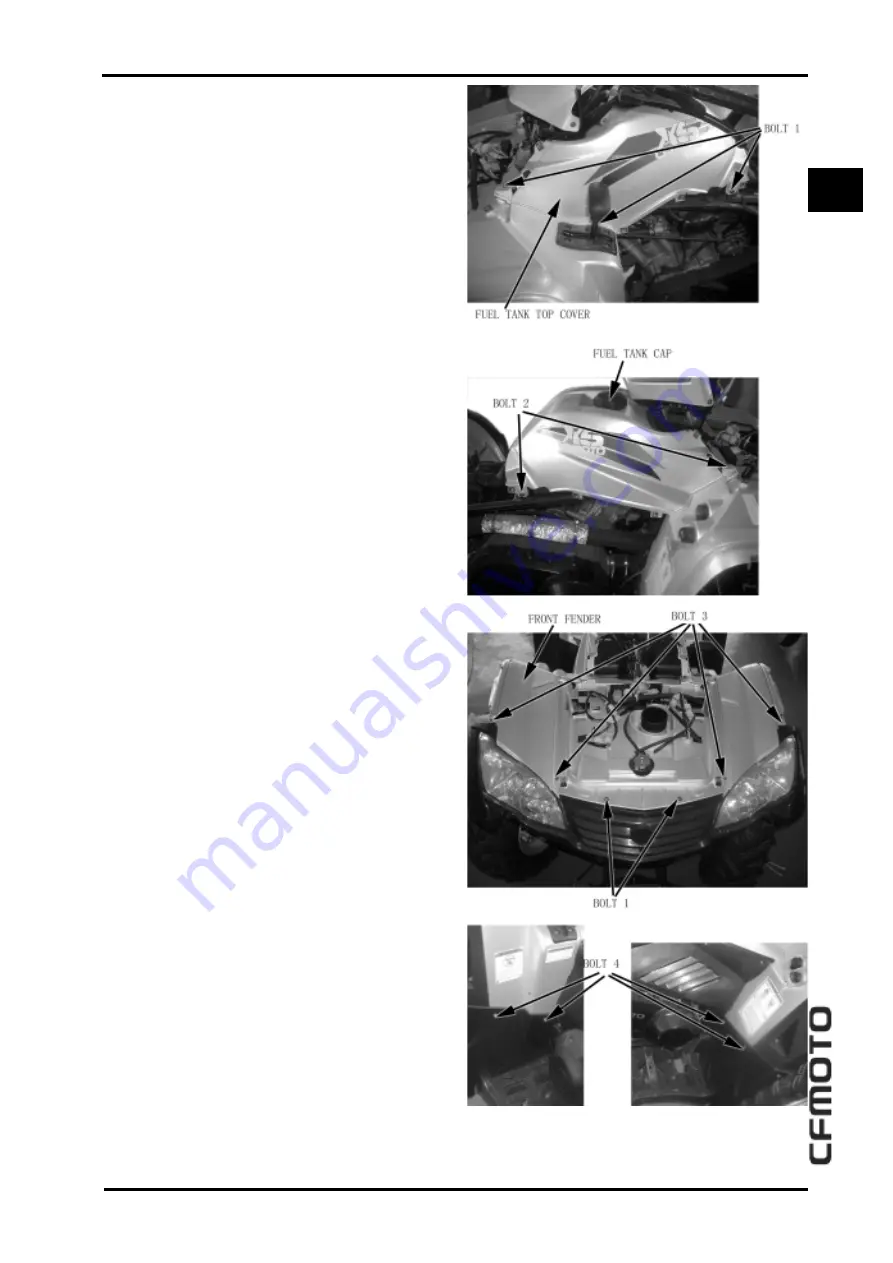
2-9
2 Vehicle Body and Muffler
2
2
2
2
2
Top Cover, Fuel Tank
Remove
--Seat(2-3)
--Front Rack(2-2)
--Front Top Cover(2-4)
--Left Side Panel(2-7)
--Right Side Panel(2-8)
--Bolt 1, 2
--Bolt 3, 4
--Fuel Tank Cap
Remove Fuel Tank Top Cover
Installation
Reverse the remove procedure and
direction for installation .
Front Fender
Remove
--Front Rack(2-2)
--Front Top Cover(2-4)
--Left, Right Side Panel(2-7)(2-8)
--Fuel Tank Top Cover(2-8)
--Left,Right Side Support(2-5)
Loosen Cable Connector of Front Fender
Remove Electronics Parts of Front Fender
Remove 3 Front Fender bolts fixed in Frame
Remove 4 bolts fixed with left and right
footrest
Remove Front Fender
Installation
Reverse the remove procedure for installation
Summary of Contents for CF500-5
Page 1: ...WWW CFMOTO COM CF500 5 SERVICE CF500 5A MANUAL...
Page 2: ...All rights reserved Zhejiang CFMOTO Power Co Ltd April 2009 WWW CFMOTO COM...
Page 24: ...1 20 CFMOTO...
Page 25: ...1 21 1 Maintenance Information 1 1 1 1 1...
Page 26: ...1 22 CFMOTO...
Page 47: ...2 19 2 Vehicle Body and Muffler 2 2 2 2 2 Visible Parts...
Page 80: ...4 7 4 Cooling and Lubrication system 4 4 4 4 4 Cooling System Chart...
Page 92: ...4 19 4 Cooling and Lubrication system 4 4 4 4 4...
Page 97: ...5 4 CFMOTO Removal Bolt 4 units of Engine...
Page 129: ...6 29 6 Engine Removal Inspection Installation 6 6 6 6 6 Primary and Secondary Sheave...
Page 222: ...11 Battery Charging System 11 11 11 11 11 11 9 Layout of Electric parts...
Page 230: ...12 8 CFMOTO Starting Motor...
Page 233: ...12 Ignition System 1 2 1 2 1 2 1 2 1 2 12 11 Ignition System Diagram...
Page 247: ...14 2 CFMOTO...
Page 248: ...14 Troubleshooting 14 14 14 14 14 14 3...
Page 249: ...14 4 CFMOTO...