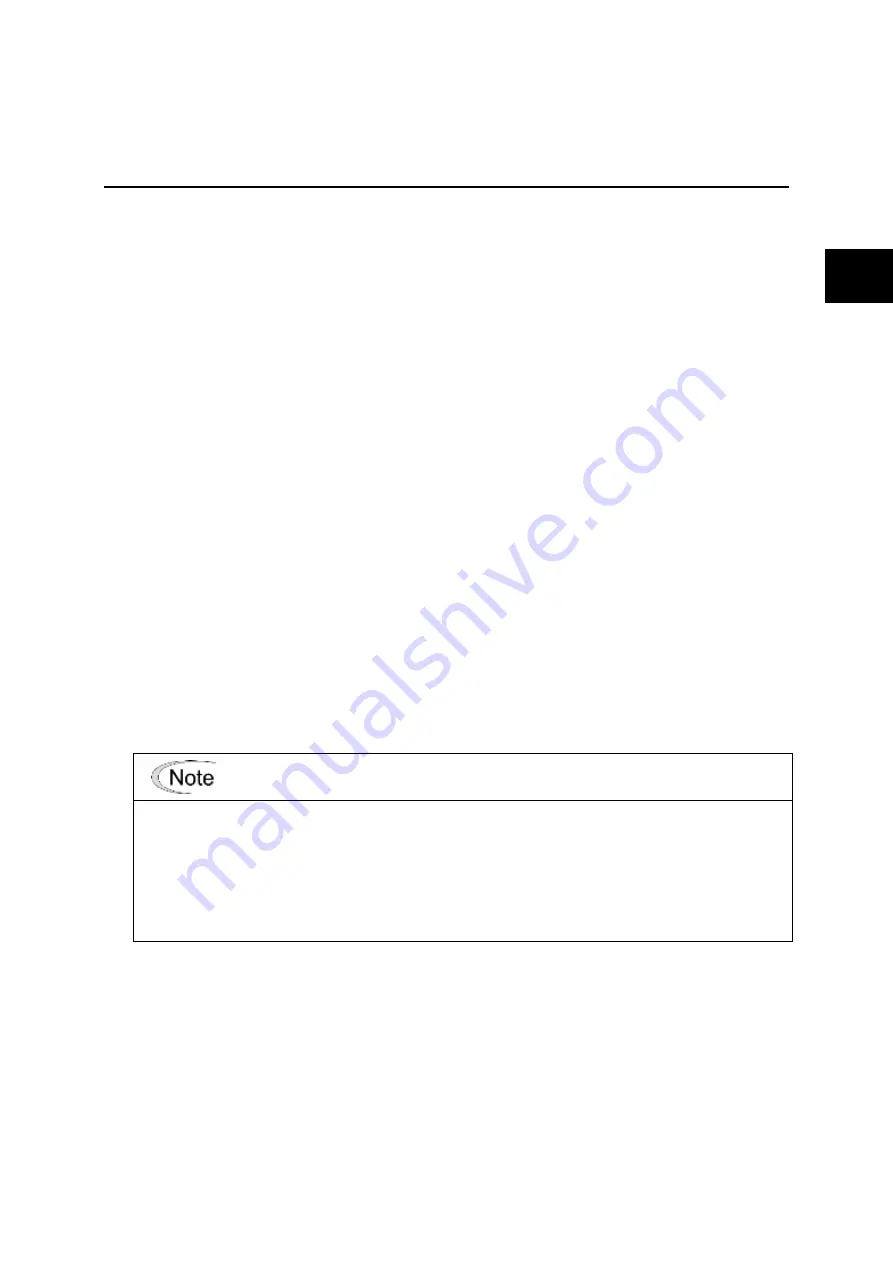
CHAPTER 2 WIRING
Description of I/O Signals
2-39
2
Over-travel in positive direction [+OT]: Sequence input signal (Reference value 7)
Over-travel in negative direction [-OT]: Sequence input signal (Reference value 8)
A signal from a limit switch or similar can forcibly stop the machine travel.
Function
The signal is an input from a limit switch for avoiding over-travel (OT) beyond the limit of machine
travel.
Each signal is always enabled except under torque control.
If the over-travel signal is turned off during operation, the servomotor decelerates and stops at the
limit value set at PA2_60 (third torque limit) or deceleration time set at PA2_76 (third deceleration
time) based on the PA2_63 (action sequence at mainpower shutoff, OT detection) setting.
Pulse input in the direction opposite to the detection direction, manual feed (forward/reverse
command) and positioning (auto feed) can be executed (normally close contact).
If an OT signal is detected during positioning operation, the servomotor is forcibly stopped and
therefore difference may be caused between the command position and feedback position.
Take care of the reference value and sensor position so that the OT signal will not be detected
during regular operation.
Parameter setting
To assign the +OT signal to a sequence input terminal, specify the corresponding value ("7") to
the input terminal function setting parameter. For the -OT signal, specify ("8").
This signal is handled to be always turned on if it is not assigned to the sequence input terminal.
Relevant description
(1) Direction of detection
The +OT signal is detected during a travel of the servomotor in the positive direction. The positive
direction indicates the direction of forward rotation if PA1_4 (rotation direction selection) is set at
"0" (positive direction).
If the servomotor rotation direction and OT signal direction are the opposite of one another, the
servo motor will not stop even if the OT signal is detected. There is a possibility of equipment
failure due to such reasons as a collision at the equipment end, and therefore it is necessary to
ensure that the rotation direction and OT signal direction match.
Failure to observe this may result in a fault.
Summary of Contents for ALPHA7
Page 1: ......
Page 3: ...ii...
Page 22: ...0 1 CHAPTER 0 INTRODUCTION 0...
Page 36: ...1 1 CHAPTER 1 INSTALLATION 1...
Page 47: ...CHAPTER 1 INSTALLATION 1 12 Servo Amplifier 1...
Page 48: ...2 1 CHAPTER 2 WIRING 2...
Page 163: ...CHAPTER 2 WIRING 2 116 Safety Function 2...
Page 164: ...3 1 CHAPTER 3 OPERATION 3...
Page 192: ...4 1 CHAPTER 4 PARAMETER 4...
Page 317: ...CHAPTER 4 PARAMETER 4 126 Extension Function 2 Setting Parameters 4...
Page 318: ...5 1 CHAPTER 5 SERVO ADJUSTMENT 5...
Page 353: ...CHAPTER 5 SERVO ADJUSTMENT 5 36 Special Adjustment Vibration Suppression 5...
Page 354: ...6 1 CHAPTER 6 KEYPAD 6...
Page 408: ...7 1 CHAPTER 7 MAINTENANCE AND INSPECTION 7...
Page 434: ...8 1 CHAPTER 8 SPECIFICATIONS 8...
Page 460: ...9 1 CHAPTER 9 CHARACTERISTICS 9...
Page 472: ...10 1 CHAPTER 10 PERIPHERAL EQUIPMENT 10...
Page 516: ...11 1 CHAPTER 11 ABSOLUTE POSITION SYSTEM 11...
Page 523: ...CHAPTER 11 ABSOLUTE POSITION SYSTEM 11 8 Calculation of Battery Life 11...
Page 524: ...12 1 CHAPTER 12 POSITIONING DATA 12...
Page 540: ...13 1 CHAPTER 13 MODBUS RTU COMMUNICATION 13...
Page 579: ...CHAPTER 13 MODBUS RTU COMMUNICATION 13 40 Communications Procedures 13...
Page 580: ...14 1 CHAPTER 14 PC LOADER 14...
Page 614: ...STANDARDS COMPLIANCE CHAPTER 15 15...
Page 628: ...CHAPTER 16 APPENDIXES 16...
Page 661: ...CHAPTER 16 APPENDIXES 34 Product Warranty 16 16 7 Product Warranty...
Page 662: ......