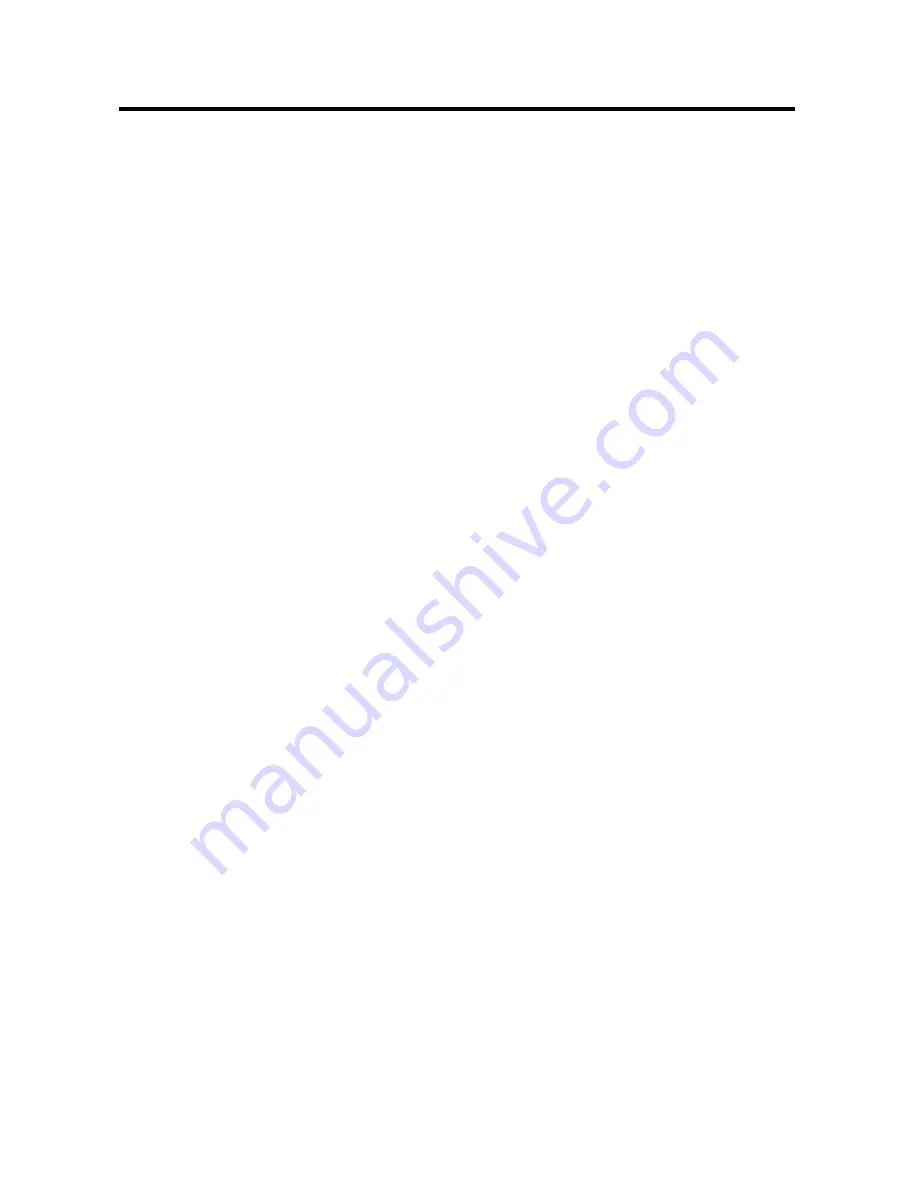
28 February 1989
9. ELECTRICAL COMPONENT DESCRIPTIONS
Index
No.
Name
Motors
55
50
2
62
3
69
57
27
12
Main Motor
Fusing Exhaust
Fan
Cooling Fan
Vacuum Fan
Scanner Drive
3rd Scanner Drive
Lens Drive
Jogger
1st Lift Motor
Magnetic Clutches
22
11
13
18
7
21
5
39
15
Registration
1st Paper Feed
2nd Paper Feed
3rd Paper Feed
Toner Supply
Relay roller
Development Drive
Duplex/Overlay
Transport
1st Pick-up
Function
Symbol
Drives all main unit components except
optics unit and fans. (100 Vac)
Removes heat from around the fusing unit.
(100 Vac)
Prevents build up of hot air in the optics
cavity. (100 Vac)
Provides suction so paper is held firmly on
the transport belt. (100 Vac)
Drives the scanner. (dc servo)
Positions the 3rd scanner. (dc stepper)
Positions the lens.
Drives the jogger plates to keep paper
evenly stacked on the jogger tray. (dc
stepper)
Lifts paper to the appropriate feed position.
Drives the registration rollers.
Starts paper feed from the first feed sta-
tion.
Starts paper feed from the second feed
station.
Starts paper feed from the 3rd feed station.
Drives toner supply roller.
Drives the relay rollers for the 3rd cas-
sette, cassette bank and the duplex/over-
lay paper path.
Drives black development or color
development units
Drives the rollers of the Duplex/Overlay
section.
Starts paper feed from the 1st feed station.
M1
M2
M3
M4
M5
M7
M6
M8
M9
MC1
MC2
MC3
MC4
MC5
MC6
MC7
MC8
SOL1
P to P
Location
H-5
H-4
H-5
F-5
D-4
D-5
D-5
F-12
F-5
F-7
F-7
F-8
F-8
F-8
F-8
F-6
F-11
F-4
1-22
Summary of Contents for FT4460
Page 1: ...RICOH R I C O H F T 4 4 6 0 RICOH COMPANY LTD...
Page 19: ...SECTION 1 OVERALL M A C H I N E INFORMATION...
Page 29: ...28 February 1989 3 COPY PROCESSES AROUND THE DRUM...
Page 30: ...28 February 1989 4 FUNCTIONAL OPERATION 1 10...
Page 38: ...28 February 1989 7 MECHANICAL COMPONENT LAYOUT...
Page 49: ...SECTION 2 DETAILED SECTION D E S C R I P T I O N S...
Page 136: ...Section 2 Timing Chart following page...
Page 137: ......
Page 138: ...S E C T I O N 3...
Page 158: ...SERVICE T A B L E S...
Page 212: ...REPLACEMENT AND...
Page 334: ...SECTION 12...
Page 399: ......
Page 411: ......
Page 412: ......
Page 413: ......