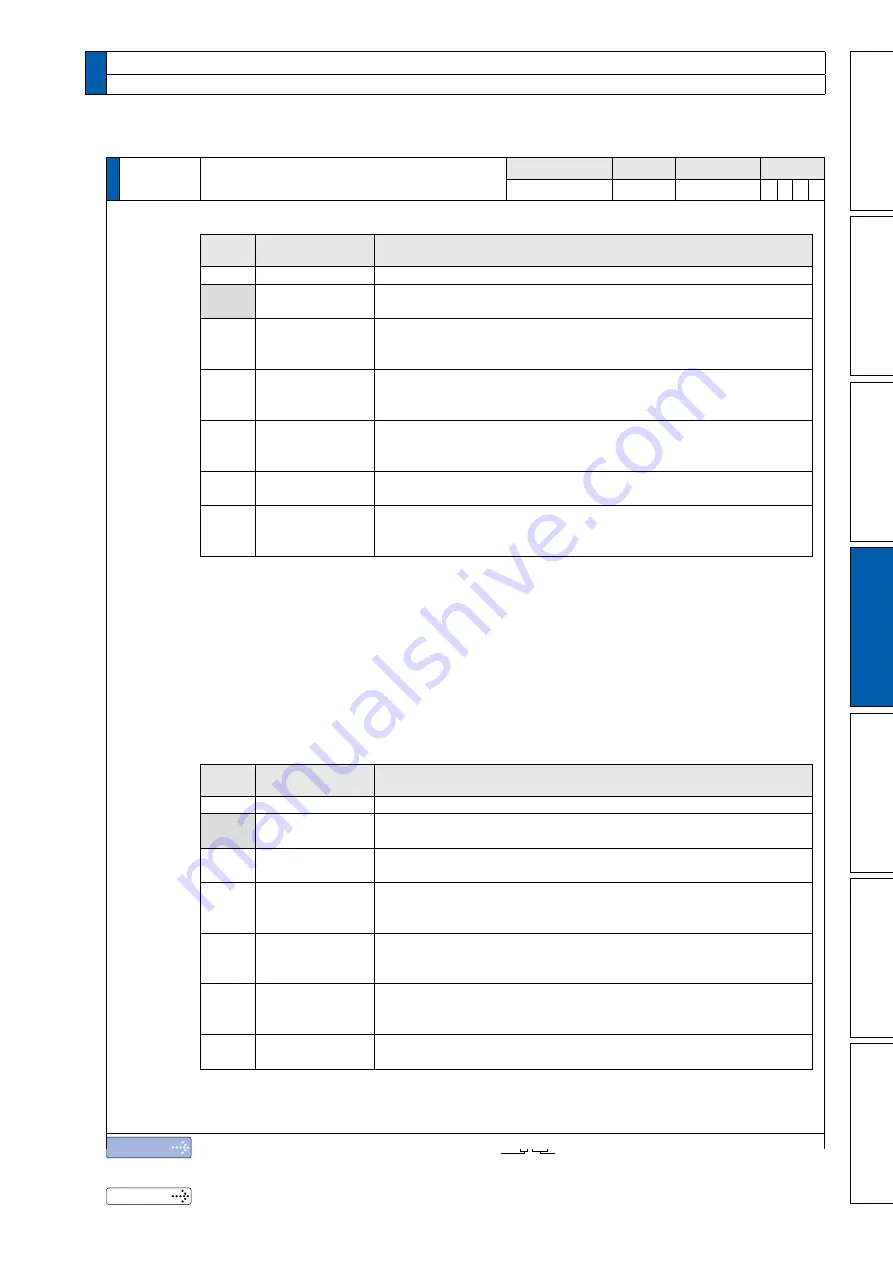
4-7
1
Before Using the Products
2
Preparation
3
Connection
4
Setup
5
Adjustment
6
When in T
rouble
7
Supplement
Note
Related page
• A parameter is designated as follows:
Pr0.00 Parameter No.
Class
• For parameters which No. have a suffix of “
*
”
, changed contents will be validated
when you turn on the control power.
• P.3-32... “Inputs and outputs on connector X4”
Default: [ ]
1. Details of parameter
[Class 0] Basic setting
Pr0.02
Real-time auto-gain tuning setup
Range
Unit
Default
Related
control mode
0 to 6
—
1
P S T F
You can set up the action mode of the real-time auto-gain tuning.
Setup
value
Mode
Varying degree of load inertia in motion
0
Invalid
Real-time auto-gain tuning function is disabled.
[1]
Standard
Basic mode. Do not use unbalanced load, friction compensation or
gain switching.
2
Positioning
*
1
Main application is positioning. It is recommended to use this mode
on equipment without unbalanced horizontal axis, ball screw driving
equipment with low friction, etc.
3
Vertical axis
*
2
With additional features to the positioning mode - use this mode to
positively and effectively compensate for unbalanced load to the
vertical axis or minimize variations in setting time.
4
Friction
compensation
*
3
With additional features to the vertical axis mode - use this mode to
positively and effectively reduce positioning setting time when the belt
driving axis has high friction.
5
Load characteristic
measurement
Estimate the load characteristics without changing current parameter
setting. This mode requires use of the setup support software.
6
Customize
*
4
Functions of real-time auto-gain tuning can be customized to meet the
requirements of the specific application by combining desired functions
according to the Pr6.32 “Real-time auto-gain tuning custom setting”.
*
1 Velocity and torque controls are the same as in the standard mode.
*
2 Torque control is the same as in the standard mode.
*
3 Velocity control is the same as in the vertical axis mode. Torque control is the same as
in the standard mode.
*
4 Certain function(s) is not available in a specific control mode. Refer to description in
Pr6.32.
Two-degree-of-freedom control mode: standard type
For Two-degree-of-freedom control mode, refer to Pr6.47 (P.4-64).
Set up the action mode of the real-time auto-gain tuning.
Setup
value
Mode
Varying degree of load inertia in motion
0
Invalid
Real-time auto-gain tuning function is disabled.
[1]
Standard
Stability-first mode. Do not use unbalanced load compensation, friction
compensation or gain switching
2
Quick response
mode 1
Positioning-first mode. Use this mode for equipment with horizontal
axis, low friction ball screw driving and without unbalanced load.
3
Quick response
mode 2
In addition to the features provided with the Quick response mode 1,
use this mode to compensate unbalanced load, to apply third gain to
reduce variation in positioning settling time.
4
Quick response
mode 3
*
1
In addition to the features provided with the Quick response mode 2,
use this mode to shorten positioning settling time when the load has
high friction.
5
Load characteristic
measurement
Estimate load characteristics without changing basic gain setting
or friction compensation setting with the help of the setup support
software.
6
Fit gain mode
To be used for fine adjustment of rigidity setting after completion of
fit gain.
*
1
Velocity control is the same as in the quick response mode 2. Value of parameters, Pr6.08
Forward torque compensation value, Pr6.09 Backward torque compensation value and
Pr6.50 Viscous friction compensation gain will be updated but not reflected on operation.
(continued)
Buy: www.ValinOnline.com | Phone 844-385-3099 | Email: [email protected]