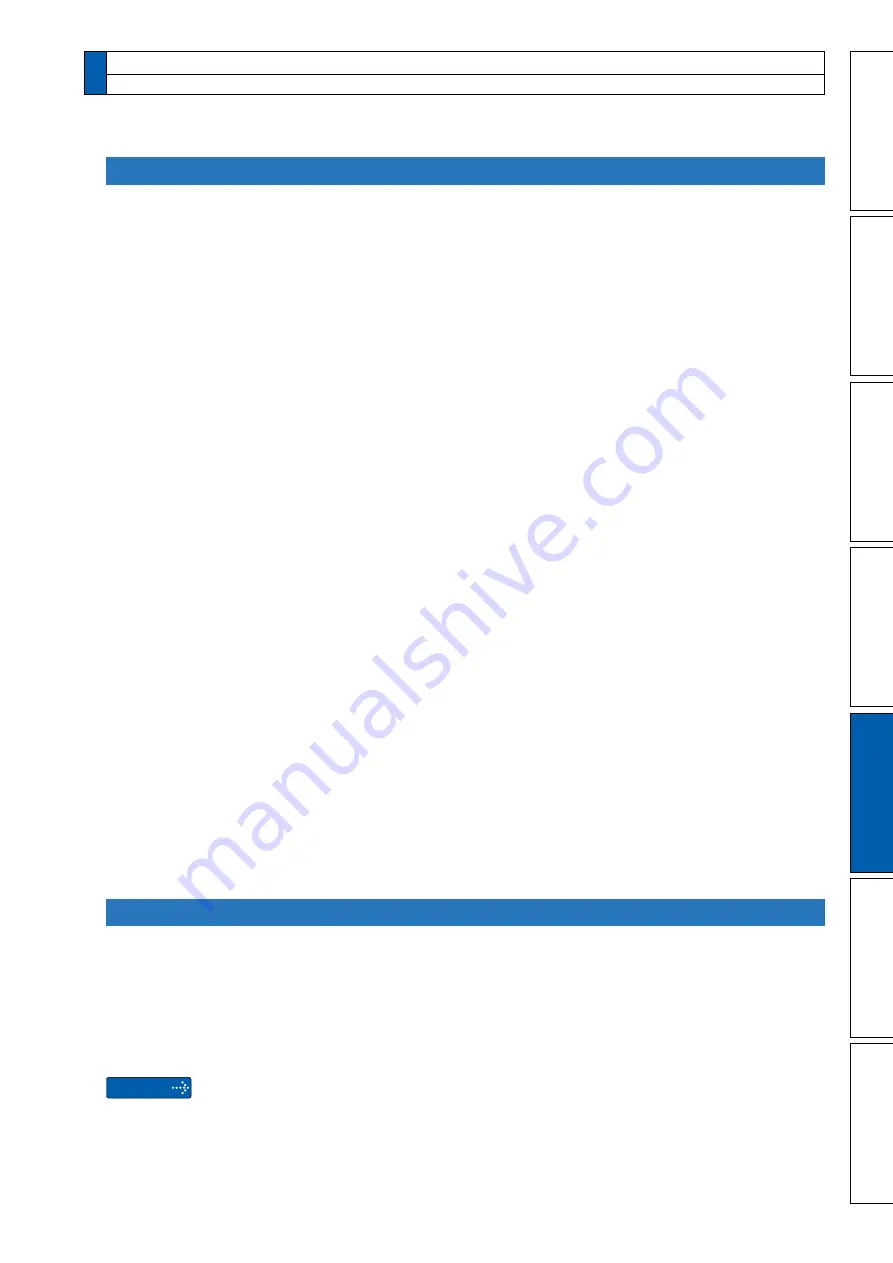
5-25
1
Before Using the Products
2
Preparation
3
Connection
4
Setup
5
Adjustment
6
When in T
rouble
7
Supplement
Caution
(1) Immediately after the first servo-on upon start up; or after increasing Pr0.03
Real-time auto-tuning stiffness setup, abnormal sound or oscillation may be gener-
ated until the load characteristics estimation is stabilized. If such abnormality lasts or
repeats for 3 or more reciprocating operations, take the following countermeasures.
1) Lower the setup of Pr0.03 (Selection of machine stiffness at real-time auto-gain
tuning).
2) Set Pr0.02 Real-time auto-tuning setup to 0 to disable the real-time auto-tuning.
3) Set Pr0.04 Inertial ratio to the calculational value of the equipment and set Pr6.07
(Torque command addition value), Pr6.08 (Positive direction compensation value),
Pr6.09 (Negative direction compensation value) and Pr6.50 (Viscous friction com
-
pensation gain) to 0.
4) Disabale load variation suppression function. (bit1=0 after Pr 6.10 bit14=0).
(2) When abnormal noise and oscillation occur, Pr0.04 (Inertia ratio) or Pr6.07 (Torque
command additional value), Pr6.08 (Positive direction torque compensation value),
Pr6.09 (Negative direction compensation value), Pr6.50 (Viscous friction compensa
-
tion gain) might have changed extreme value.Take the same measures as the above
in these cases.
(3) Among the results of real-time auto-gain tuning, Pr0.04 (Inertia ratio) and Pr6.07
(Torque command additional value), Pr6.08 (Positive direction torque compensation
value), Pr6.09 (Negative direction compensation value), Pr6.50 (Viscous friction com
-
pensation gain) will be written to EE-PROM every 30 minutes. When you turn on the
power again,the auto-gain tuning will be executed using the latest data as initial val
-
ues.
(4) Because the control gain is updated while the motor stops, changed setting value
of Pr0.03 “Real-time auto-tuning stiffness setup” may not be reflected if the motor
cannot stop due to excessively low gain or application of a command that directs the
motor to turn in the same direction continuously. If the changed stiffness setting value
is reflected after motor stops, it may generate abnormal sound or oscillate.
After changing stiffness, stop the motor and check to see that the new stiffness
setting is made effective.
Invalidation of Real-Time Auto-Gain Tuning
Caution
You can stop the automatic calculation of Pr0.04 (Inertial ratio) and invalidate the real-
time auto-gain tuning by setting up Pr0.02 (Real-time auto-gain tuning setup) to 0.
Because the estimation result of Pr0.04 Inertia ratio is recorded, if this parameter be-
comes abnormal value, manually set to the appropriate value which is obtained from suit-
able formula or calculation.
If power is turned off within 30 minutes after the end of tuning process, the result of the
real-time auto-tuning is not saved. If the result is not saved, manually write parameters to
EEPROM and then turn off power.
2. Real-Time Auto-Gain Tuning
Two-degree-of-freedom control mode – Synchronous type
Buy: www.ValinOnline.com | Phone 844-385-3099 | Email: [email protected]