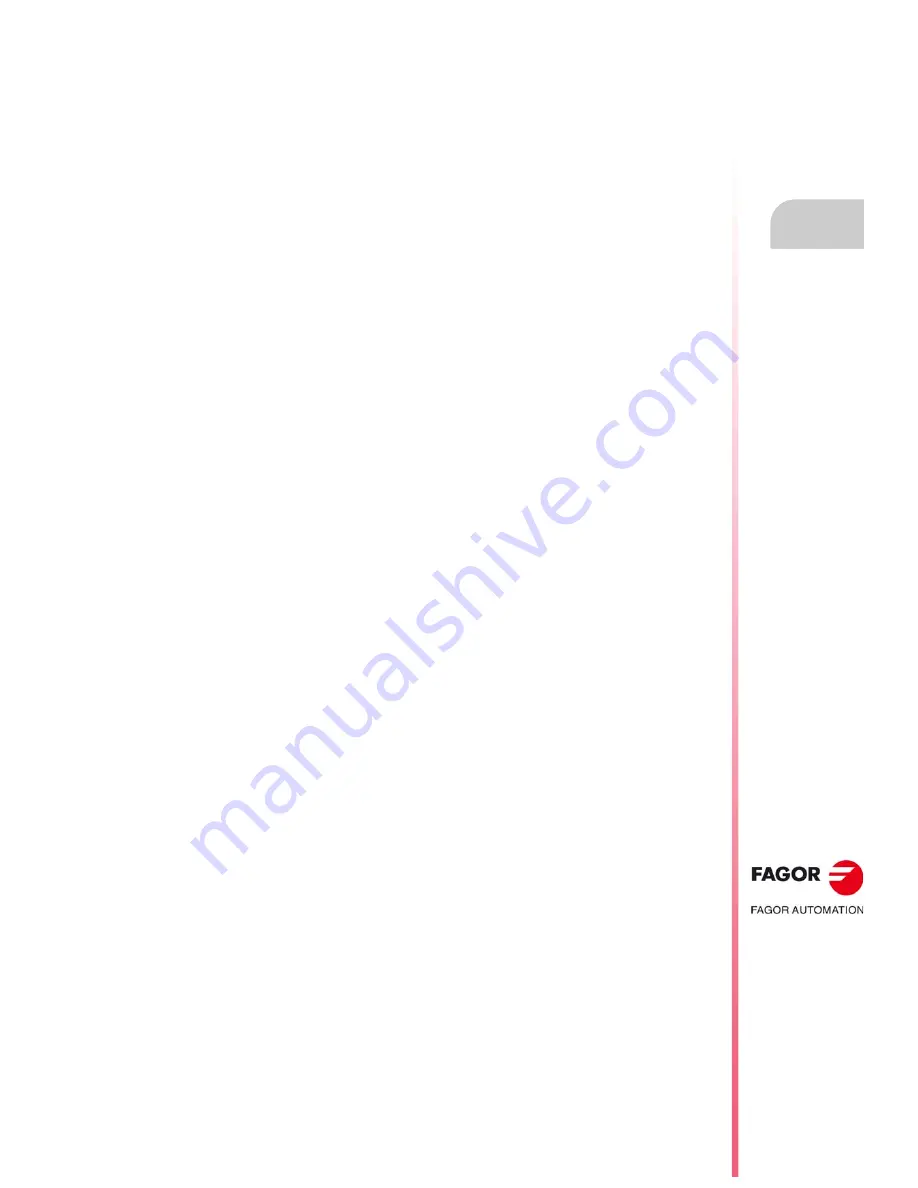
Error solving manual.
CNC 8060
CNC 8065
·7·
(R
EF
: 1709)
0027
The axis is not mechatrolink.
DETECTION
When defining variables defined in a channel of the oscilloscope.
CAUSE
The variable or parameter is unique to a mechatrolink axis, however, the axis
requesting the variable or parameter is not a mechatrolink axis
SOLUTION
Select a Mechatrolink axis. There must be an axis variable or parameter for the
requested axis.
0029
'Only MLINKII admits DRV or MLINK variables in a channel of the oscilloscope'
DETECTION
When defining variables defined in a channel of the oscilloscope.
CAUSE
The variable assigned to the channel of the oscilloscope is not Mlink-II.
SOLUTION
Access to variables and/or parameters of the Mechatrolink devices is only available
for the Mlink-II mode with 32 bytes.
0030
'The axis of the variable must be programmed using its name'
DETECTION
During execution.
CAUSE
In some variable of the drive (DRV), the axis is programmed using its logic number
or index in the channel.
SOLUTION
In these variables, the axis must be programmed using its name.
0031
'Only MLINKII admits mechatrolink parameters in the oscilloscope'
DETECTION
When defining parameters in a channel of the oscilloscope.
CAUSE
The parameter assigned to the channel of the oscilloscope is not Mlink-II.
SOLUTION
Access to variables and/or parameters of the Mechatrolink devices is only available
for the Mlink-II mode with 32 bytes.
0036
'The CNC was not turned off properly, the active tool must be loaded'
DETECTION
During CNC startup.
CAUSE
The CNC data related to the active tool that are saved into the disk is not valid. The
file that contains these data does not exist, is not accessible or is corrupt.
SOLUTION
Define in the tool table which tool is active, and if necessary, make a tool change. If
the error persists after powering the CNC up several times, contact your supplier.
0040
'M before-before or Before-After with subroutine does not admit movements in the block'
DETECTION
During the validation of the machine parameters.
CAUSE
In the M functions table, there is a function with associated subroutine and Before-
Before or Before-After synchronization type.
SOLUTION
The CNC always executes the subroutine associated with an M function at the end
of the block where the function has been programmed. Define the M function without
synchronization or with After-After synchronization.
0041
'Duplicate M in the table'
DETECTION
During the validation of the machine parameters.
CAUSE
There is a duplicate function in the M functions table.
SOLUTION
Correct the definition of the functions. The table cannot have two M functions with
the same number.
0042
'Wrong machine parameter value'
DETECTION
During the validation of the machine parameters.
CAUSE
The machine parameter has the wrong value.
SOLUTION
Set the machine parameter with a value within the admitted limits. The error window
shows which is the wrong parameter and the maximum and minimum value admitted.
0043
'Restart the CNC to assume the new value'
DETECTION
During the validation of the machine parameters.
CAUSE
The user has changed a machine parameter and the CNC application must be
restarted in order to assume its new value.
SOLUTION
Restart the CNC.
Содержание 8065
Страница 1: ...Ref 1709 8060 8065 CNC Error solving manual...
Страница 4: ...BLANK PAGE 4...
Страница 216: ...Error solving manual CNC 8060 CNC 8065 216 REF 1709...
Страница 217: ...Error solving manual CNC 8060 CNC 8065 217 User notes REF 1709...
Страница 218: ...Error solving manual CNC 8060 CNC 8065 218 User notes REF 1709...
Страница 219: ...Error solving manual CNC 8060 CNC 8065 219 User notes REF 1709...