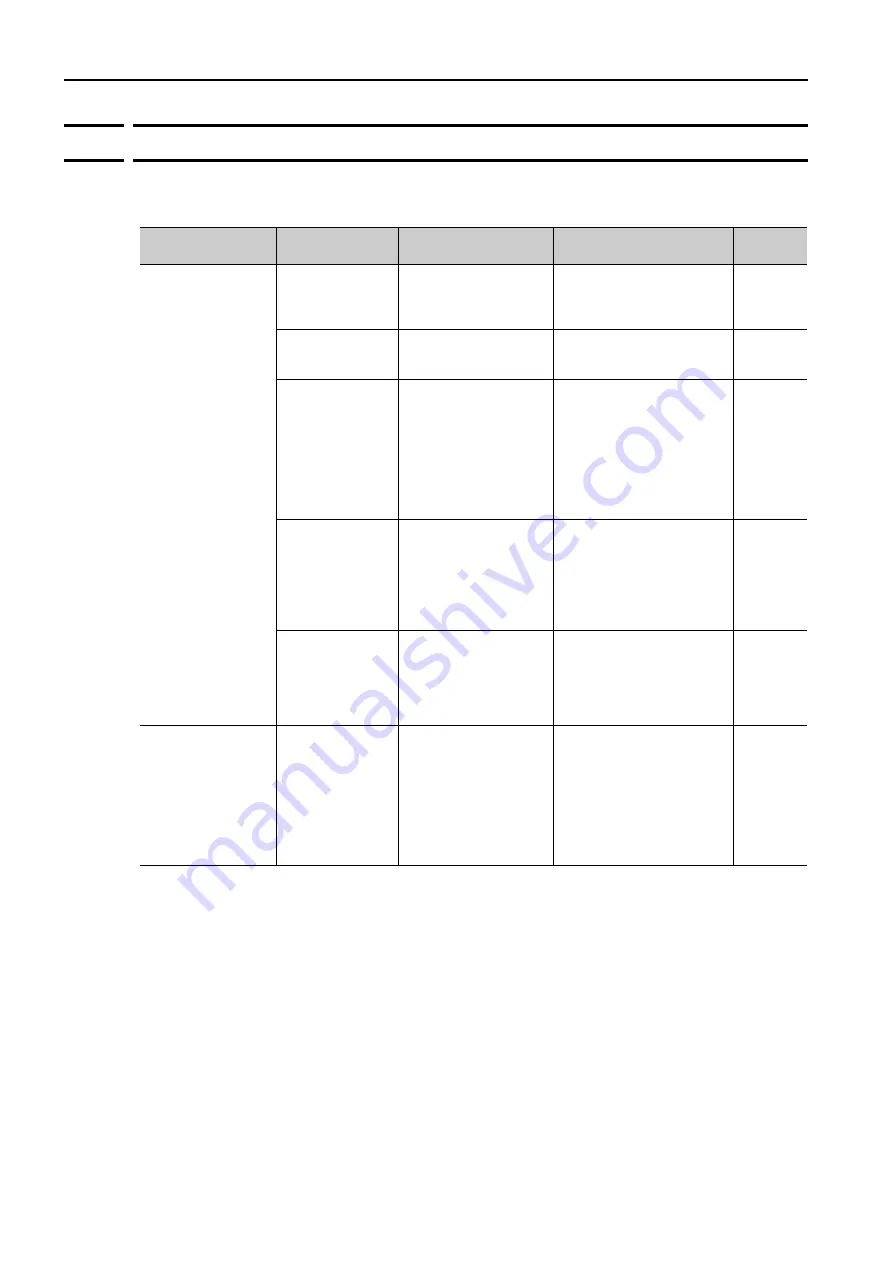
3.2 FT82 SERVOPACK with MECHATROLINK-II Communications References
3.2.6 Troubleshooting Warnings
3-82
3.2.6
Troubleshooting Warnings
The causes of and corrections for the warnings are given in the following table. Contact your
Yaskawa representative if you cannot solve a problem with the correction given in the table.
Warning Number:
Warning Name
Possible Cause
Confirmation
Correction
Reference
A.900:
Position Deviation
Overflow
The Servomotor
U, V, and W wiring
is not correct.
Check the wiring of the
Servomotor’s Main Cir-
cuit Cables.
Make sure that there are no
faulty connections in the
wiring for the Servomotor
and encoder.
–
A SERVOPACK
gain is too low.
Check the SERVO-
PACK gains.
Increase the servo gain,
e.g., by using autotuning
without a host reference.
*
The acceleration
of the position ref-
erence is too high.
Reduce the reference
acceleration and try
operating the SERVO-
PACK.
Reduce the acceleration of
the position reference using
a MECHATROLINK com-
mand. Or, smooth the posi-
tion reference acceleration
by selecting the position
reference filter (ACCFIL)
using a MECHATROLINK
command.
–
The excessive
position deviation
alarm level (Pn520
×
Pn51E/100) is
too low for the
operating condi-
tions.
Check excessive posi-
tion deviation alarm
level (Pn520
×
Pn51E/
100) to see if it is set to
an appropriate value.
Optimize the settings of
Pn520 and Pn51E.
*
A failure occurred
in the SERVO-
PACK.
–
Turn the power supply to
the SERVOPACK OFF and
ON again. If an alarm still
occurs, the SERVOPACK
may be faulty. Replace the
SERVOPACK.
–
A.901:
Position Deviation
Overflow Alarm at
Servo ON
The position devi-
ation when the
servo was turned
ON exceeded the
percentage set
with the following
formula:
(Pn526
×
Pn528/
100)
–
Optimize the setting of
Pn528 (Excessive Position
Error Warning Level at
Servo ON).
–
Continued on next page.