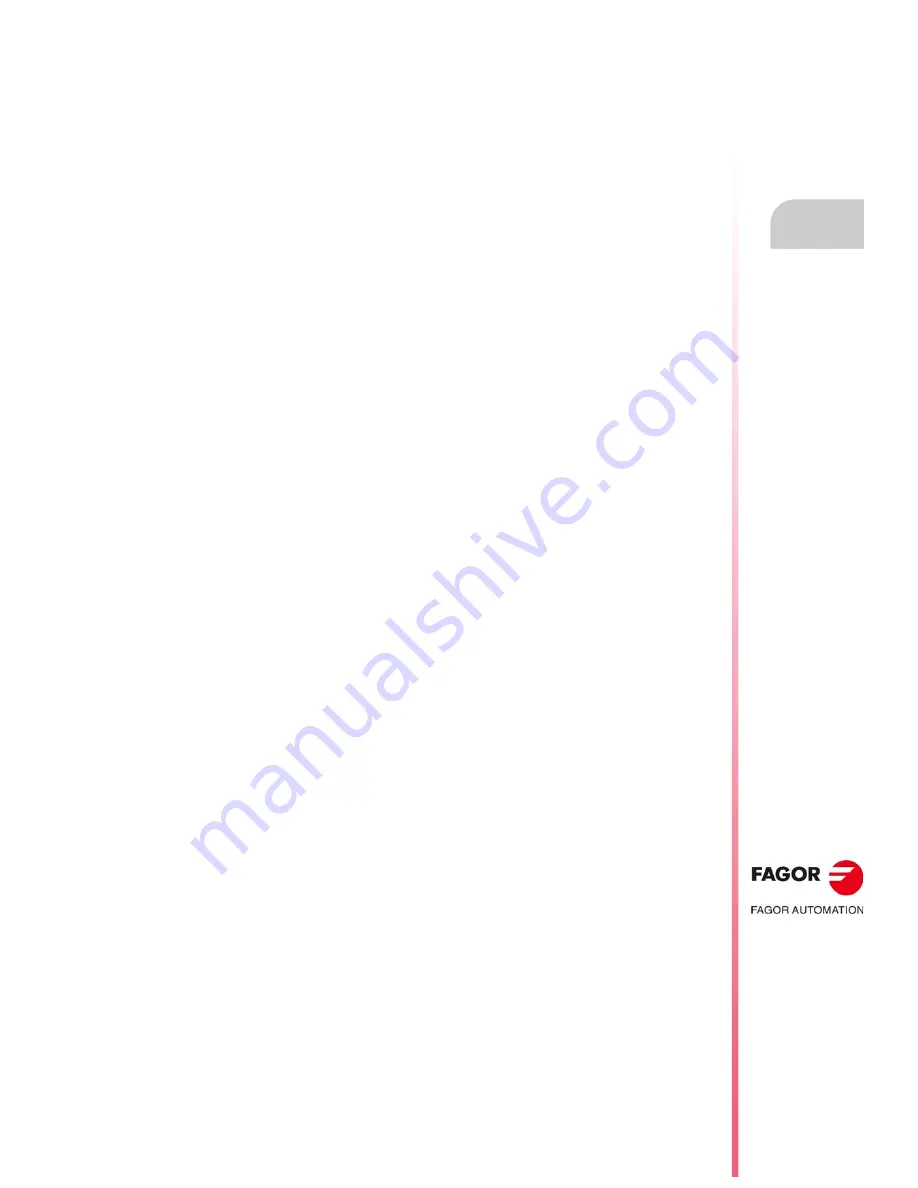
Error solving manual.
CNC 8060
CNC 8065
·9·
(R
EF
: 1709)
0052
'Module difference too small'
DETECTION
During the validation of the machine parameters.
CAUSE
The difference between machine parameters MODUPLIM and MODLOWLIM is
lower than the resolution of the axis.
SOLUTION
Check the resolution of the axis; if correct, increase MODUPLIM or decrease
MODLOWLIM.
0053
'Parameter MGPAXIS repeated in several handwheels'
DETECTION
During the validation of the machine parameters.
CAUSE
There are two or more handwheels assigned to the same axis in the Jog table
parameters.
SOLUTION
One axis can only have one handwheel assigned to it.
0054
'The MOVAXIS and COMPAXIS axis must be different'
DETECTION
During the validation of the machine parameters.
CAUSE
In one of the cross compensation tables, the compensated axis and the axis whose
movement affects the compensated axis are the same.
SOLUTION
The two axes of each cross compensation table must be different (parameters
MOVAXIS and COMPAXIS).
0055
'The same axis is causing and suffering the cross compensation error'
DETECTION
During the validation of the machine parameters.
CAUSE
In the cross compensation tables, checking the different associations of
compensated (affected) axes (parameter COMPAXIS) and those (parameter
MOVAXIS) whose movements affect the other ones, there is an axis whose
movement is affected by itself.
SOLUTION
Check the relationship between the defined cross compensations. Check parameters
MOVAXIS and COMPAXIS of the defined cross compensations.
0056
'Compensation table positions not in ascending order'
DETECTION
During the validation of the machine parameters.
CAUSE
In the compensation tables, the points to be compensated are not ordered correctly
or the value to compensate in all the points have a zero value.
SOLUTION
The POSITION parameter within the compensation tables must have ascending
values. The value to compensate cannot be zero in all the points.
0057
'Compensation table with error slope greater than 1'
DETECTION
While validating the machine parameters (leadscrew error compensation table)
CAUSE
In the leadscrew compensation tables, the difference between two consecutive errors
is greater than the gap between those points.
SOLUTION
The error slope in leadscrew compensation tables cannot be greater than 1. Increase
the gap between points; if this is not possible, the error entered for the leadscrew is
so large that cannot be compensated for.
0058
'The CNC must be restarted too assume the changes in the HMI table,'
DETECTION
During the validation of the machine parameters.
CAUSE
The CNC application must be restarted in order to assume the changes made to the
HMI table.
SOLUTION
Restart the CNC.
0059
'The CNC must be restarted too assume the changes in the tool magazine table,'
DETECTION
During the validation of the machine parameters.
CAUSE
The CNC application must be restarted in order to assume the changes made to the
tool magazine table.
SOLUTION
Restart the CNC.
0060
'The maximum jogging feedrate exceeds the maximum feedrate set for the axis'
DETECTION
During the validation of the machine parameters.
CAUSE
Parameter MAXMANFEED is greater than G00FEED.
SOLUTION
Decrease the value of parameter MAXMANFEED; it must be lower than G00FEED.
0061
'The manual rapid feedrate exceeds the maximum feedrate set for the axis'
DETECTION
During the validation of the machine parameters.
CAUSE
Parameter JOGRAPFEED is greater than G00FEED.
SOLUTION
Decrease the value of parameter JOGRAPFEED; it must be lower than G00FEED.
Содержание 8065
Страница 1: ...Ref 1709 8060 8065 CNC Error solving manual...
Страница 4: ...BLANK PAGE 4...
Страница 216: ...Error solving manual CNC 8060 CNC 8065 216 REF 1709...
Страница 217: ...Error solving manual CNC 8060 CNC 8065 217 User notes REF 1709...
Страница 218: ...Error solving manual CNC 8060 CNC 8065 218 User notes REF 1709...
Страница 219: ...Error solving manual CNC 8060 CNC 8065 219 User notes REF 1709...