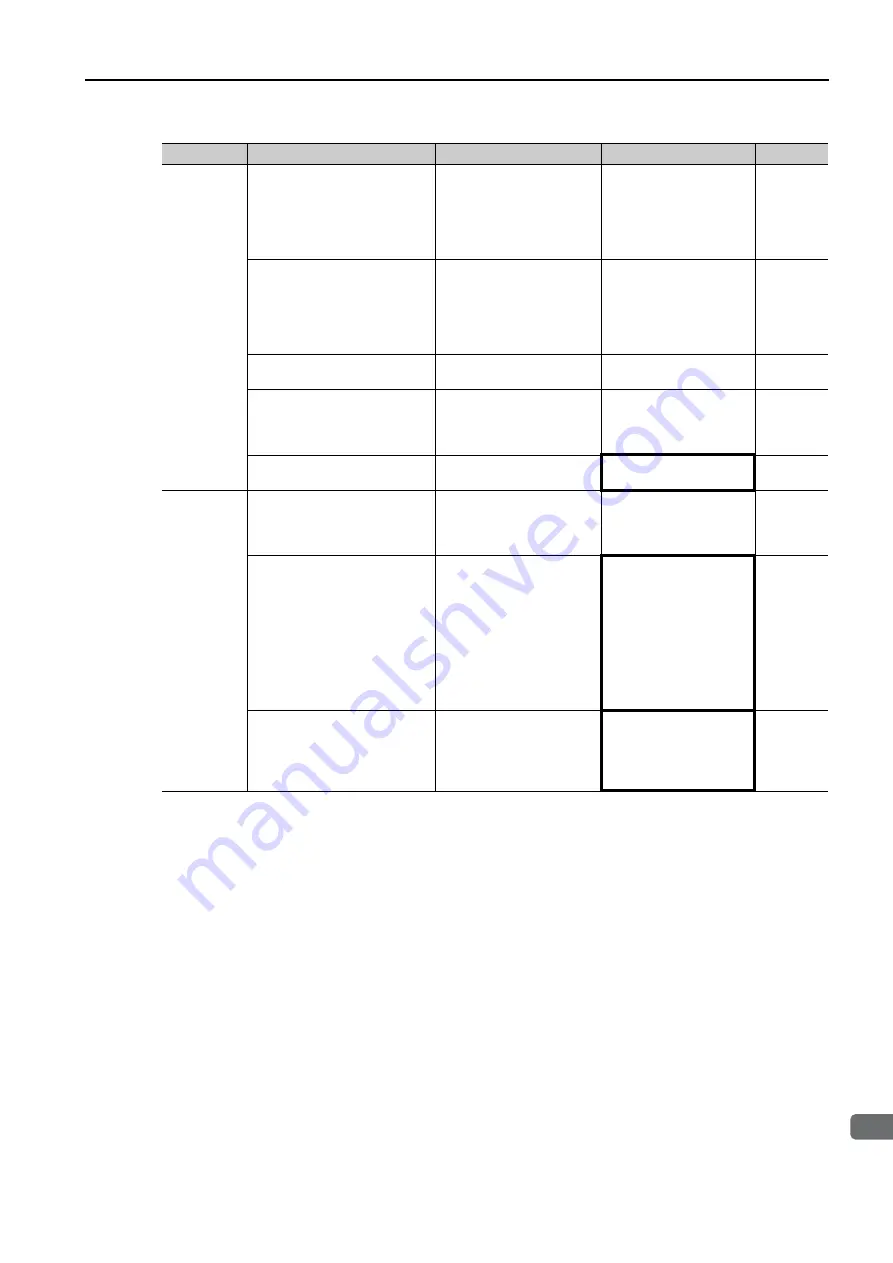
3.1 FT82 SERVOPACKs with Analog Voltage/Pulse Train References
3.1.7 Troubleshooting Based on the Operation and Conditions of the Servomotor
3
Maintenance
3-43
Servomotor
Moves with-
out a Refer-
ence Input
Speed control: The speed
reference input is not appro-
priate.
Check between the
speed reference input (V-
REF) and signal ground
(SG) to see if the control
method and the input
agree.
Correctly set the con-
trol method and input
method.
*
Torque control: The torque
reference input is not appro-
priate.
Check between the
torque reference input (T-
REF) and signal ground
(SG) to see if the control
method and the input
agree.
Correctly set the con-
trol method and input
method.
*
The speed reference offset is
not correct.
The SERVOPACK offset
is adjusted incorrectly.
Adjust the SERVO-
PACK offset.
*
Position control: The refer-
ence pulse input is not
appropriate.
Check the setting of
Pn200 =n.
X (Refer-
ence Pulse Form) and the
sign and pulse signals.
Correctly set the con-
trol method and input
method.
–
A failure occurred in the SER-
VOPACK.
–
Replace the SERVO-
PACK.
–
Dynamic
Brake Does
Not Operate
The setting of Pn001 =
n.
X (Servo OFF or
Alarm Group 1 Stopping
Method) is not suitable.
Check the setting of
Pn001 = n.
X.
Set Pn001 = n.
X
correctly.
–
The dynamic brake resistor is
disconnected.
Check the moment of
inertia, motor speed, and
dynamic brake frequency
of use. If the moment of
inertia, motor speed, or
dynamic brake frequency
of use is excessive, the
dynamic brake resis-
tance may be discon-
nected.
Replace the SERVO-
PACK. To prevent dis-
connection, reduce the
load.
–
There was a failure in the
dynamic brake drive circuit.
–
There is a defective
component in the
dynamic brake circuit.
Replace the SERVO-
PACK.
–
Continued on next page.
Continued from previous page.
Problem
Possible Cause
Confirmation
Correction
Reference