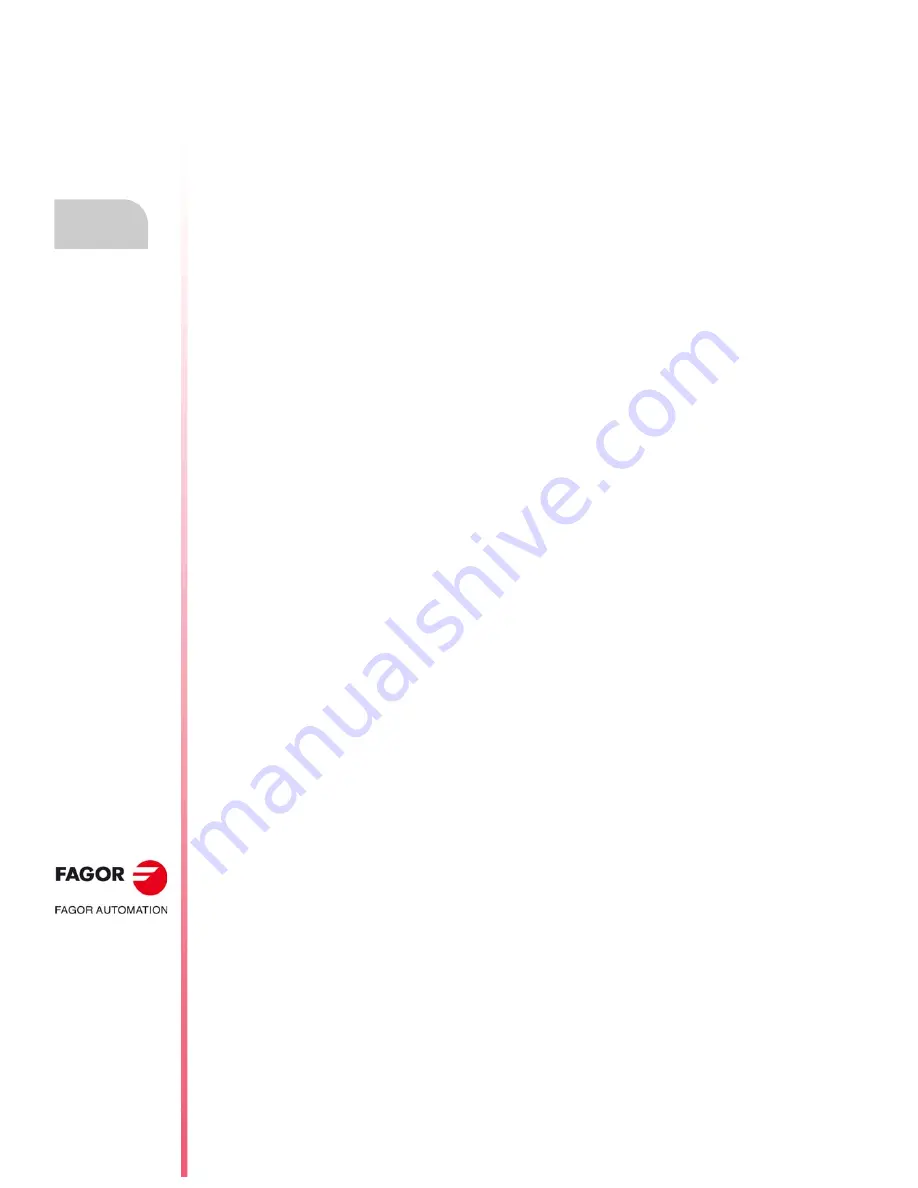
Error solving manual.
CNC 8060
CNC 8065
·42·
(R
EF
: 1709)
1292
'M function programmed twice'
DETECTION
During execution.
CAUSE
The same M function has been programmed more than once in the block.
SOLUTION
Program both functions in different blocks.
1293
'H function programmed twice'
DETECTION
During execution.
CAUSE
The same H function has been programmed more than once in the block.
SOLUTION
Program both functions in different blocks.
1301
'The tool length transformation exceeds the valid numeric format'
DETECTION
During execution.
CAUSE
The tool length transformation exceeds the valid numeric format.
SOLUTION
Modify the values of the length transformation or those of the tool.
1302
'Wrong character in the name'
DETECTION
During execution.
CAUSE
Wrong character in the name of a label, subroutine or variable.
SOLUTION
Check the program.
1303
'Variable name too long'
DETECTION
During execution.
CAUSE
Too many characters for the name of the variable.
SOLUTION
The maximum number of characters allowed is 13.
1304
'Wrong spindle speed'
DETECTION
During execution.
CAUSE
The programmed speed is too low.
SOLUTION
Check the program.
1305
'Programming not allowed while #MCS is active'
DETECTION
During execution.
CAUSE
The CNC does not allow executing the programmed function if the MCS function is
active. Some incompatible functions are:
• Zero offsets (G54-G59, G159, G92, G158, G53) on/off
• Measuring offset (G101, G102) on/off.
• Fixtures on/off ("V.G.FIX" variable).
• Mirror (G11/G12/G13/G14) image on/off.
• Programming in radius/diameters (G151/G152).
• Activate incremental programming (G91).
• Programming in mm/inches (G70/G71).
• Scaling factor (G72).
• Movement in G0, G1, G2, G3, G8 or G9 in Polar coordinates.
• Threading G63 or G33 in Polar coordinates.
• Polar origin (G30).
• Pattern rotation (G73).
• Instructions #FACE, #CYL and #RTCP.
SOLUTION
Check the program.
1306
'The kinematics cannot be changed while tool radius compensation is active'
DETECTION
During execution.
CAUSE
The CNC has tried to change the kinematics while tool radius compensation was
active.
SOLUTION
Cancel the compensation to define the new work plane.
1308
'An axis of the active transformation cannot be a slave'
DETECTION
During execution.
CAUSE
The slave axis of the coupling is part of the active kinematics.
SOLUTION
Cancel the kinematics to be able to couple the axis. The axis involved in the active
kinematics can be master of a coupling.
Содержание 8065
Страница 1: ...Ref 1709 8060 8065 CNC Error solving manual...
Страница 4: ...BLANK PAGE 4...
Страница 216: ...Error solving manual CNC 8060 CNC 8065 216 REF 1709...
Страница 217: ...Error solving manual CNC 8060 CNC 8065 217 User notes REF 1709...
Страница 218: ...Error solving manual CNC 8060 CNC 8065 218 User notes REF 1709...
Страница 219: ...Error solving manual CNC 8060 CNC 8065 219 User notes REF 1709...