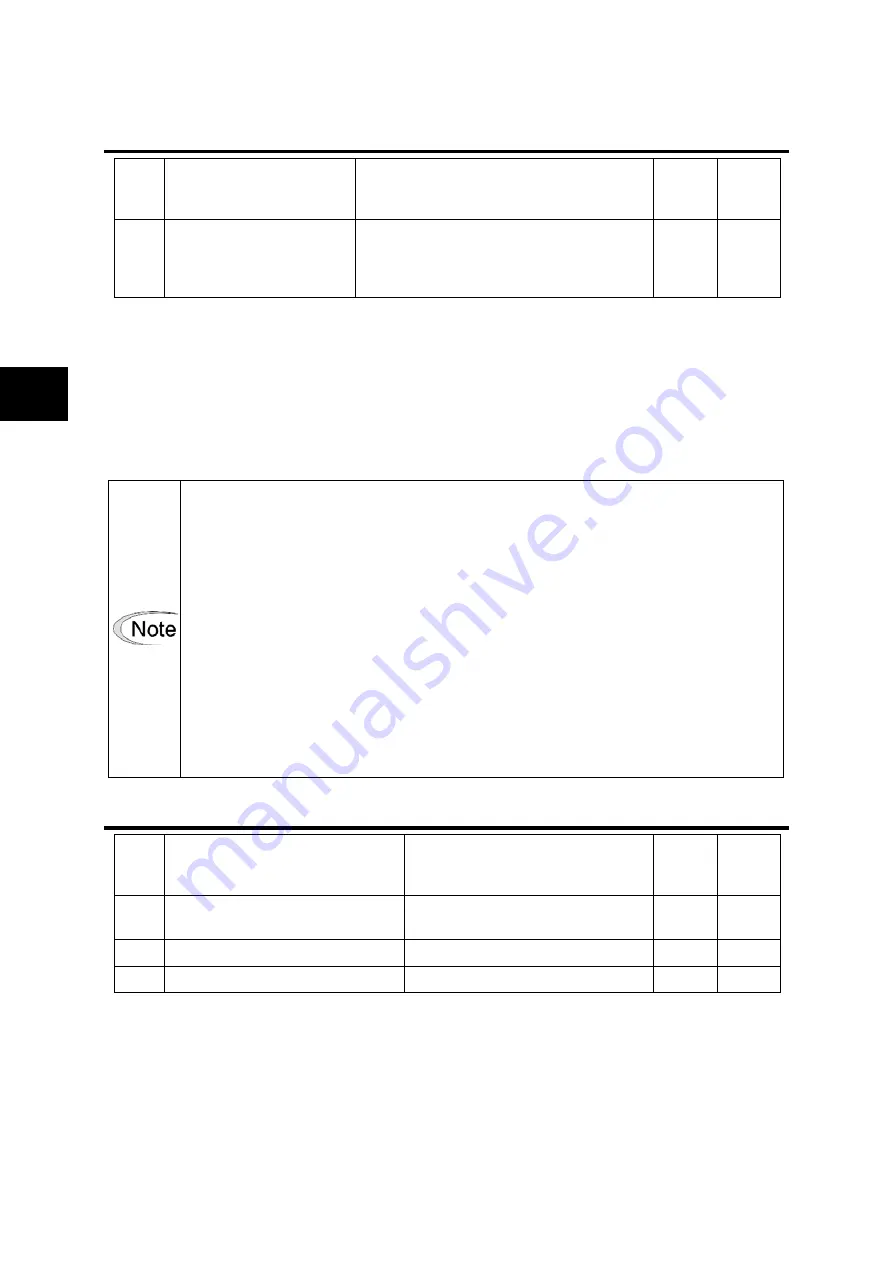
CHAPTER 4 PARAMETER
4-124
Extension Function 2 Setting Parameters
4
PA4_60
Cogging torque compensation
No.
Name
Setting range
Default
value
Change
60
Cogging torque
compensation
0: Disable
1: Enable
2: Learning
3: Clear learning result
0
Always
Speed fluctuations resulting from servomotor cogging torque can be suppressed.
Use this parameter if wishing to suppress speed fluctuations during operation.
This function can be used by setting the parameter to 2 (learning), rotating the servomotor 10 times or
more, and after the servo amplifier has learned the cogging torque (the parameter is automatically set
to 1: Enable when learning is complete.)
To reset the learned result, set to 3 (clear learning result) (the parameter is automatically set to 0:
Disable when the result is cleared.)
Run the servomotor under the following operating conditions when performing
learning.
If the following conditions are not satisfied, it may not be possible to perform learning
correctly.
(1)
Run the servomotor on its own before installing it on the machine.
(2)
When performing learning, run the servomotor at a constant rotation speed of
approximately 100 [r/min].
If learning is not completed, it will not be possible to set this parameter to 1: Enable. A
data error will occur when an attempt is made to set the parameter.
The cogging torque differs for each motor. Perform teaching again when a motor is
replaced.
There may be no effect, even when using this function, for such reasons as the
cogging torque being too low. If no effect is observed, set this function to “0: Disable”.
PA4_61 to 63
Tuningless function settings
No.
Name
Setting range
Default
value
Change
61
Tuningless function
Enable/disable
0: Disable 1: Enable
0
Power
supply
62 Tuningless level
0 to 7
4
Always
63 Tuningless load level
0 to 3
3
Always
Set these parameters when using the tuningless function.
Refer to "5.2 Tuningless Function" for details on settings and adjustment, etc.
Summary of Contents for ALPHA7
Page 1: ......
Page 3: ...ii...
Page 22: ...0 1 CHAPTER 0 INTRODUCTION 0...
Page 36: ...1 1 CHAPTER 1 INSTALLATION 1...
Page 47: ...CHAPTER 1 INSTALLATION 1 12 Servo Amplifier 1...
Page 48: ...2 1 CHAPTER 2 WIRING 2...
Page 163: ...CHAPTER 2 WIRING 2 116 Safety Function 2...
Page 164: ...3 1 CHAPTER 3 OPERATION 3...
Page 192: ...4 1 CHAPTER 4 PARAMETER 4...
Page 317: ...CHAPTER 4 PARAMETER 4 126 Extension Function 2 Setting Parameters 4...
Page 318: ...5 1 CHAPTER 5 SERVO ADJUSTMENT 5...
Page 353: ...CHAPTER 5 SERVO ADJUSTMENT 5 36 Special Adjustment Vibration Suppression 5...
Page 354: ...6 1 CHAPTER 6 KEYPAD 6...
Page 408: ...7 1 CHAPTER 7 MAINTENANCE AND INSPECTION 7...
Page 434: ...8 1 CHAPTER 8 SPECIFICATIONS 8...
Page 460: ...9 1 CHAPTER 9 CHARACTERISTICS 9...
Page 472: ...10 1 CHAPTER 10 PERIPHERAL EQUIPMENT 10...
Page 516: ...11 1 CHAPTER 11 ABSOLUTE POSITION SYSTEM 11...
Page 523: ...CHAPTER 11 ABSOLUTE POSITION SYSTEM 11 8 Calculation of Battery Life 11...
Page 524: ...12 1 CHAPTER 12 POSITIONING DATA 12...
Page 540: ...13 1 CHAPTER 13 MODBUS RTU COMMUNICATION 13...
Page 579: ...CHAPTER 13 MODBUS RTU COMMUNICATION 13 40 Communications Procedures 13...
Page 580: ...14 1 CHAPTER 14 PC LOADER 14...
Page 614: ...STANDARDS COMPLIANCE CHAPTER 15 15...
Page 628: ...CHAPTER 16 APPENDIXES 16...
Page 661: ...CHAPTER 16 APPENDIXES 34 Product Warranty 16 16 7 Product Warranty...
Page 662: ......