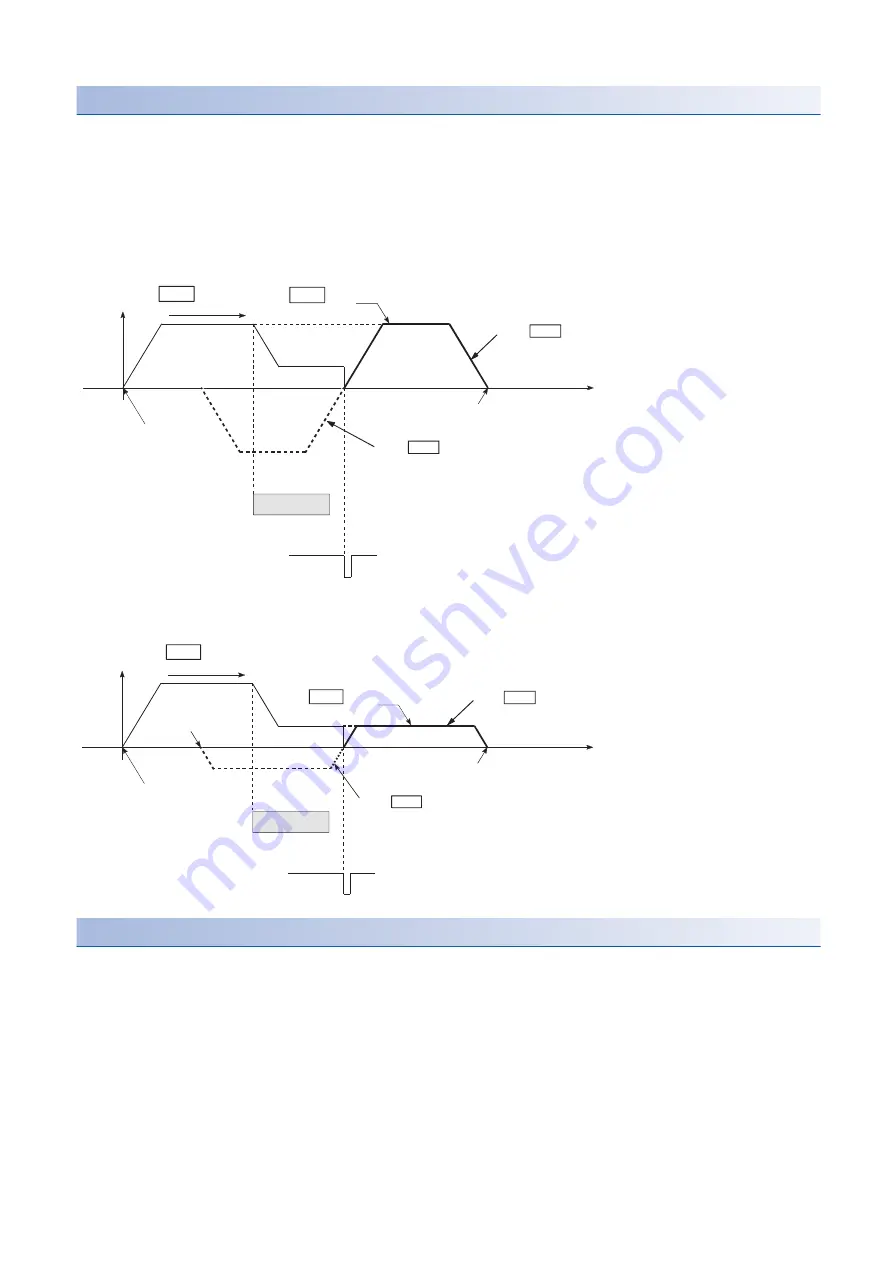
216
7 CONTROL SUB FUNCTIONS
7.2 Sub Functions Specific to Machine OPR
Movement speed during the OP shift
When the OP shift function is used, set the movement speed during the OP shift in [Pr.56] Speed specification during OP shift.
Select the movement speed during the OP shift from [Pr.46] OPR speed or [Pr.47] Creep speed. Set the speed in [Pr.56]
Speed specification during OP shift.
The following figures show the movement speed during the OP shift when the machine OPR is performed using the near-
point dog method.
■
OP shift operation at the speed set in [Pr.46] OPR speed (when [Pr.56] Speed specification
during OP shift is 0)
■
OP shift operation at the speed set in [Pr.47] Creep speed (when [Pr.56] Speed specification
during OP shift is 1)
Control precautions
• OPR complete flag ([Md.31] Status: b4), [Md.20] Current feed value, [Md.21] Machine feed value, and [Md.26] Axis
operation status are set after the OP shift operation is completed. OPR request flag ([Md.31] Status: b3) is reset after the
OP shift operation is completed.
• The value set in [Pr.53] OP shift amount is not added in [Md.34] Movement amount after near-point dog ON. The movement
amount immediately before the OP shift operation, considering the amount when the near-point dog is on as 0, is stored.
For the stopper method (1, 2, 3), the movement amount is not changed from 0.
• When using the OP shift function with the stopper method (1, 2, 3) selected for the OPR method, configure the OP shift
operation in the opposite direction of the OPR direction. Shifting in the OPR direction is not possible due to a mechanical
stopper in the OPR direction.
Pr. 44
Pr. 46
OP
When Pr.53 OP shift
amount is positive
When Pr.53 OP shift amount is negative
OPR direction
Machine OPR start
OPR speed
Near-point dog
Zero signal
Pr. 44
Pr. 47
When Pr.53 OP shift amount is negative
When Pr.53 OP shift
amount is positive
OPR direction
OP
Machine OPR start
Near-point dog
Zero signal
OP
Creep speed
Summary of Contents for MELSEC iQ-R RD75P4
Page 1: ...MELSEC iQ R Positioning Module User s Manual Application RD75P2 RD75P4 RD75D2 RD75D4 ...
Page 2: ......
Page 13: ...11 MEMO ...
Page 19: ...17 CONTENTS INDEX 588 REVISIONS 592 WARRANTY 593 TRADEMARKS 594 ...
Page 498: ...496 13 PROGRAMMING 13 2 List of Labels Used ...
Page 503: ...13 PROGRAMMING 13 4 Program Example 501 13 ...
Page 514: ...512 13 PROGRAMMING 13 4 Program Example Restart program Parameter data initialization program ...
Page 515: ...13 PROGRAMMING 13 4 Program Example 513 13 Flash ROM write program Error reset program ...
Page 516: ...514 13 PROGRAMMING 13 4 Program Example Stop program ...
Page 565: ...APPENDICES Appendix 4 Operation Examples of When the Remote Head Module Is Mounted 563 A ...
Page 597: ......