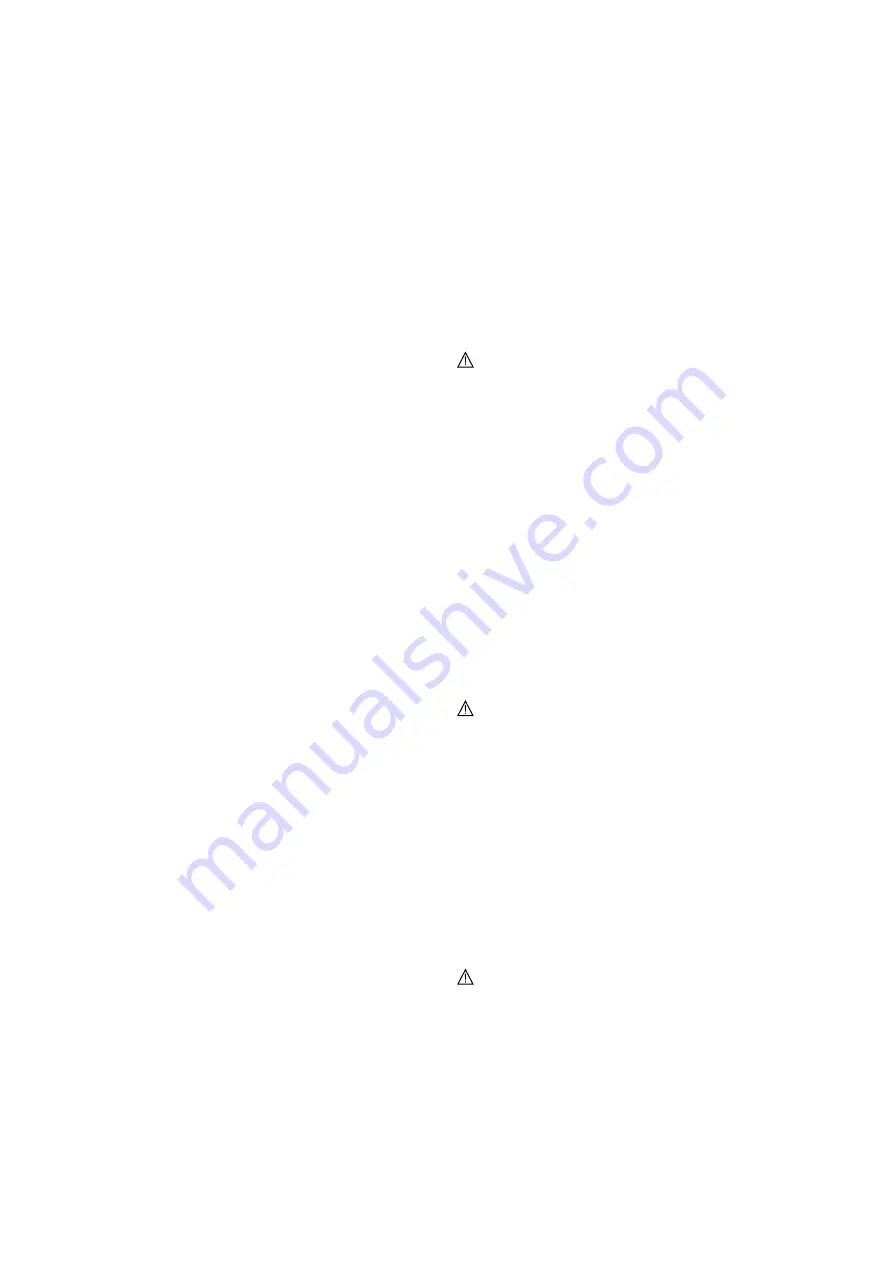
5.7.2 Synthetic hose for aluminium wires
6.2.3 Arc voltage
Carry out operations
1, 2, 3
as given for the steel hose (ignore operations
4, 5, 6, 7, 8
).
Can be adjusted at short intervals (steps) by switches on the power source. Voltage
must comply with the chosen speed of wire advancement (current), and with the wire
9-
Re-tighten the contact tip for aluminium, making sure it comes into contact with the
diameter and shielding gas used. This may be set out in the following equation giving the
hose.
medium value:
10-
At the other end of the hose (torch connector end) insert the brass nipple and the OR
U = (14 + 0,05 x l )
ring and, keeping slight pressure on the hose, tighten the hose locking nut.
2
2
Extract the capillary pipe for steel hoses from the wire feeder torch connector.
where :U = arc voltage in volts;
2
l = welding current in amperes.
11-
THE CAPILLARY PIPE IS NOT REQUIRED for aluminium hoses of diameter 1.6-
2
2.4mm (coloured yellow); the hose is therefore inserted into the torch connector
Remember that in comparison with the no-load voltage supplied for each step, the arc
without it.
voltage will be less 2-4V for every 100A delivered. The argon/CO mixtures require arc
2
Cut the capillary pipe for aluminium hoses of diameter 1.2-1.6mm (coloured red) to
voltage of 1-2V less than that required with CO .
2
approx. 2mm shorter than the steel pipe, and insert it into the free end of the hose.
12-
Insert and lock the torch into the wire feeder connector, mark the hose at 1-2mm
6.2.4 Weld quality
from the rollers, take the torch out again.
The quality of the weld seam is higher when less spatter is produced. this is determined
13-
Cut the hose to the required size, without distorting the inlet hole.
principally by a correct balance of the welding parameters: current (wire speed), wire
Reassemble the torch in the wire feeder connector and assemble the gas nozzle.
diameter, arc voltage etc., as well as a correct choice of choke intakes.
In the same way the torch position must comply with the data in figure
(FIG. M)
in order
to avoid excessive spatter and faults on the weld seam. The weld speed (i.e. the
6. WELDING: DESCRIPTION OF THE PROCEDURE
advancement speed along the joint) is also a determining factor for the correct
6.1 METHODS OF METAL TRANSFER
execution of the seam. This is particularly important for good penetration and correct
6.1.1 Short arc
shape of the seam.
The melting of the electrode wire and the detachment of the drop is produced by
The most common welding flaws are summarized in
TAB.5.
repeated short circuits (up to 200 times per second) from the tip of the wire to the molten
pool.
Carbon and mild steels
7. MAINTENANCE
_____________________________________________________________________________________________________________________
- Suitable wire diameter:
0.6-1.2mm
- Welding current range:
40-210A
WARNING! BEFORE CARRYING OUT MAINTENANCE OPERATIONS MAKE
-
Arc voltage range:
13-23V
- Suitable gases:
CO , mix Ar/CO , Ar/CO /O
SURE THE WELDING MACHINE IS SWITCHED OFF AND DISCONNECTED FROM
2
2
2
2
THE MAIN POWER SUPPLY.
Stainless steels
_____________________________________________________________________________________________________________________
- Suitable wire diameter:
0.8-1mm
- Welding current range:
40-160A
7.1 ROUTINE MAINTENANCE
-
Arc voltage range:
14-20V
ROUTINE MAINTENANCE OPERATIONS CAN BE CARRIED OUT BY THE
- Suitable gases:
mix Ar/O , Ar/CO (1-2%)
2
2
OPERATOR.
Aluminium and alloys
- Suitable wire diameter:
0.8-1.6mm
7.1.1.Torch
- Welding current range:
75-160A
-
Do not put the torch or its cable on hot pieces; this would cause the insulating
-
Arc voltage range:
16-22V
materials to melt, making the torch unusable after a very short time.
- Suitable gases:
Ar 99.9%
-
Make regular checks on the gas pipe and connector seals.
- Wire stick out:
5-12mm
-
Every time the wire reel is changed, blow out the wire-guide hose using dry
compressed air (max. 5bar) to make sure it is not damaged.
Generally, the
contact tip
should be flush with the nozzle or protrude slightly when
-
To control, before every I use, check the wear and correct assembly of the parts at
using the thinnest wires and lowest arc voltages; the length of free wire (stick-out) will
the end of the torch: nozzle, contact tip, gas diffuser.
normally be between 5 and 12mm. Select the
minimum reactance outlet
for carbon or
mild steels with C0 gas (wire diameters 0.8-1.2mm) and
for the same material
7.1.2 Wire feeder
average
2
- Make frequent checks on the state of wear of the wire feeder rollers, regularly
with Ar/CO gas,
high
for stainless steel and aluminium.
2
remove the metal dust deposited in the feeder area (rollers and wire-guide infeed
and outfeed).
Application:
Welding in all positions, on thin material or for the first passage in bevelled
edges, with the advantage of limited heat transfer and highly controllable pool.
7.2 EXTRAORDINARY MAINTENANCE
EXTRAORDINARY MAINTENANCE OPERATIONS SHOULD BE CARRIED OUT
Note:
SHORT ARC transfer for welding aluminium and alloys should be used with great
ONLY AND EXCLUSIVELY BY SKILLED OR AUTHORISED ELECTRICAL-
care (especially with wires of diameter >1mm) because the risk of melting defects may
MECHANICAL TECHNICIANS.
arise.
_____________________________________________________________________________________________________________________
6.1.2 Spray arc
Higher voltages and currents than for "short arc" are used here to achieve the melting of
WARNING! BEFORE REMOVING THE WELDING MACHINE PANELS AND
the wire. The wire tip does not come into contact with the molten pool; an arc forms from
WORKING INSIDE THE MACHINE MAKE SURE THE WELDING MACHINE IS
the tip and through it flows a stream of metallic droplets. These are produeced by the
SWITCHED OFF AND DISCONNECTED FROM THE MAIN POWER SUPPLY
continuous melting of the electrode wire without short-circuits involved.
OUTLET.
Carbon and mild steels
_____________________________________________________________________________________________________________________
- Suitable wire diameter:
0.8-1.6mm
If checks are made inside the welding machine while it is live, this may cause
-
Welding current range:
180-450A
-
Arc voltage range :
24-40V
serious electric shock due to direct contact with live parts and/or injury due to
- Suitable gases :
mix Ar/CO , Ar/CO /O
direct contact with moving parts.
2
2
2
- Inspect the welding machine regularly, with a frequency depending on use and the
Stainless steels
dustiness of the environment, and remove the dust deposited on the transformer,
- Suitable wire diameter:
1-1.6mm
reactance and rectifier using a jet of dry compressed air (max. 10bar).
-
Welding current range:
140-390A
- Do not direct the jet of compressed air on the electronic boards; these can be
-
Welding voltage range :
22-32V
cleaned with a very soft brush or suitable solvents.
-
Suitable gases :
mix Ar/O , Ar/CO (1-2%)
2
2
- At the same time make sure the electrical connections are tight and check the wiring
Aluminium and alloys
for damage to the insulation.
- Suitable wire diameter:
0.8-1.6mm
- At the end of these operations re-assemble the panels of the welding machine and
-
Welding current range:
120-360A
screw the fastening screws right down.
-
welding voltage range :
24-30V
- Never, ever carry out welding operations while the welding machine is open.
-
suitable gases :
Ar 99.9%
The
contact tip
should generally be 5-10mm inside the nozzle, the higher the arc
8. TROUBLESHOOTING
(TAB.6)
_____________________________________________________________________________________________________________________
voltage the further inside; the length of free wire (stick-out) should normally be between
10 and 12mm. Use the
minimum reactance outlet.
WARNING! CARRYING OUT CERTAIN CHECKS IMPLIES THE RISK OF
Application:
Horizontal welding with thicknesses of at least 3-4mm (very fluid pool);
CONTACT WITH LIVE AND/OR MOVING PARTS.
_____________________________________________________________________________________________________________________
execution rate and deposit rate are very high (high heat transfer).
Before carrying out any operation on the wire feeder or inside the welding machine it is
6.2 ADJUSTING THE WELDING PARAMETERS
absolutely necessary to refer to section 7
MAINTENANCE .
6.2.1 Shielding gas
shielding gas flow rate should be:
short arc:
8-14 l/min
spray arc:
12-20 l/min
depending on welding current intensity and nozzle diameter.
6.2.2 Welding current (FIG. L)
Is determined for a given wire diameter by its own advancement speed. Remember that
for a given current the wire advancement speed is inversely proportional to the diameter
used.
Approximate values for the current in manual welding mode for the most commonly
used wires are given in the table (
TAB. 4
).
- 8 -