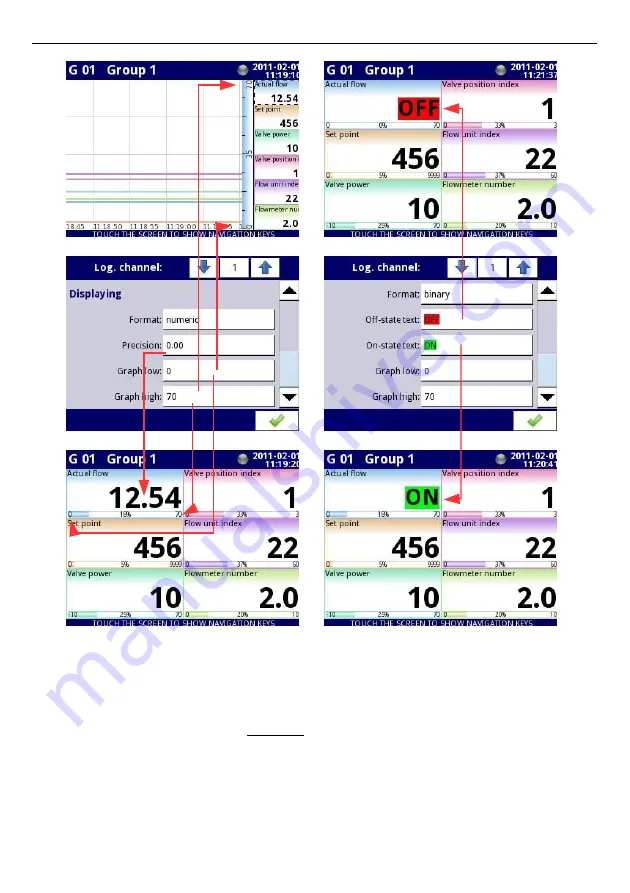
User Manual For - CONTROLLER/DATA RECORDER MultiCon CMC-99/141
Fig. 7.45. Input channels menu – 2 different kinds of Displaying parameters
To calculate the percentage which will be displayed on the indicator, the device is using
the following equation:
where:
R – result
V – value in logical channel
Lo – Graph low value in logical channel
Hi – Graph high value in logical channel
87
R
=
V
−
Lo
Hi
−
Lo
⋅
100 %