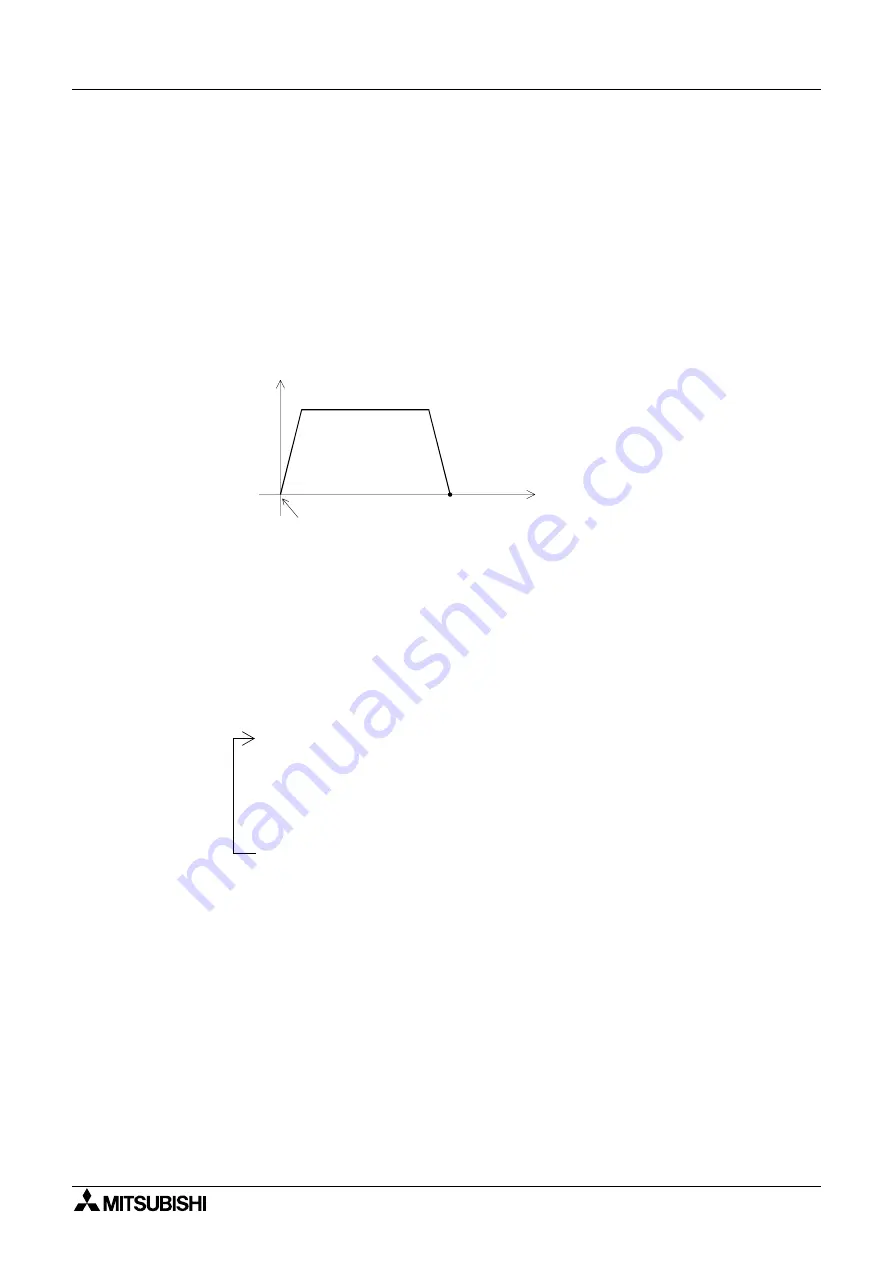
FX Series Positioning Controllers
Program Examples 9
9-10
9.3.4
Positioning operation in which movement quantity is variable (FX
2N
-10GM, FX
2N
-20GM)
1) Outline of positioning
A digital switch is connected to the positioning unit, and the machine moves by the move-
ment quantity set by the digital switch.
2) Operating procedure
c
The feed quantity (incremental value) is set from the digital switch. (For a connection
example, refer to the attached connection diagram.)
d
By the start command from the outside, the machine moves by the quantity set in
c
.
e
When movement is completed, the output Y5 turns on.
3) Operation chart
4) Program
In order to read the digital switch, the digit changeover time (initial value = 20 msec) should
be set by PARA. 33.
When a digital switch is connected to the FX
2N
-10GM / 20GM main body, this changeover
time is fixed to "7 ms". As a result, the operation time is reduced.
5) Parameter
Set the positioning parameter No. 16 (mechanical zero point address) to "0". For other
parameters, refer to Paragraph 9.2.4.
Speed
The output Y5 turns on.
The X axis start input turns on.
("One short 10 msec or more" turns on.)
Movement distance
Line No.
Instruction
Description
Ox0, N0
RST Y5;
Turns off the output Y5.
N1
cod91(INC);
Specifies the incremental address.
N2
cod92(SET) x0 ;
Sets the current value to "0".
N3
cod00(DRV) XD0;
Moves the machine by the quantity set to D0.
N4
SET Y5;
Turns on the output Y5.
N5
m02(END);
O100,N0
P0;
N1
FNC72(EXT) X0 Y0 D0 K5; (Head No. for digital switch connection input: X0
(X0 to X3 will be used.))
(Head No. for digital switch connection output: Y0)
(Data storage destination: D0)
(Number of digits: 5 (Y0 to Y4 will be used.))
N2
FNC04(JMP) P0;
N3
ml02(SEND);
Summary of Contents for FX2N-10GM
Page 1: ...HARDWARE PROGRAMMING MANUAL FX2N 10GM FX2N 20GM ...
Page 4: ...FX Series Positioning Controllers ii ...
Page 6: ...FX Series Positioning Controllers iv ...
Page 46: ...FX Series Positioning Controllers Introduction 1 1 34 MEMO ...
Page 76: ...FX Series Positioning Controllers Wiring 3 3 24 MEMO ...
Page 222: ...FX Series Positioning Controllers Operation Maintenance and Inspection 8 8 18 MEMO ...
Page 256: ...FX Series Positioning Controllers Program Examples 9 9 34 MEMO ...