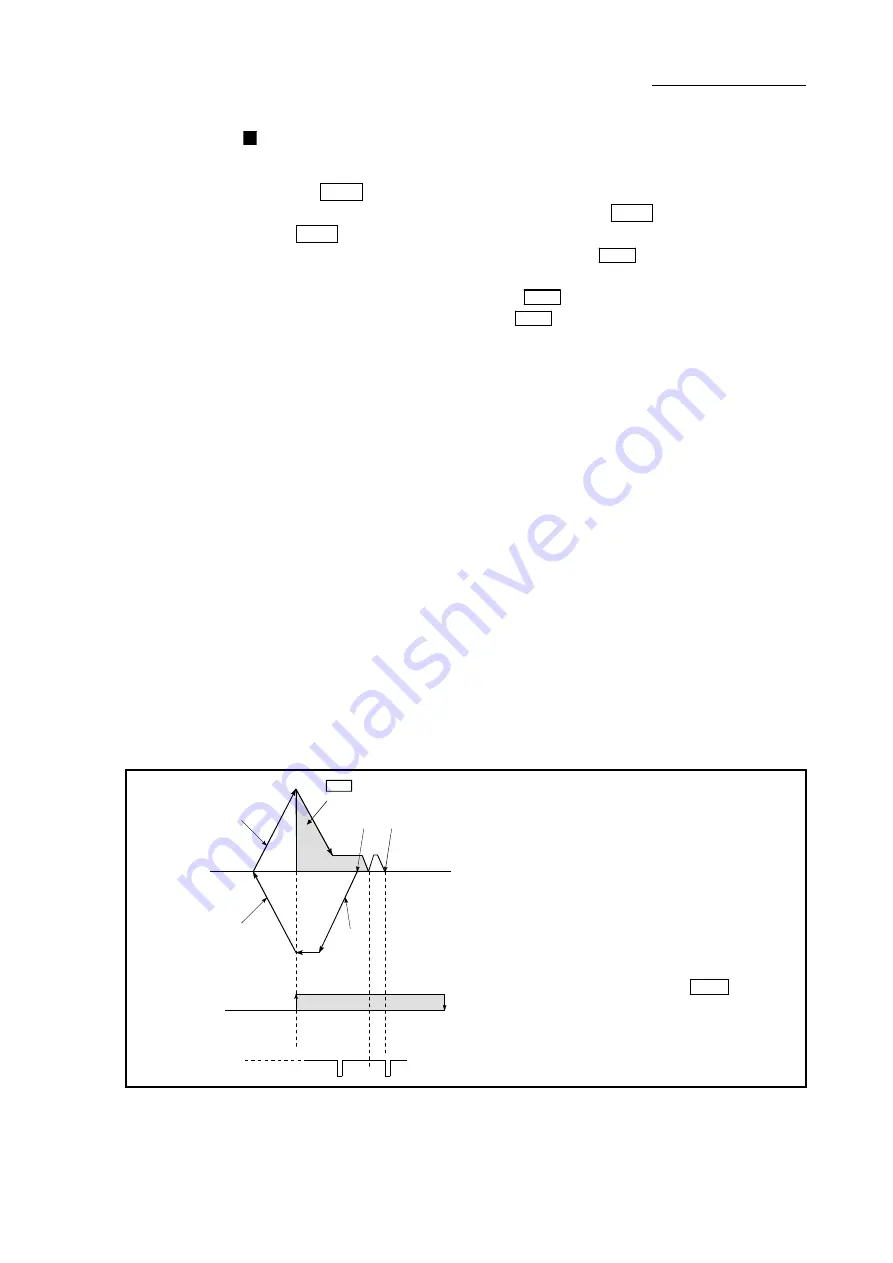
8 - 10
Chapter 8 OPR Control
Precautions during operation
(1) An error "Count method movement amount fault (error code: 206)" will occur if
the "
Pr.50
Setting for the movement amount after near-point dog ON" is
smaller than the deceleration distance from the "
Pr.46
OPR speed" to
"
Pr.47
Creep speed".
(2) If the speed is changed to a speed faster than "
Pr.46
OPR speed
" by the speed
change function (refer to "13.5.1 Speed change function".) during a machine
OPR, the distance to decelerate to "
Pr.47
Creep speed
" may not be ensured,
depending on the setting value of "
Pr.50
Setting for the movement amount after
near-point dog ON
". In this case, the error "Count method movement amount
fault" (error code: 206) occurs and the machine OPR is stopped.
(3) The following shows the operation when a machine OPR is started while the
near-point dog is ON.
(4) Turn OFF the near-point dog at a sufficient distance from the OP.
Although there is no harm in operation if the near-point dog is turned OFF
during a machine OPR, it is recommended to leave a sufficient distance from
the OP when the near-point dog is turned OFF for the following reason.
If machine OPRs are performed consecutively after the near-point dog is
turned OFF at the time of machine OPR completion, operation will be
performed at the OPR speed until the hardware stroke limit (upper/lower limit)
is reached.
If a sufficient distance cannot be kept, consider the use of the OPR retry
function.
(5) When the stop signal stops the machine OPR, carry out the machine OPR
again. When restart command is turned ON after the stop signal stops the
OPR, the error "OPR restart impossible (error code: 209)" will occur.
(6) After the home position return (OPR) has been started, the zero point of the
encoder must be passed at least once before point A is reached.
However, if selecting "1: Not need to pass motor Z-phase after the power
supply is switched on." with "Function selection C-4 (PC17)", it is possible to
carried out the home position return (OPR) without passing the zero point.
ON
1)
5)
4)
3)
2)
Zero signal
Near-point dog OFF
Pr. 50 Setting for the movement
amount after near-point dog ON
[Operation when a machine OPR is started at the
near-point dog ON position]
1) A machine OPR is started.
2) The machine moves at the OPR speed in the
opposite direction of an OPR.
3) Deceleration processing is carried out when
the near-point dog OFF is detected.
4) After the machine stops, a machine OPR is
carried out in the OPR direction.
5) The machine OPR is completed on detection
of the first zero signal after the travel of the
movement amount set to "
Pr.50
Setting for
the movement amount after near-point dog
ON" on detection of the near-point dog signal
ON.
Fig. 8.6 Count method 1) machine OPR on the near-point dog ON position
Summary of Contents for MELSEC-Q QD77MS
Page 1: ......
Page 27: ...A 26 MEMO...
Page 29: ...MEMO...
Page 101: ...3 34 Chapter 3 Specifications and Functions MEMO...
Page 232: ...5 111 Chapter 5 Data Used for Positioning Control MEMO...
Page 315: ...5 194 Chapter 5 Data Used for Positioning Control MEMO...
Page 337: ...6 22 Chapter 6 Sequence Program Used for Positioning Control...
Page 338: ...6 23 Chapter 6 Sequence Program Used for Positioning Control...
Page 339: ...6 24 Chapter 6 Sequence Program Used for Positioning Control...
Page 340: ...6 25 Chapter 6 Sequence Program Used for Positioning Control...
Page 341: ...6 26 Chapter 6 Sequence Program Used for Positioning Control...
Page 342: ...6 27 Chapter 6 Sequence Program Used for Positioning Control...
Page 343: ...6 28 Chapter 6 Sequence Program Used for Positioning Control...
Page 344: ...6 29 Chapter 6 Sequence Program Used for Positioning Control...
Page 345: ...6 30 Chapter 6 Sequence Program Used for Positioning Control...
Page 346: ...6 31 Chapter 6 Sequence Program Used for Positioning Control...
Page 347: ...6 32 Chapter 6 Sequence Program Used for Positioning Control...
Page 348: ...6 33 Chapter 6 Sequence Program Used for Positioning Control...
Page 349: ...6 34 Chapter 6 Sequence Program Used for Positioning Control...
Page 353: ...6 38 Chapter 6 Sequence Program Used for Positioning Control...
Page 354: ...6 39 Chapter 6 Sequence Program Used for Positioning Control...
Page 357: ...6 42 Chapter 6 Sequence Program Used for Positioning Control...
Page 359: ...6 44 Chapter 6 Sequence Program Used for Positioning Control...
Page 360: ...6 45 Chapter 6 Sequence Program Used for Positioning Control...
Page 361: ...6 46 Chapter 6 Sequence Program Used for Positioning Control...
Page 363: ...6 48 Chapter 6 Sequence Program Used for Positioning Control...
Page 364: ...6 49 Chapter 6 Sequence Program Used for Positioning Control...
Page 413: ...MEMO...
Page 433: ...8 20 Chapter 8 OPR Control MEMO...
Page 458: ...9 25 Chapter 9 Major Positioning Control MEMO...
Page 593: ...10 30 Chapter 10 High Level Positioning Control MEMO...
Page 625: ...11 32 Chapter 11 Manual Control MEMO...
Page 659: ...12 34 Chapter 12 Expansion Control MEMO...
Page 767: ...13 108 Chapter 13 Control Sub Functions MEMO...
Page 813: ...14 46 Chapter 14 Common Functions MEMO...
Page 831: ...15 18 Chapter 15 Dedicated Instructions MEMO...
Page 846: ...16 15 Chapter 16 Troubleshooting MEMO...
Page 892: ...16 61 Chapter 16 Troubleshooting MEMO...
Page 971: ...Appendix 62 Appendices MEMO...
Page 974: ......
Page 975: ......