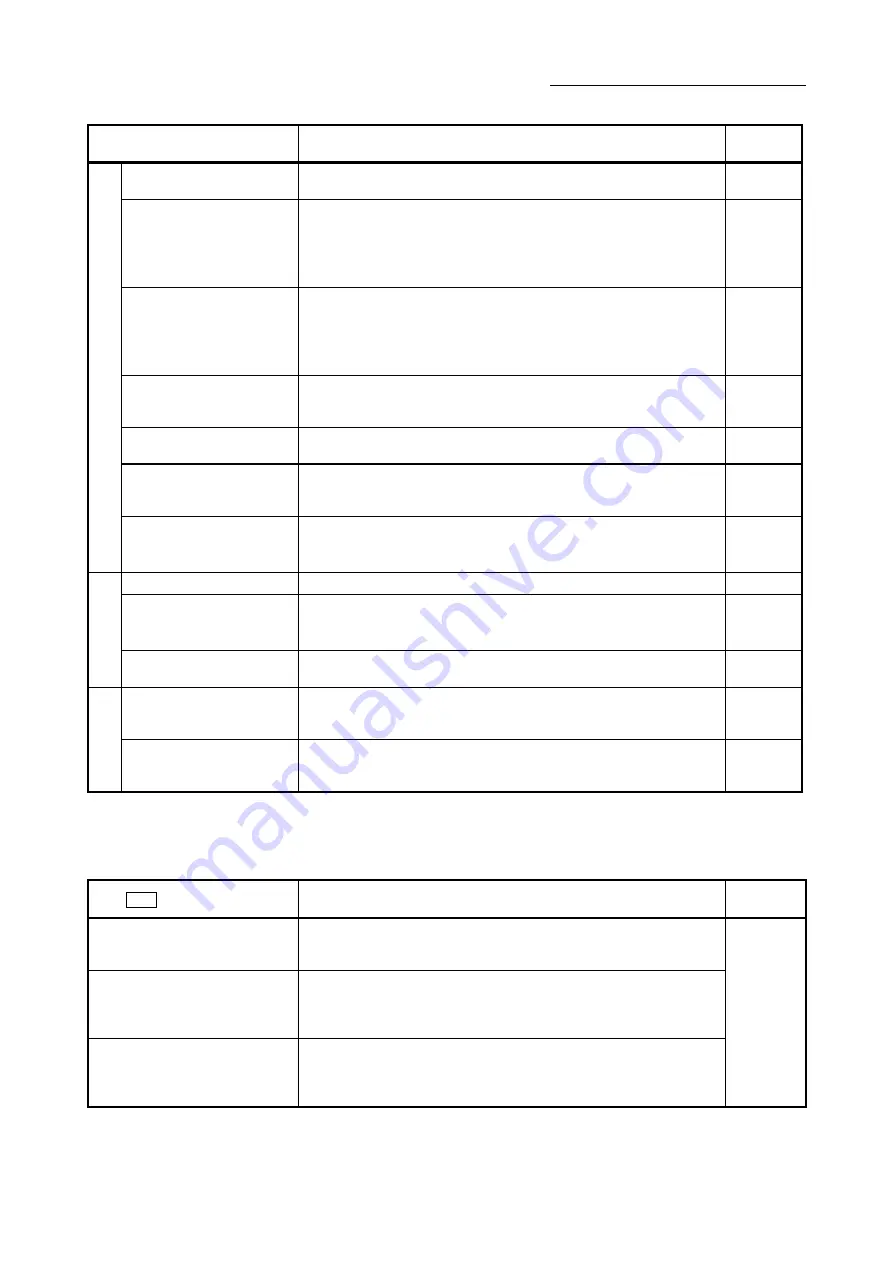
3 - 8
Chapter 3 Specifications and Functions
Main functions
Details
Reference
section
Block start (Normal start)
With one start, executes the positioning data in a random block with the
set order.
10.3.2
Condition start
Carries out condition judgment set in the "condition data" for the
designated positioning data, and then executes the "block start data".
When the condition is established, the "block start data" is executed.
When not established, that "block start data" is ignored, and the next
point's "block start data" is executed.
10.3.3
Wait start
Carries out condition judgment set in the "condition data" for the
designated positioning data, and then executes the "block start data".
When the condition is established, the "block start data" is executed.
When not established, stops the control until the condition is
established. (Waits.)
10.3.4
Simultaneous start
Simultaneously executes the positioning data having the No. for the axis
designated with the "condition data". (Outputs commands at the same
timing.)
10.3.5
Repeated start (FOR loop)
Repeats the program from the block start data set with the "FOR loop" to
the block start data set in "NEXT" for the designated number of times.
10.3.6
Repeated start (FOR
condition)
Repeats the program from the block start data set with the "FOR
condition" to the block start data set in "NEXT" until the conditions set in
the "condition data" are established.
10.3.7
H
igh-level positioning control
Multiple axes simultaneous
start control
Starts the operation of multiple axes simultaneously according to the
command output level.
(Positioning start No. 9004, same as the "simultaneous start" above)
10.5
JOG operation
Outputs a command to servo amplifier while the JOG start signal is ON.
11.2
Inching operation
Outputs commands corresponding to minute movement amount by
manual operation to servo amplifier.
(Performs fine adjustment with the JOG start signal.)
11.3
Manual control Manual pulse generator
operation
Outputs pulses commanded with the manual pulse generator to servo
amplifier.
11.4
Speed-torque control
Carries out the speed control or torque control that does not include the
position loop for the command to servo amplifier by switching control
mode.
12.1
Expansion
control
Synchronous control
Carries out the synchronous control that synchronizes with input axis by
setting the system such as gear, shaft, change gear and cam to the
"synchronous control parameter".
–
With the "major positioning control" ("high-level positioning control"), whether or not to
continuously execute the positioning data can be set with the "operation pattern".
Outlines of the "operation patterns" are given below.
Da.1
Operation pattern
Details
Reference
section
Independent positioning control
(positioning complete)
When "independent positioning control" is set for the operation pattern of
the started positioning data, only the designated positioning data will be
executed, and then the positioning will end.
Continuous positioning control
When "continuous positioning control" is set for the operation pattern of
the started positioning data, after the designated positioning data is
executed, the program will stop once, and then the next following
positioning data will be executed.
Continuous path control
When "continuous path control" is set for the operation pattern of the
started positioning data, the designated positioning data will be
executed, and then without decelerating, the next following positioning
data will be executed.
9.1.2
Summary of Contents for MELSEC-Q QD77MS
Page 1: ......
Page 27: ...A 26 MEMO...
Page 29: ...MEMO...
Page 101: ...3 34 Chapter 3 Specifications and Functions MEMO...
Page 232: ...5 111 Chapter 5 Data Used for Positioning Control MEMO...
Page 315: ...5 194 Chapter 5 Data Used for Positioning Control MEMO...
Page 337: ...6 22 Chapter 6 Sequence Program Used for Positioning Control...
Page 338: ...6 23 Chapter 6 Sequence Program Used for Positioning Control...
Page 339: ...6 24 Chapter 6 Sequence Program Used for Positioning Control...
Page 340: ...6 25 Chapter 6 Sequence Program Used for Positioning Control...
Page 341: ...6 26 Chapter 6 Sequence Program Used for Positioning Control...
Page 342: ...6 27 Chapter 6 Sequence Program Used for Positioning Control...
Page 343: ...6 28 Chapter 6 Sequence Program Used for Positioning Control...
Page 344: ...6 29 Chapter 6 Sequence Program Used for Positioning Control...
Page 345: ...6 30 Chapter 6 Sequence Program Used for Positioning Control...
Page 346: ...6 31 Chapter 6 Sequence Program Used for Positioning Control...
Page 347: ...6 32 Chapter 6 Sequence Program Used for Positioning Control...
Page 348: ...6 33 Chapter 6 Sequence Program Used for Positioning Control...
Page 349: ...6 34 Chapter 6 Sequence Program Used for Positioning Control...
Page 353: ...6 38 Chapter 6 Sequence Program Used for Positioning Control...
Page 354: ...6 39 Chapter 6 Sequence Program Used for Positioning Control...
Page 357: ...6 42 Chapter 6 Sequence Program Used for Positioning Control...
Page 359: ...6 44 Chapter 6 Sequence Program Used for Positioning Control...
Page 360: ...6 45 Chapter 6 Sequence Program Used for Positioning Control...
Page 361: ...6 46 Chapter 6 Sequence Program Used for Positioning Control...
Page 363: ...6 48 Chapter 6 Sequence Program Used for Positioning Control...
Page 364: ...6 49 Chapter 6 Sequence Program Used for Positioning Control...
Page 413: ...MEMO...
Page 433: ...8 20 Chapter 8 OPR Control MEMO...
Page 458: ...9 25 Chapter 9 Major Positioning Control MEMO...
Page 593: ...10 30 Chapter 10 High Level Positioning Control MEMO...
Page 625: ...11 32 Chapter 11 Manual Control MEMO...
Page 659: ...12 34 Chapter 12 Expansion Control MEMO...
Page 767: ...13 108 Chapter 13 Control Sub Functions MEMO...
Page 813: ...14 46 Chapter 14 Common Functions MEMO...
Page 831: ...15 18 Chapter 15 Dedicated Instructions MEMO...
Page 846: ...16 15 Chapter 16 Troubleshooting MEMO...
Page 892: ...16 61 Chapter 16 Troubleshooting MEMO...
Page 971: ...Appendix 62 Appendices MEMO...
Page 974: ......
Page 975: ......