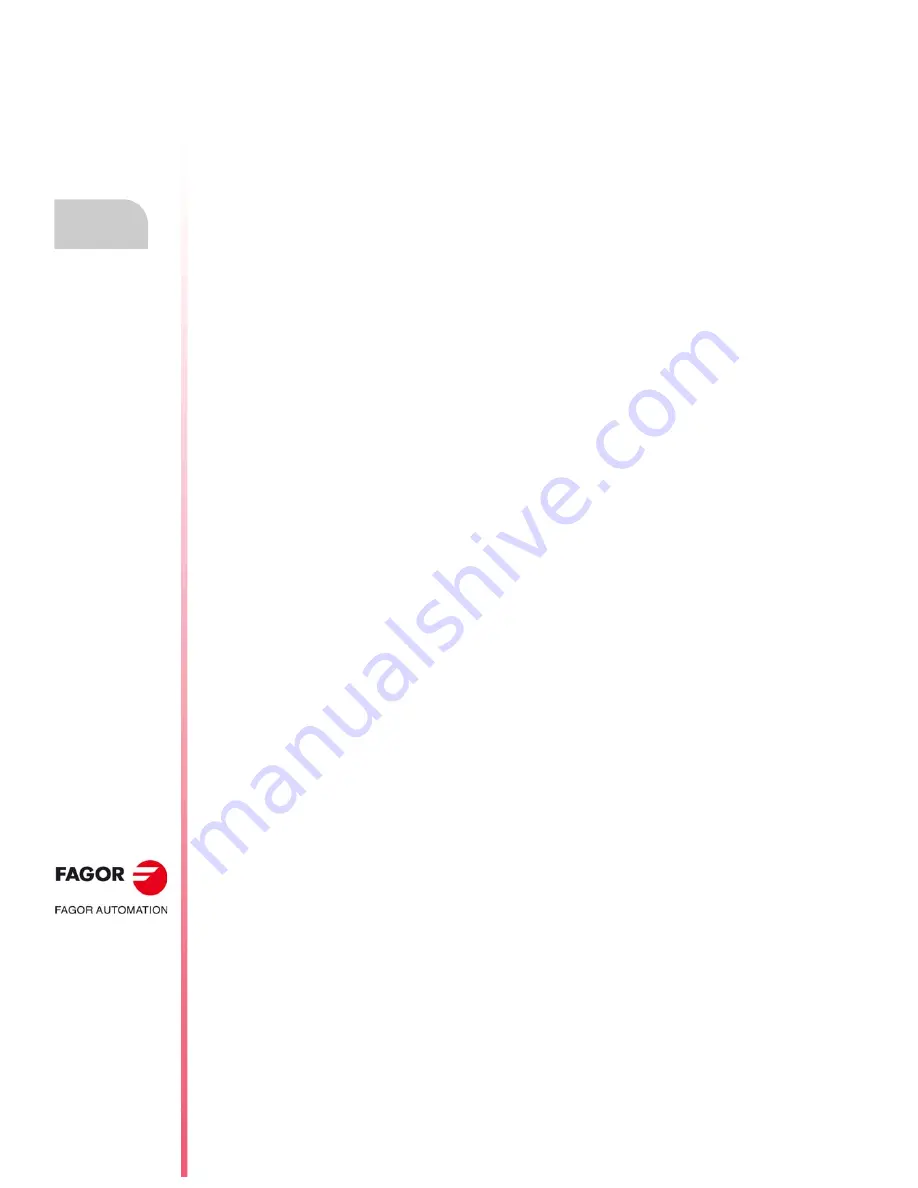
Error solving manual.
CNC 8060
CNC 8065
·56·
(R
EF
: 1709)
1459
'#POLY: Wrong starting point'
DETECTION
During execution.
CAUSE
The starting point of the polynomial is not the same as the current position.
SOLUTION
Modify the independent term of the polynomial for each axis making the starting point
of the polynomial the same as the end position of the previous block.
1461
'G9: The arc's intermediate point has been programmed wrong'
DETECTION
During execution.
CAUSE
One or both coordinates of the arc's intermediate point have not been programmed.
SOLUTION
Function G9 requires the programming of both coordinates of the arc's intermediate
point.
1462
'G8: the tangent path cannot be calculated'
DETECTION
During execution.
CAUSE
An arc tangent to the previous path cannot be done with the programmed radius and
end point.
SOLUTION
Check the program.
1463
'G9: Circular path programmed wrong'
DETECTION
During execution.
CAUSE
No arc can go through those three points.
SOLUTION
Define two points in the block with a G9, that define an arc with the end point of the
previous movement. Bear in mind that all three points must be different and cannot
be in line.
1464
'Programmed rotary axis out of the range of the module'
DETECTION
During execution.
CAUSE
The absolute coordinate (G90) programmed for the MODULE type rotary axis is
wrong.
SOLUTION
The coordinate programmed for the axis must be between the limits set by its machine
parameters MODUPLIM and MODLOWLIM.
1465
'Functions RTCP and TLC are incompatible with each other'
DETECTION
During execution.
CAUSE
The CNC has tried to activate one of the functions while the other one was active.
SOLUTION
Both functions cannot be active at the same time.
1466
'G8 cannot be programmed as second motion block for G36/G37/G38/G39'
DETECTION
During execution.
CAUSE
A G8 block cannot be the second motion block of one of the functions
G36/G37/G38/G39. On one hand, these functions do not have an intermediate block
to make the path joining two blocks and, on the other hand, function G8 does not have
a previous block to be tangent to.
SOLUTION
The second motion block of a G36/G37/G38/G39 function must be G0/G1/G2/G3.
1467
'POSLIMIT/NEGLIMIT cannot exceed the value of the machine parameter'
DETECTION
During execution.
CAUSE
The value to be written in variables V.A.POSLIMIT.xn and V.A.NEGLIMIT.xn cannot
exceed the value of machine parameters POSLIMIT and NEGLIMIT for that axis.
SOLUTION
Check the program.
1468
'G30: Polar origin programmed wrong'
DETECTION
During execution.
CAUSE
One of the two coordinates of the Polar origin is missing in the G30 function.
SOLUTION
Check the program. The coordinates of the Polar origin must be programmed in both
main axes.
1469
'Negative or zero radius not allowed'
DETECTION
During execution.
CAUSE
In a movement in Polar coordinates, the Polar radius is negative or zero.
SOLUTION
The Polar radius must always be greater than zero. When programming with
incremental coordinates, the programmed value may be negative or zero, but not the
absolute Polar radius.
Содержание 8065
Страница 1: ...Ref 1709 8060 8065 CNC Error solving manual...
Страница 4: ...BLANK PAGE 4...
Страница 216: ...Error solving manual CNC 8060 CNC 8065 216 REF 1709...
Страница 217: ...Error solving manual CNC 8060 CNC 8065 217 User notes REF 1709...
Страница 218: ...Error solving manual CNC 8060 CNC 8065 218 User notes REF 1709...
Страница 219: ...Error solving manual CNC 8060 CNC 8065 219 User notes REF 1709...