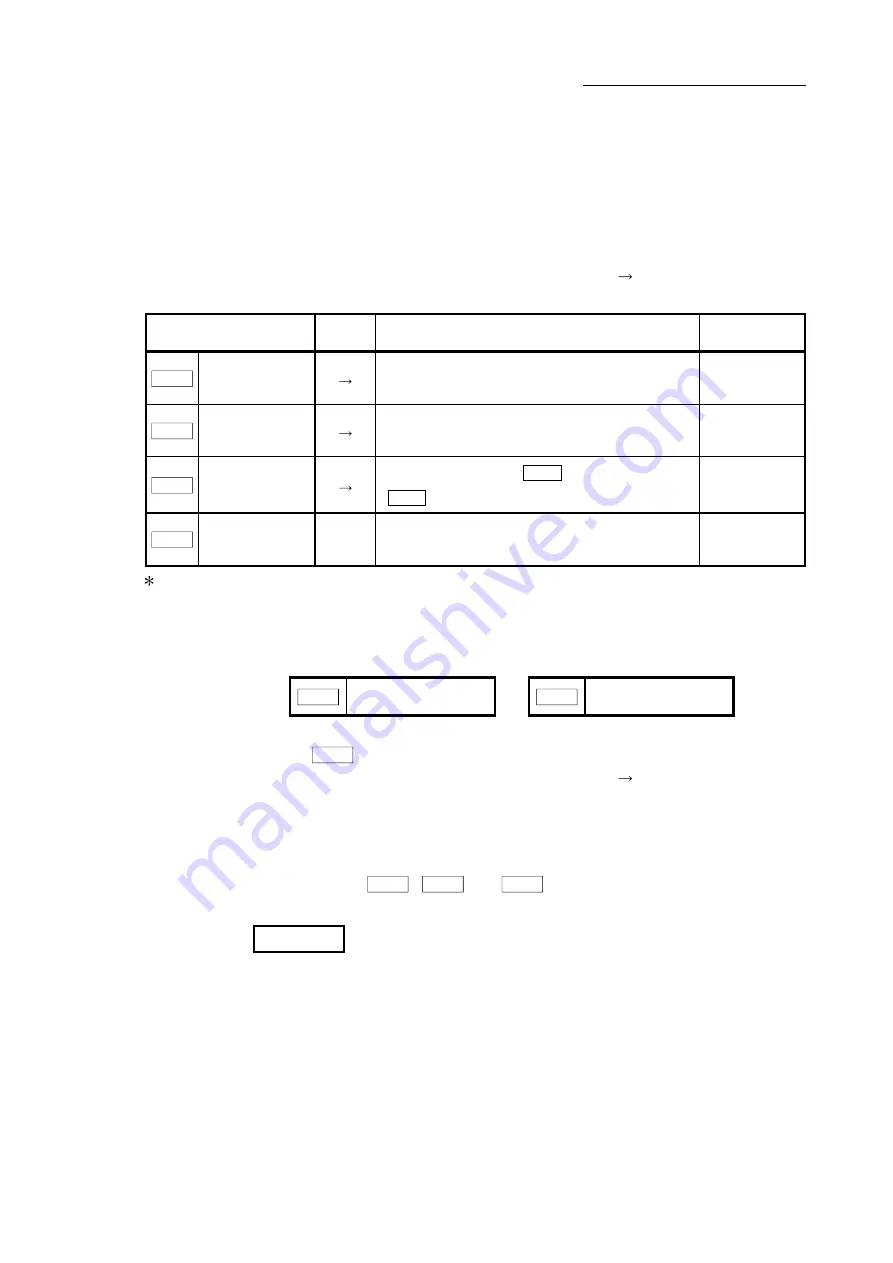
13 - 33
Chapter 13 Control Sub Functions
(5) During simultaneous start, a stroke limit check is carried out for the current
values of every axis to be started. Every axis will not start if an error occurs,
even if it only occurs in one axis.
[5] Setting the software stroke limit function
To use the "software stroke limit function", set the required values in the
parameters shown in the following table, and write them to the QD77MS.
The set details are validated at the rising edge (OFF ON) of the PLC READY
signal [Y0].
Setting item
Setting
value
Setting details
Factory-set
initial value
Pr.12
Software stroke
limit upper limit
value
Set the upper limit value of the moveable range.
2147483647
Pr.13
Software stroke
limit lower limit
value
Set the lower limit value of the moveable range.
–2147483648
Pr.14
Software stroke
limit selection
Set whether to use the "
Md.20
Current feed value" or
"
Md.21
Machine feed value" as the "current value".
0: Current feed
value
Pr.15
Software stroke
limit valid/invalid
setting
0:Valid
Set whether the software stroke limit is validated or
invalidated during manual control (JOG operation,
Inching operation, manual pulse generator operation).
0: valid
:
Refer to Section 5.2 "List of parameters" for setting details.
[6] Invalidating the software stroke limit
To invalidate the software stroke limit, set the following parameters as shown,
and write them to the QD77MS. (Set the value within the setting range.)
Pr.12
Software stroke limit
upper limit value
=
Pr.13
Software stroke limit
lower limit value
(To invalidate only the manual operation, set "1: software stroke limit invalid" in
the "
Pr.15
Software stroke limit valid/invalid setting".)
The set details are validated at the rising edge (OFF ON) of the PLC READY
signal [Y0].
When the unit is "degree", the software stroke limit check is not performed during
speed control (including speed control in speed-position switching control or
position-speed switching control) or during manual control, independently of the
values set in
Pr.12
,
Pr.13
and
Pr.15
.
REMARK
•
Parameters are set for each axis.
•
It is recommended that the parameters be set whenever possible with GX Works2.
Execution by sequence program uses many sequence programs and devices. The
execution becomes complicated, and the scan times will increase.
Summary of Contents for MELSEC-Q QD77MS
Page 1: ......
Page 27: ...A 26 MEMO...
Page 29: ...MEMO...
Page 101: ...3 34 Chapter 3 Specifications and Functions MEMO...
Page 232: ...5 111 Chapter 5 Data Used for Positioning Control MEMO...
Page 315: ...5 194 Chapter 5 Data Used for Positioning Control MEMO...
Page 337: ...6 22 Chapter 6 Sequence Program Used for Positioning Control...
Page 338: ...6 23 Chapter 6 Sequence Program Used for Positioning Control...
Page 339: ...6 24 Chapter 6 Sequence Program Used for Positioning Control...
Page 340: ...6 25 Chapter 6 Sequence Program Used for Positioning Control...
Page 341: ...6 26 Chapter 6 Sequence Program Used for Positioning Control...
Page 342: ...6 27 Chapter 6 Sequence Program Used for Positioning Control...
Page 343: ...6 28 Chapter 6 Sequence Program Used for Positioning Control...
Page 344: ...6 29 Chapter 6 Sequence Program Used for Positioning Control...
Page 345: ...6 30 Chapter 6 Sequence Program Used for Positioning Control...
Page 346: ...6 31 Chapter 6 Sequence Program Used for Positioning Control...
Page 347: ...6 32 Chapter 6 Sequence Program Used for Positioning Control...
Page 348: ...6 33 Chapter 6 Sequence Program Used for Positioning Control...
Page 349: ...6 34 Chapter 6 Sequence Program Used for Positioning Control...
Page 353: ...6 38 Chapter 6 Sequence Program Used for Positioning Control...
Page 354: ...6 39 Chapter 6 Sequence Program Used for Positioning Control...
Page 357: ...6 42 Chapter 6 Sequence Program Used for Positioning Control...
Page 359: ...6 44 Chapter 6 Sequence Program Used for Positioning Control...
Page 360: ...6 45 Chapter 6 Sequence Program Used for Positioning Control...
Page 361: ...6 46 Chapter 6 Sequence Program Used for Positioning Control...
Page 363: ...6 48 Chapter 6 Sequence Program Used for Positioning Control...
Page 364: ...6 49 Chapter 6 Sequence Program Used for Positioning Control...
Page 413: ...MEMO...
Page 433: ...8 20 Chapter 8 OPR Control MEMO...
Page 458: ...9 25 Chapter 9 Major Positioning Control MEMO...
Page 593: ...10 30 Chapter 10 High Level Positioning Control MEMO...
Page 625: ...11 32 Chapter 11 Manual Control MEMO...
Page 659: ...12 34 Chapter 12 Expansion Control MEMO...
Page 767: ...13 108 Chapter 13 Control Sub Functions MEMO...
Page 813: ...14 46 Chapter 14 Common Functions MEMO...
Page 831: ...15 18 Chapter 15 Dedicated Instructions MEMO...
Page 846: ...16 15 Chapter 16 Troubleshooting MEMO...
Page 892: ...16 61 Chapter 16 Troubleshooting MEMO...
Page 971: ...Appendix 62 Appendices MEMO...
Page 974: ......
Page 975: ......