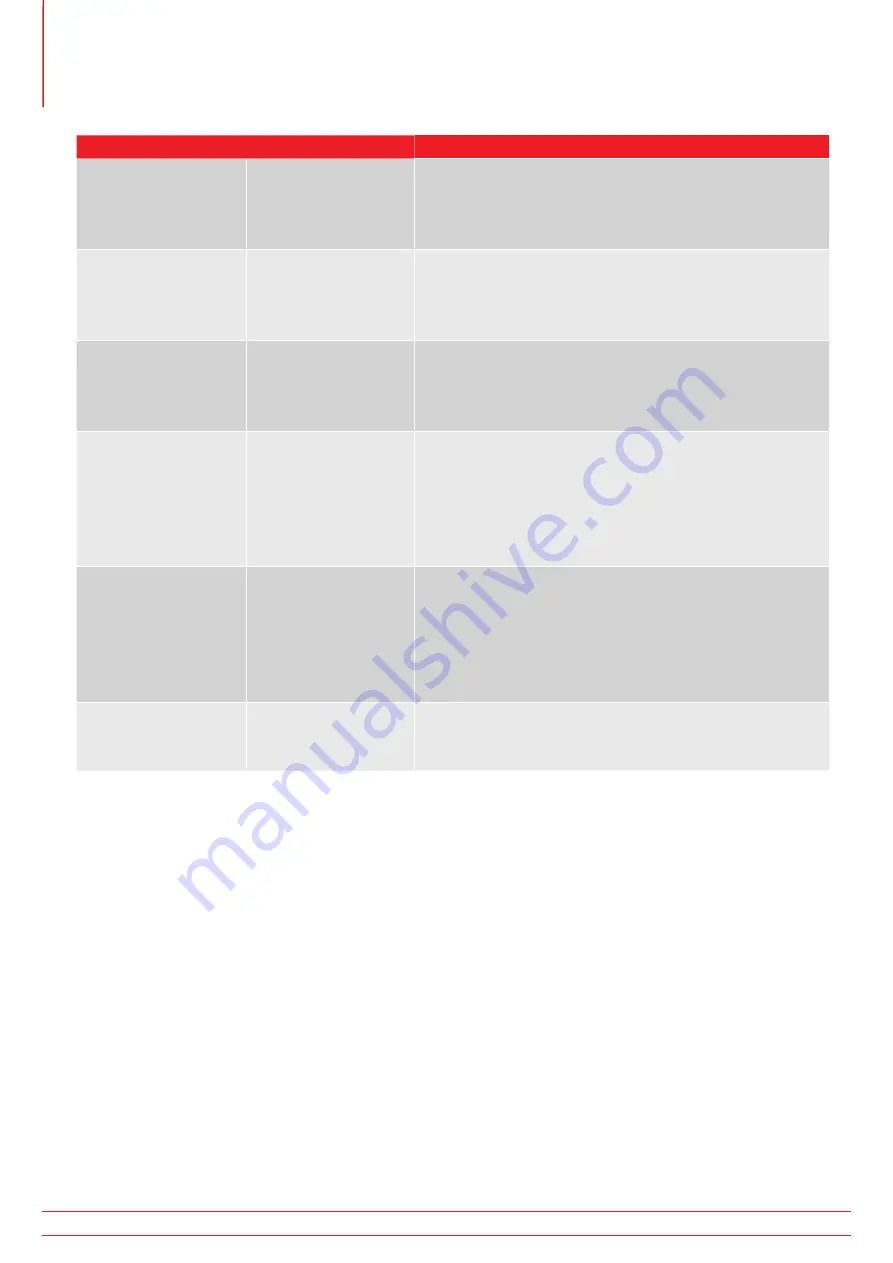
12.3.3 Initialisation critical errors.
Error no.
Cause:
Action:
1:
Licence is missing.
The BALTO software
installation is missing
a critical component.
Please contact Megger technical assistance.
2:
Calibration values
missing.
3:
Registry key ‘NLC’ not
found.
4:
Registry key ‘NLCin’
not found.
The calibration
program is unable
to access the
system calibration
parameters.
Please contact Megger technical assistance.
5:
PLC problem detected.
The calibration
program is unable to
communicate with
the TwinCAT I/O
service.
Please try restarting the system.
If the problem persists, please contact Megger technical
assistance.
6:
No DC Current
Generators connected.
No connected DC
Current Generators
are detected.
Ensure that all DC Current Generators are properly
connected and restart the calibration program.
12.4 Failed calibration messages.
If a step of the calibration process fails, one of the following messages will be displayed:
The offset output calibration has reached the end without being able to determine a plausible value.
Unable to determine CF_OUT.
Unable to determine CF_IN.
Approaching invalid values, procedure stopped for safety reasons.
Cause:
The calibration step failed to determine the calibration value.
Action:
Please check the following:
The High-speed DC Circuit Breaker is closed.
The High-speed DC Circuit Breaker’s configured trip level is sufficiently high.
The calibration sensor is connected properly.
If the problem persists, please contact Megger technical assistance.
www.megger.com
138
Calibration