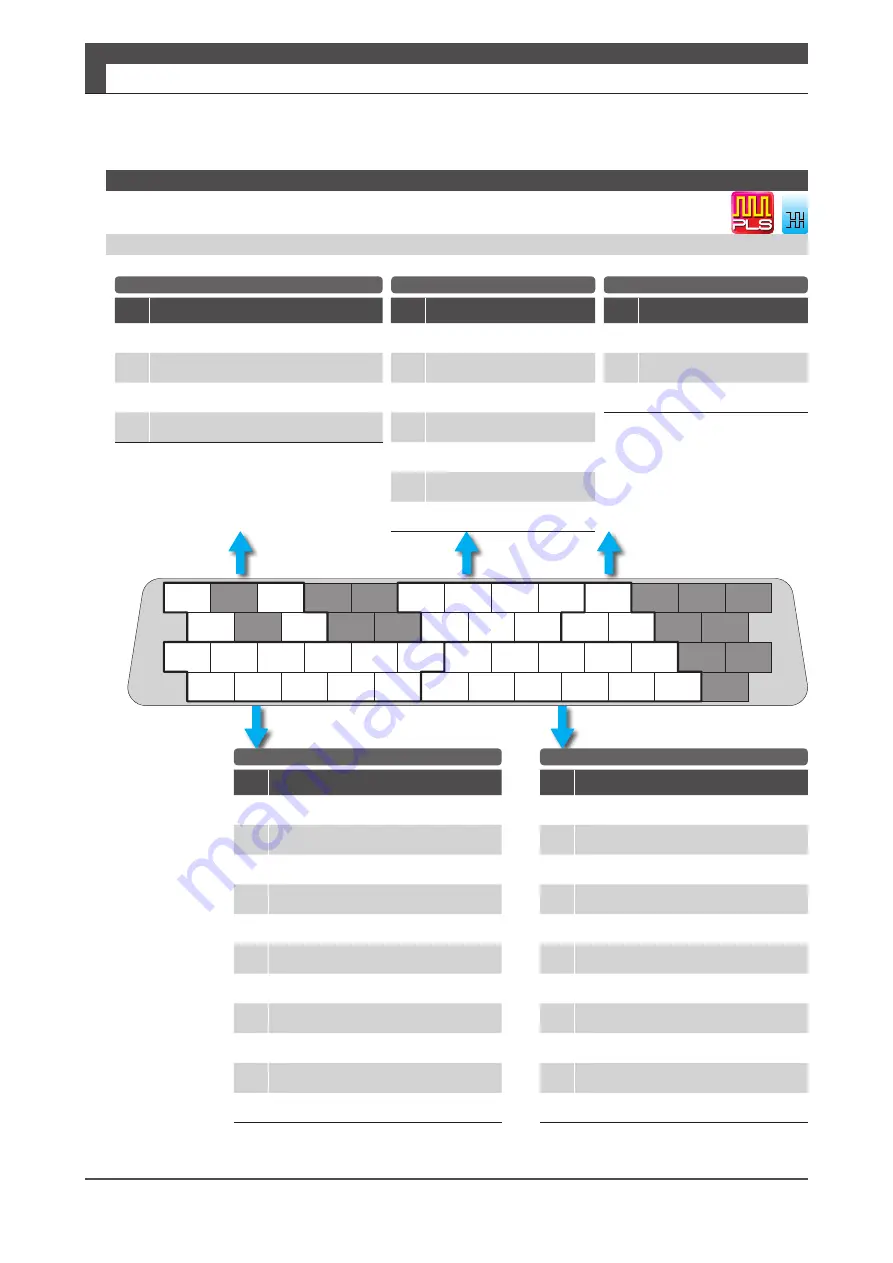
6
22
ALM−
23
―
49
―
OUT̲A
36
CMD̲PLS
26
―
28
CMD̲DIR
30
―
32
―
34
OUT̲B
38
OUT̲Z
40
SG
42
/485
44
―
46
―
48
―
50
/CMD̲PLS
27
29
―
31
/CMD̲DIR
33
―
35
―
37
/OUT̲A
39
/OUT̲B
41
/OUT̲Z
43
485
45
SG
47
―
1
24V
3
COM+
5
RESET
7
PCLR
9
CCWL
11
TLSEL1
13
MBRK
15
POSIN
17
MEND
/T-LIMIT
19
SRDY+
21
ALM+
25
―
2
G24V
4
SVON
6
HOLD
8
HOME
10
CWL
12
COM−
14
SERVO
16
HEND
18
OCZ
20
SRDY−
24
―
4. Connection
SD3 Series Instruction Manual
2. Position Control Mode
Pin
No.
Signal
Description
26
CMD_PLS
Pulse, QEP A-phase or CCW
27
/CMD_PLS
/Pulse, QEP /A-phase or /CCW
30
CMD_DIR
Direction, QEP B-phase or CW
31
/CMD_DIR
/Direction, QEP /B-phase or /CW
Pin
No.
Signal
Description
12
COM-
I/O power GND
13
MBRK
Brake release
14
SERVO
Servo status
15
POSIN
Positioning complete
16
HEND
(*)
Homing complete
17
MEND/T-LIMIT
(*)
Motion complete/Torque limiting
18
OCZ
Encoder Z-phase (open collector)
19
SRDY+
Servo ready +
20
SRDY-
Servo ready-Servo ready -
21
ALM +
Alarm
22
ALM-
Alarm status -
Pin
No.
Signal
Description
1
24V
Control power 24 V
2
G24V
Control power GND
3
COM+
I/O Power 24 V
4
SVON
Servo ON
5
RESET
Alarm reset
6
HOLD
Command input prohibited
7
PCLR
Deviation counter clear
8
HOME
(*)
Homing start
9
CCWL
CCW drive restriction
10
CWL
CW drive restriction
11
TLSEL1
Torque Limit
Pin
No.
Signal
Description
36
OUT_A
A-phase
37
/OUT_A
/A-phase
38
OUT_B
B-phase
39
/OUT_B
/B-phase
40
OUT_Z
Z-phase
41
/OUT_Z
/Z-phase
42
SG
Signal ground
Pin
No.
Signal
Description
43
485
Data
44
/485
/Data
45
SG
Signal ground
Differential, I/O Setting Option 1
General-Purpose Input
General-Purpose Output
Command Input
Encoder Output
RS-485 Communication
QEP: Quadrature encoder pulse
I/O Connector pinout
on the soldering surface
Pinout Diagram
*) For these pins function, change I/O setting with "Servo Studio".
dif.
Summary of Contents for SD3 Series
Page 1: ...R FATEK AUTOMATION CORP Instruction Manual AC SERVO MOTOR and SERVO AMPLIFIER SD3 Series...
Page 6: ...6 MEMO SD3 Series Instruction Manual...
Page 52: ...32 MEMO 2 Specifications SD3 Series Instruction Manual...
Page 92: ...40 MEMO 3 Preparation SD3 Series Instruction Manual...
Page 292: ...48 MEMO SD3 Series Instruction Manual 6 Operation...
Page 338: ...46 MEMO SD3 Series Instruction Manual 7 Tuning...
Page 362: ...24 MEMO 8 Troubleshooting SD3 Series Instruction Manual...
Page 395: ...MEMO SD3 Series Instruction Manual...
Page 396: ...R...