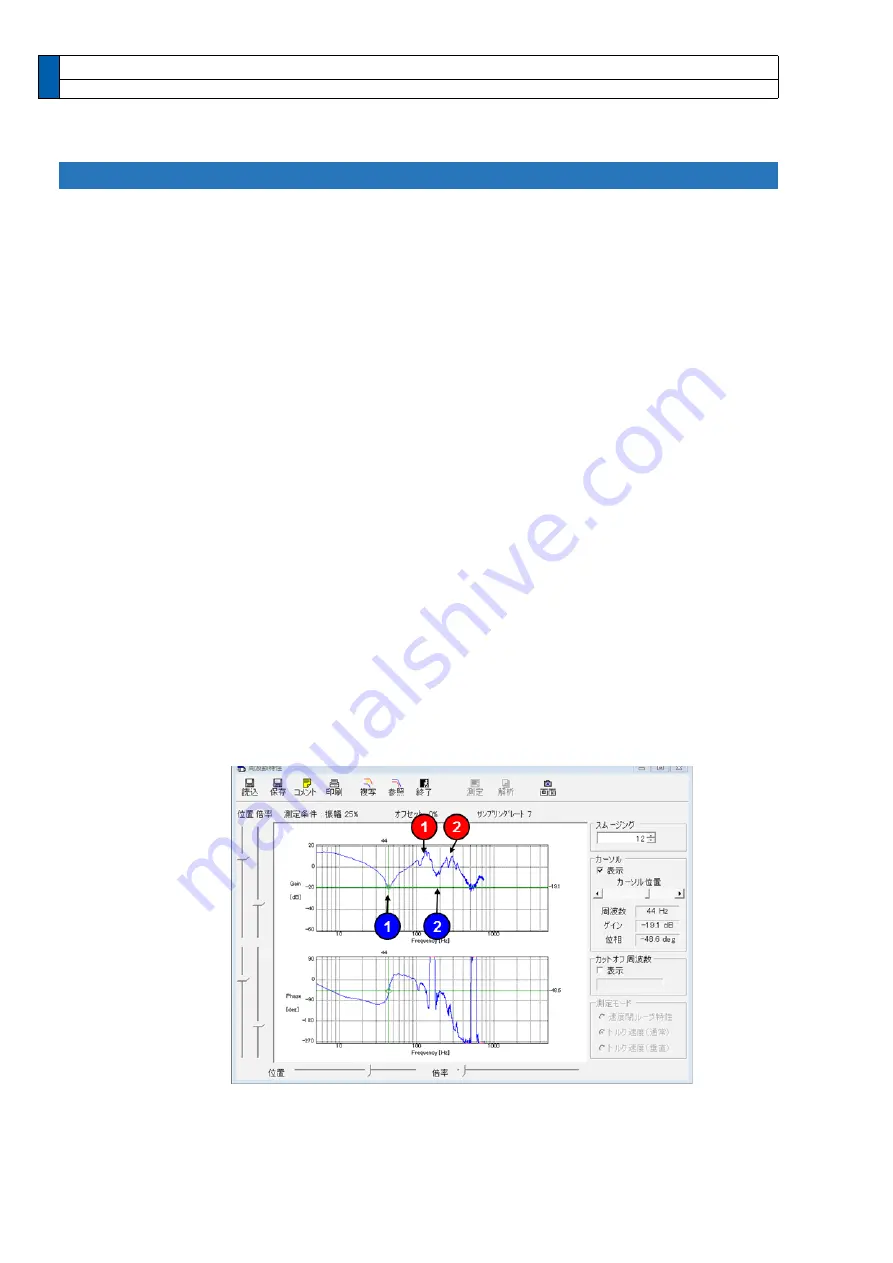
5-46
How to Use
1)
As preparation, measure the resonance frequency and anti-resonance frequency us-
ing the frequency characteristic measuring function of PANATERM with torque veloc
-
ity mode.
Ex.) The figure below shows the measurement result with a belt device. Ignoring
small resonances, the resonance frequency at the gain peak and the anti-resonance
frequency at the gain valley are as follows:
1st resonance frequency = 130 [Hz], 1st anti-resonance frequency = 44 [Hz]
2nd resonance frequency = 285 [Hz], 2nd anti-resonance frequency=180 [Hz]
2) The resonance attenuation ratio and anti-resonance attenuation ratio should have ini-
tial values of around 50 (0.050).
3) The response frequency should start with the same value as the anti-resonance fre-
quency.
4) Specify a value of 4 to 6 in Pr. 2.13 “Damping filter switching selection” to enable
model-type damping control.
5) Activate the motor and fine tune the parameters in the following sequence so that vi-
bration components including command position deviation become small.
(1) Anti-resonance frequency
(2) Anti-resonance attenuation ratio
(3) Resonance frequency
(4) Resonance attenuation ratio
6)
Once the setting where vibration is minimized was found, increase the setup value of
response frequency. The response frequency increases from one to four times the
anti-resonance frequency, and the higher the frequency, the smaller the delay due to
damping control. However, the damping effect decreases gradually, so a balanced
setting should be chosen.
Example of frequency characteristic measurement with setup support software PANATERM
5. Manual Gain Tuning (Application)
Model type resonance oppression notch filter
Buy: www.ValinOnline.com | Phone 844-385-3099 | Email: [email protected]