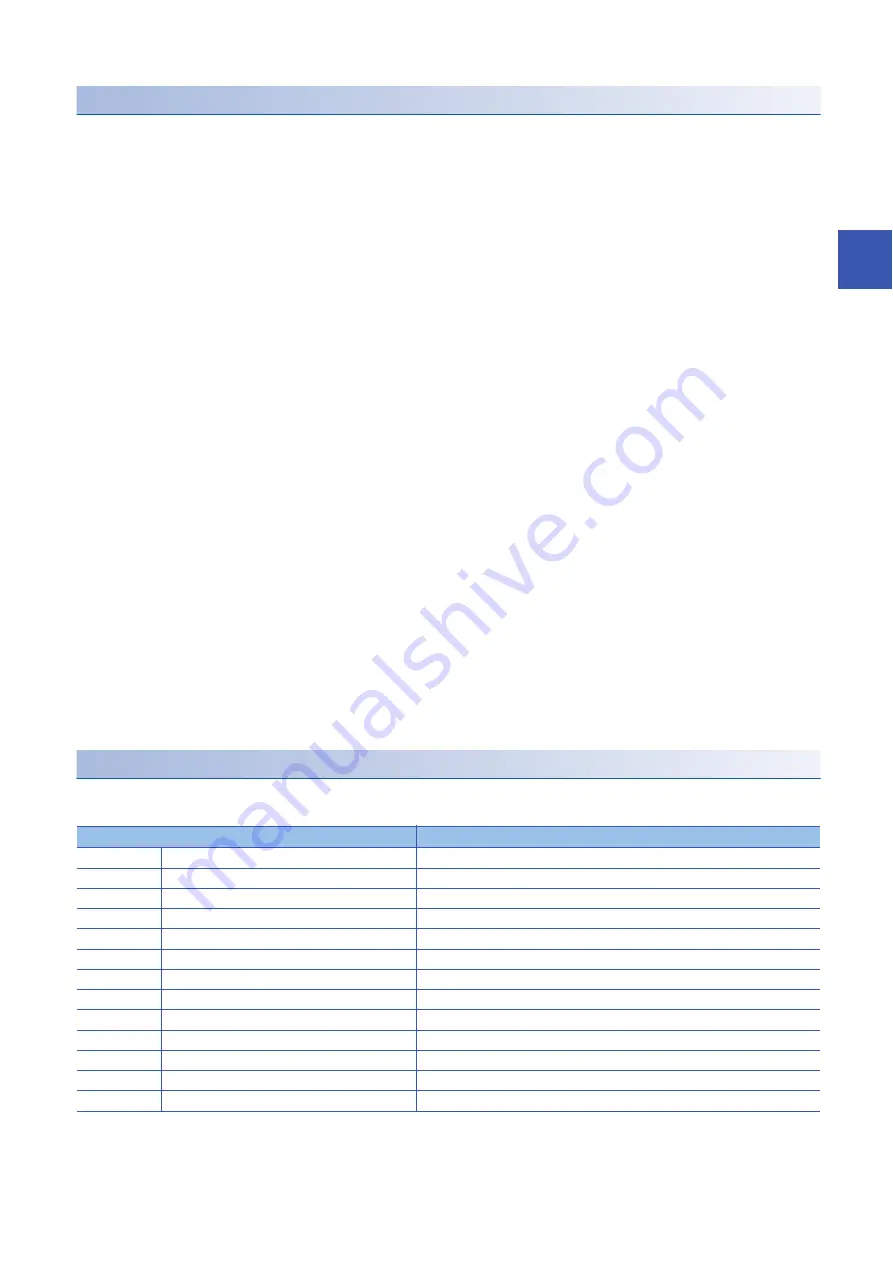
3 MAJOR POSITIONING CONTROL
3.2 Positioning Data Setting
131
3
Restrictions
• If Continuous path control is set in [Da.1] Operation pattern, Continuous path control not possible (Error code: 1A1FH)
occurs and the control will not start.
• Speed-position switching control cannot be set in [Da.2] Control method in the positioning data when Continuous path
control is set in [Da.1] Operation pattern of the immediately previous positioning data. (For example, if the operation pattern
of the positioning data No.1 is Continuous path control, the speed-position switching control cannot be set to the positioning
data No.2.) If this setting is configured, Continuous path control not possible (Error code: 1A20H) occurs and the
deceleration stop is performed.
• If Current speed (-1) is set to [Da.8] Command speed, No command speed (Error code: 1A14H) occurs.
• The software stroke limit range check during the speed control is executed only when the following 1) and 2) are satisfied.
• Is the value set in [Da.6] Positioning address/movement amount is negative, Outside address range (Error code: 1A30H)
occurs.
• If the movement amount of the position control set in [Da.6] Positioning address/movement amount is smaller than the
deceleration distance from [Da.8] Command speed, the deceleration processing is performed when Speed-position
switching signal is input.
• Turn on Speed-position switching signal in the speed stabilization region (in the constant speed state). If the signal is turned
on during the acceleration, the variation of the droop pulse amount becomes large and Speed-position switching signal ON
(Warning code: 0993H) occurs. When a servomotor is used, the actual movement amount after the control is switched to
the position control is calculated by adding Set movement amount and Droop pulse amount. If the signal is turned on during
the acceleration or deceleration, the variation of the droop pulse amount becomes large and the operation stop position
varies. Even if the values in [Md.29] Speed-position switching control positioning amount are the same between the two
controls, the stop positions change because the droop pulse amount changes when the values in [Da.8] Command speed
of both controls differ.
• When a negative value is set in [Cd.23] Speed-position switching control movement amount change register, Insufficient
movement amount (Warning code: 0998H) occurs and the movement amount is the value set in [Da.6] Positioning address/
movement amount.
Positioning data to be set
To use the speed-position switching control (INC mode), set the following positioning data.
: Always set,
: Set as required,
: Setting not required
For details on the settings, refer to the following.
1)
[Pr.21] Current feed value during speed control is 1: Current feed value is updated.
In any case other than the above, if the movement amount exceeds the software stroke limit range during the speed control, Software stroke limit (+) (Error
code: 1A18H) or Software stroke limit (-) (Error code: 1A1AH) occurs and the control decelerates and stops when the control is switched to the position
control.
2)
When a value other than 2: degree is set in [Pr.1] Unit setting
When the unit is degree, the software stroke limit range is not checked.
Setting item
Setting requirement
[Da.1]
Operation pattern
[Da.2]
Control method
(Set Forward run speed-position or Reverse run speed-position.)
[Da.3]
Acceleration time No.
[Da.4]
Deceleration time No.
[Da.5]
Axis to be interpolated
[Da.6]
Positioning address/movement amount
[Da.7]
Arc address
[Da.8]
Command speed
[Da.9]
Dwell time
[Da.10]
M code
[Da.27]
M code ON signal output timing
[Da.28]
ABS direction in degrees
[Da.29]
Interpolation speed specification method
Summary of Contents for MELSEC iQ-R RD75P4
Page 1: ...MELSEC iQ R Positioning Module User s Manual Application RD75P2 RD75P4 RD75D2 RD75D4 ...
Page 2: ......
Page 13: ...11 MEMO ...
Page 19: ...17 CONTENTS INDEX 588 REVISIONS 592 WARRANTY 593 TRADEMARKS 594 ...
Page 498: ...496 13 PROGRAMMING 13 2 List of Labels Used ...
Page 503: ...13 PROGRAMMING 13 4 Program Example 501 13 ...
Page 514: ...512 13 PROGRAMMING 13 4 Program Example Restart program Parameter data initialization program ...
Page 515: ...13 PROGRAMMING 13 4 Program Example 513 13 Flash ROM write program Error reset program ...
Page 516: ...514 13 PROGRAMMING 13 4 Program Example Stop program ...
Page 565: ...APPENDICES Appendix 4 Operation Examples of When the Remote Head Module Is Mounted 563 A ...
Page 597: ......