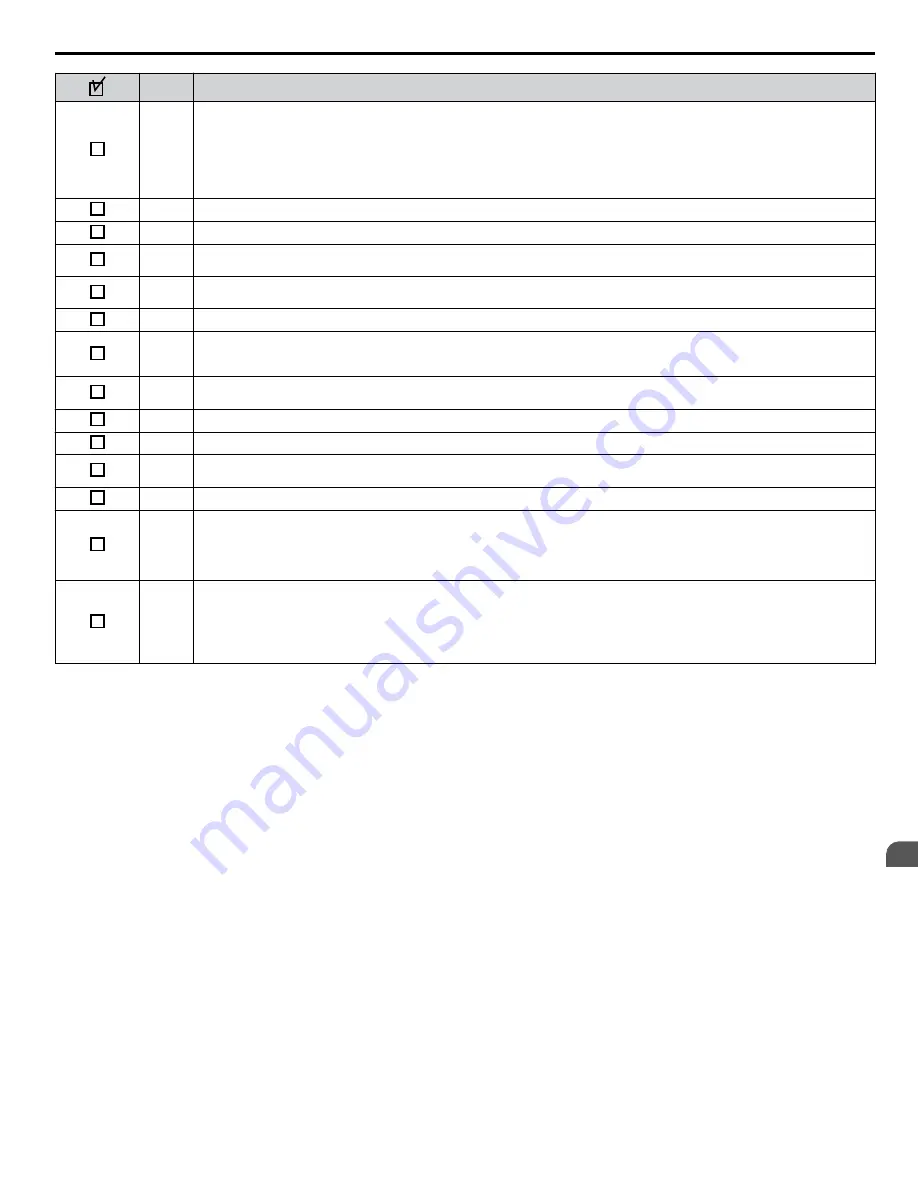
No.
Item
14
WARNING! Always ground the ground terminal. (200 V Class: Ground to 100 Ω or less, 400 V Class: Ground to
10 Ω or less). Improper equipment grounding could result in death or serious injury by contacting ungrounded
electrical equipment.
When using multiple drives, ground each drive directly or daisy-chain to the ground pole(s). DO NOT FORM A LOOP WITH THE
GROUND LEADS.
Refer to Multiple Drive Wiring on page 72
15
Review terminal functions of signal and control circuits.
16
Verify if any customer safety devices are required (e.g. External Pump Fault).
17
Record the following motor nameplate information:
Voltage: _____________________Motor Rated Amps: ____________________
18
Verify that the commercial power supply is within the rated drive input voltage:
Power Supply: ____________________Vac Drive Input Voltage: ____________________Vac
19
Verify that the leads in the three-phase electric motor conduit box are configured for the proper voltage.
20
Ensure Motor Rated Current is less than or equal to drive output amps. If multiple motors are being used, make sure that the Motor
Rated Current sum is less than or equal to drive output amp rating. Please note that if multiple motors are being operated from one
drive, each motor must have its own overload and short circuit protection.
21
Wire all necessary power leads to the drive.
DO NOT CONNECT MOTOR TO DRIVE AT THIS TIME.
2
Wire all necessary
ground
wires to the drive.
23
Wire all necessary
control
wires to the drive.
24
Ensure that the power leads are connected to the R/L1, S/L2 and T/L3 terminals in the drive. Confirm single-phase input or three-
phase input wiring.
25
Tighten all of the three-phase power and ground connections. Please check that all control and signal terminations are tight.
26
Inspect the control circuit connections (including the shield) and determine if a motor safety circuit is connected. If normally closed,
these contacts may be wired in series with the RUN command contacts, which are between terminals S1 and SN of the drive. No
special programming is required.
Alternately, these contacts could be wired between terminals S3 and SN as External Fault Inputs, and may be either normally closed
or normally open contacts.
27
Record any other connections to the drive to determine if special programming is required for the following:
Multi-function Inputs
Multi-function Outputs
Multi-function Digital Inputs
Multi-function Analog Outputs
Network Communications
4.1 Drive Start-Up Preparation
YASKAWA TOEPYAIUPW01A YASKAWA AC Drive - U1000 iQpump Matrix Drive User Manual
89
4
Start-Up Programming & Operation