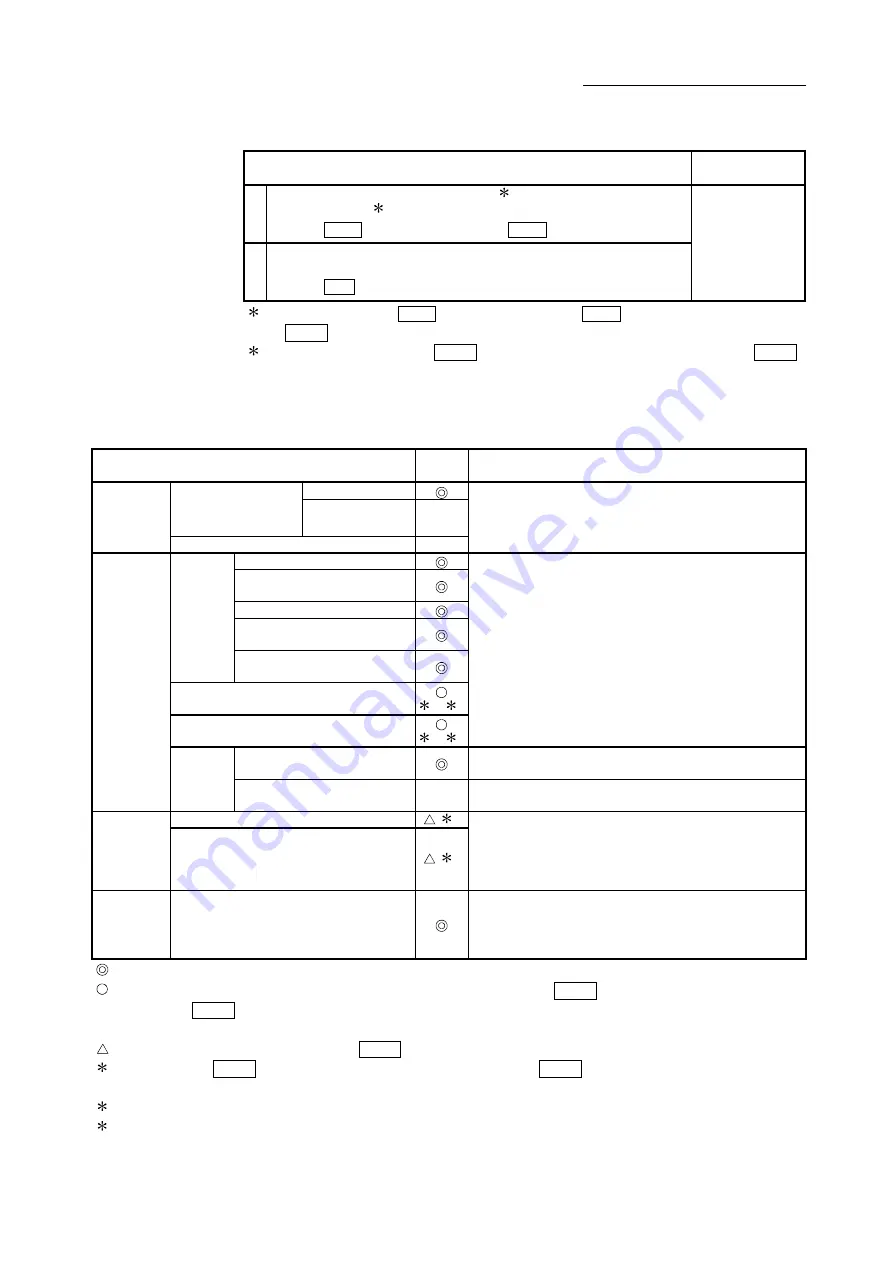
13 - 31
Chapter 13 Control Sub Functions
[2] Software stroke limit check details
Check details
Processing when
an error occurs
1)
An error shall occur if the current value 1 is outside the software
stroke limit range 2.
(Check "
Md.20
Current feed value" or "
Md.21
Machine feed value".)
2)
An error shall occur if the command address is outside the software
stroke limit range.
(Check "
Da.6
Positioning address/movement amount".)
An "axis error" will
occur (error code:
507, 508)
1: Check whether the "
Md.20
Current feed value" or "
Md.21
Machine feed value" is set in
" Pr.14 Software stroke limit selection".
2: Moveable range from the " Pr.12 Software stroke limit upper limit value" to the " Pr.13
Software stroke limit lower limit value".
[3] Relation between the software stroke limit function and various
controls
Control type
Limit
check
Processing at check
Data set method
Machine OPR control Other than "Data
set method"
–
OPR control
Fast OPR control
–
Check not carried out.
1-axis linear control
2 to 4-axes axis linear
interpolation control
1-axis fixed-feed control
2 to 4-axes fixed-feed control
(interpolation)
Position
control
2-axis circular interpolation
control
1 to 4-axes speed control
3, 4
Speed-position switching control
Position-speed switching control
3, 4
Checks 1) and 2) in the previous section [2] are carried
out.
For speed control: The axis decelerates to a stop when
it exceeds the software stroke limit
range.
For position control: The axis comes to an immediate
stop when it exceeds the software
stroke limit range.
Current value changing
The current value will not be changed if the new current
value is outside the software stroke limit range.
Major
positioning
control
Other
control
JUMP instruction, NOP
instruction, LOOP to LEND
–
Check not carried out.
JOG operation, Inching operation
5
Manual
control
Manual pulse generator operation
5
Check 1) in the previous section [2] is carried out.
The machine will carry out a deceleration stop when the
software stroke limit range is exceeded. If the address is
outside the software stroke limit range, the operation can
only be started toward the moveable range.
Expansion
control
Speed-torque control
Check 1) in the previous section [2] is carried out.
The mode is switched to position control mode when the
software stroke limit range is exceeded, then the
operation is immediately stop.
: Check valid
: Check is not made when the current feed value is not updated (Refer to Pr.21 ) at the setting of " current feed
value" in " Pr.14 Software stroke limit selection" during speed control.
– : Check not carried out (check invalid).
: Valid only when "0: valid" is set in the " Pr.15 Software stroke limit valid/invalid setting".
3 : The value in " Md.20 Current feed value" will differ according to the " Pr.21 Current feed value during speed
control" setting.
4: When the unit is "degree", check is not made during speed control.
5: When the unit is "degree", check is not carried out.
Summary of Contents for MELSEC-Q QD77MS
Page 1: ......
Page 27: ...A 26 MEMO...
Page 29: ...MEMO...
Page 101: ...3 34 Chapter 3 Specifications and Functions MEMO...
Page 232: ...5 111 Chapter 5 Data Used for Positioning Control MEMO...
Page 315: ...5 194 Chapter 5 Data Used for Positioning Control MEMO...
Page 337: ...6 22 Chapter 6 Sequence Program Used for Positioning Control...
Page 338: ...6 23 Chapter 6 Sequence Program Used for Positioning Control...
Page 339: ...6 24 Chapter 6 Sequence Program Used for Positioning Control...
Page 340: ...6 25 Chapter 6 Sequence Program Used for Positioning Control...
Page 341: ...6 26 Chapter 6 Sequence Program Used for Positioning Control...
Page 342: ...6 27 Chapter 6 Sequence Program Used for Positioning Control...
Page 343: ...6 28 Chapter 6 Sequence Program Used for Positioning Control...
Page 344: ...6 29 Chapter 6 Sequence Program Used for Positioning Control...
Page 345: ...6 30 Chapter 6 Sequence Program Used for Positioning Control...
Page 346: ...6 31 Chapter 6 Sequence Program Used for Positioning Control...
Page 347: ...6 32 Chapter 6 Sequence Program Used for Positioning Control...
Page 348: ...6 33 Chapter 6 Sequence Program Used for Positioning Control...
Page 349: ...6 34 Chapter 6 Sequence Program Used for Positioning Control...
Page 353: ...6 38 Chapter 6 Sequence Program Used for Positioning Control...
Page 354: ...6 39 Chapter 6 Sequence Program Used for Positioning Control...
Page 357: ...6 42 Chapter 6 Sequence Program Used for Positioning Control...
Page 359: ...6 44 Chapter 6 Sequence Program Used for Positioning Control...
Page 360: ...6 45 Chapter 6 Sequence Program Used for Positioning Control...
Page 361: ...6 46 Chapter 6 Sequence Program Used for Positioning Control...
Page 363: ...6 48 Chapter 6 Sequence Program Used for Positioning Control...
Page 364: ...6 49 Chapter 6 Sequence Program Used for Positioning Control...
Page 413: ...MEMO...
Page 433: ...8 20 Chapter 8 OPR Control MEMO...
Page 458: ...9 25 Chapter 9 Major Positioning Control MEMO...
Page 593: ...10 30 Chapter 10 High Level Positioning Control MEMO...
Page 625: ...11 32 Chapter 11 Manual Control MEMO...
Page 659: ...12 34 Chapter 12 Expansion Control MEMO...
Page 767: ...13 108 Chapter 13 Control Sub Functions MEMO...
Page 813: ...14 46 Chapter 14 Common Functions MEMO...
Page 831: ...15 18 Chapter 15 Dedicated Instructions MEMO...
Page 846: ...16 15 Chapter 16 Troubleshooting MEMO...
Page 892: ...16 61 Chapter 16 Troubleshooting MEMO...
Page 971: ...Appendix 62 Appendices MEMO...
Page 974: ......
Page 975: ......