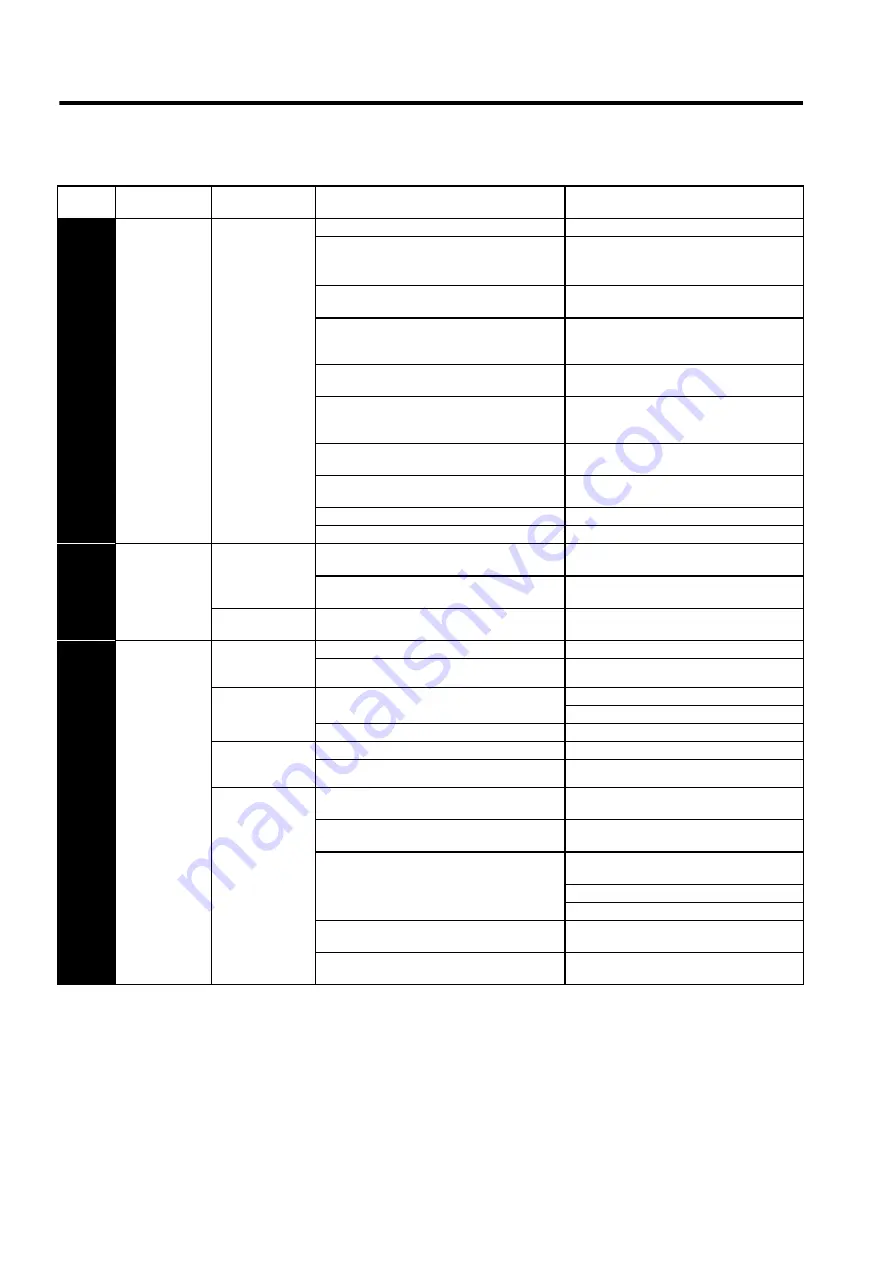
10 Inspection, Maintenance, and Troubleshooting
10.1.6 Troubleshooting of Alarm and Warning
10-14
A.Cb
Encoder
Echoback Error
Occurred when the
control power sup-
ply was turned ON
or during operation.
The encoder wiring and contact are incorrect.
Correct the encoder wiring.
Noise interference occurred due to incorrect encoder
cable specifications.
Use tinned annealed copper twisted-pair or
twisted-pair shielded wire with a core of at least
0.12 mm
2
(0.0002 in
2
).
Noise interference occurred because the wiring dis-
tance for the encoder cable is too long.
The wiring distance must be 20m (65.6 ft) max.
Noise interference occurred on the signal line,
because the encoder cable is bent and the sheath is
damaged.
Correct the encoder cable layout.
The encoder cable is bundled with a high-current
line or near a high-current line.
Correct the encoder cable layout so that no surge
is applied.
The FG electrical potential varies because of the
influence from such machines on the servomotor
side as welders.
Ground the machine separately from PG side FG.
Noise interference occurred on the signal line from
the encoder.
Take measures against noise for the encoder wir-
ing.
Excessive vibration and shocks to the encoder was
applied.
Reduce the machine vibration or mount the servo-
motor securely.
An encoder fault occurred.
Replace the servomotor.
A SERVOPACK board fault occurred.
Replace the SERVOPACK.
A.CC
Multiturn Limit
Disagreement
Occurred when the
control power sup-
ply was turned ON.
The parameter settings for the SERVOPACK are
incorrect.
Correct the setting of Pn205 (0 to 65535).
The multiturn limit value for the encoder is not set or
was changed.
Execute Fn013 at the occurrence of alarm.
Occurred during
normal operation.
A SERVOPACK board fault occurred.
Replace the SERVOPACK.
A.d0
Position Error
Pulse Overflow
(In servo ON sta-
tus, the position
error pulses
exceed the over-
flow level set in
the parameter
Pn505.)
Occurred when the
control power sup-
ply was turned ON.
The overflow level (Pn505) is incorrect.
Make the value set in the Pn505 to other than 0.
A SERVOPACK board fault occurred.
Replace the SERVOPACK.
Occurred at the ser-
vomotor high-speed
rotation.
The contact in the servomotor U, V, and W wirings
is faulty.
Correct the servomotor wiring.
Correct the encoder wiring.
A SERVOPACK board fault occurred.
Replace the SERVOPACK.
The servomotor did
not run with posi-
tion reference input.
Wirings of the servomotor U, V, and W are incorrect.
Correct the servomotor wiring.
A SERVOPACK board fault occurred.
Replace the SERVOPACK.
Normal movement,
but occurred with a
long distance refer-
ence input.
The SERVOPACK gain adjustment is improper.
Increase the speed loop gain (Pn100) and position
loop gain (Pn102).
The V-REF input voltage and the Pn300 setting are
incorrect.
Lower the reference speed to the speed limit
value.
The position reference pulse frequency is too high.
Adjust slowly the position reference pulse fre-
quency.
Apply the smoothing function.
Correct the electronic gear ratio.
Setting of the position error pulse overflow alarm
level (Pn505) is incorrect.
Set the parameter Pn505 to proper value.
The servomotor specifications do not meet the load
conditions such as torque and moment of inertia.
Reconsider and correct the load and servomotor
capacity.
Table 10.6 Alarm Display and Troubleshooting (Cont’d)
Alarm
Display
Alarm Name
Situation at Alarm
Occurrence
Cause
Corrective Actions
Summary of Contents for SGDH
Page 435: ...8 3 8...