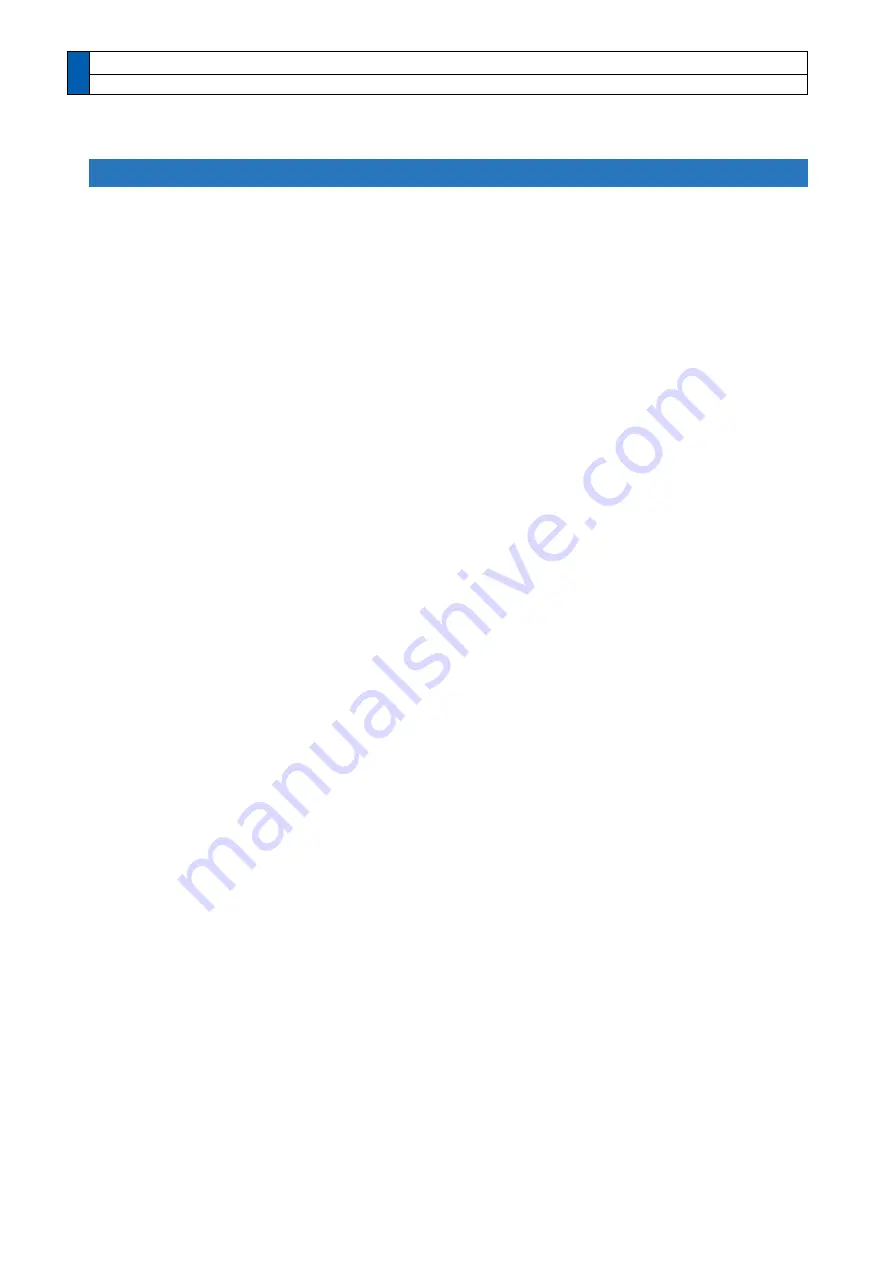
5-52
How to Use
There are two methods below for adjusting the load variation suppression function.
■
When there is no load inertia variation (disturbance suppression setting)
1) Make normal gain adjustment in advance.
Use real-time auto tuning (Pr 0.02=1) with the load variation suppression function au-
tomatic adjustment disabled (Pr 6.10 bit14=0), and set stiffness (Pr 0.03) as high as
possible.
2) Set bit14 to 1 in Pr 6.10 “Function expansion setting” to enable the load variation sup
-
pression function automatic adjustment, and check disturbance suppression effect with
the motor rotate.
* Before enabling or disabling the load variation suppression function, turn off the
servo first.
* If this change causes the motor to oscillate or generates an abnormal sound, return
to Step [1] and decrease the servo rigidity by one or two levels before repeating the
subsequent steps.
3) If further aims to adjust, set bit14 to 0 in Pr 6.10 to disable the automatic adjustment of
load variation suppression function.
4) Specify a small value as possible in Pr 6.24 “Load variation compensation filter.”
Decreasing the filter setup value within the range that does not produce any significant
abnormal sound or torque command variation will improve disturbance suppression
performance and reduce motor velocity variation and encoder position deviation.
* When an abnormal sound at high frequency (1 kHz or above) is generated, increase
the value in Pr 6.76 “Load estimation count.”
* When vibration at low frequency (10 Hz or below) is produced after operation stops,
increase the value in Pr 6.23 “Load variation compensation gain”.
* No change is required for Pr 6.73 “Load estimation filter” in normal cases, but you
can set the optimum point by fine-tuning within the range between around 0.00 and
0.20 ms.
■
When there is load inertia variation (load variation stabilization setting)
1) Turn ON the control power in two-degree-of-freedom position control (synchronization
type) (Pr 0.01=0, Pr 6.47 bit0=1 bit3=1).
2) Set the command response filter (Pr 2.22) to 10ms.
3) Set real-time auto tuning to load variation support mode, and operate the motor in a
pattern as large as possible load variation occurs in this state.
4) Set the stiffness setting (Pr 0.03) as large as possible.
5) Set the command response filter to appropriate value to continue to derease while
checking response of the motor. (*In case of need to the multi-axis trajectory control,
change all axes Pr 2.22 to the same value and adjust.)
5. Manual Gain Tuning (Application)
Load fluctuation control function
Buy: www.ValinOnline.com | Phone 844-385-3099 | Email: [email protected]